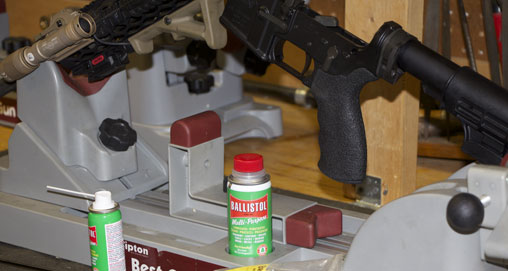
More than 100 years ago, the Imperial German Army was looking for an all-purpose oil with which to outfit its soldiers. The army wanted oil that could maintain the metallic parts on rifles, but could also be used to condition both the wooden stocks on rifles and the leather gear carried by its troops. In addition, this oil had to be safe enough to treat minor wounds, sores and scratches.
Dr. Helmut Klever, a chemistry professor at the Technical University of Karisruhe, believed he could develop a new type of oil that would meet these stringent demands. Klever also happened to be the son of the founder of Klever Company, a producer of oils and grease from coal.
In 1904, Klever introduced Ballistol, which the army tested and adopted in 1905. For the next 40 years, Ballistol was issued to Imperial Army troops as a general, all-purpose oil with a multitude of functions.
Ballistol, in its original formula, is available in both liquid and aerosol form, containing no ingredients that are carcinogens or considered hazardous by OSHA. At the same time it removes carbon and minute amounts of lead and copper, all while protecting metal parts from corrosion.
“With Ballistol you only need one product,” said Patrick Palumbo, National Sales Manager for Ballistol USA. “Once shooters use it, they want to tell their friends about it.”
Ballistol can also be mixed with water to form an alkaline emulsion for flushing blackpowder firearms or when using corrosive ammunition. Ballistol recommends a 3-to-1 water/Ballistol mixture as a blackpowder solvent and a 10-percent mixture for corrosive ammunition. The alkaline mixture neutralizes the acidic nature of the propellants. Ballistol can even be used to protect wet firearms and gear because the oil doesn’t cover water. Instead, it mixes with the water and allows it to evaporate, leaving the oil behind.
Of course, it is easy to make such claims when the oil is being tested in the controlled confines of a lab. It’s often much harder for products to perform the same way in field situations, though 40 years of military use, provides some degree of proof.
To test the company’s claims, two firearms-a DPMS AP4 Carbine in 5.56x45 mm and a Remington 783 in .30-06 Sprg.-were chosen to test the product’s viability against two popular platforms, hunting and high-volume training. Both firearms were thoroughly cleaned before heading to the range.
To begin, I sighted the 783. It took 12 rounds of Remington 125-grain Managed Recoil loads to ensure the rifle was in the bullseye. The box was then finished with some off-hand shots for fun and to make sure the bore was good and dirty.
At the shop, I followed the recommended of soaking the bore with Ballistol, and allowing it to sit for 10 minutes. Next was a vigorous scrubbing with a brass brush before pushing through a couple of saturated patches on a standard jag. Copious amounts of fouling dyed the first patch completely black with powder residue. The second patch picked up what the first left behind, turning gray with just a streak or two of green. A second application of the brush, followed by more patches, removed more fouling, but considerably less than the first round. Another series of soaking, brush and patches brought out a little more copper green, but no black, leaving the bore clean and oiled.
The DPMS was used in a training session that included a multitude of drills and 125 rounds sent downrange, a fairly standard count for both competition and training sessions.
Again the bore was coated with Ballistol and allowed to work on the fouling. The session produced similar results to the 783, though it required more applications of the brush and a dozen or so more patches to duplicate the results. Vast amounts of black carbon appeared on the patches, followed by small amounts of green copper.
While Ballistol did a good job on carbon, it was difficult to determine its effectiveness on copper. Some was obviously removed, as shown by the green on the patches, but exactly how much copper was lifted away could only be determined by an application of a copper specific solvent.
After a soaking of copper solvent and a brush, the patches popped out green from the barrels of both rifles. The patches, however, weren’t completely saturated with the color, though the DPMS was significantly more emerald than the 783. A second application showed the patches almost pale, and resulted in both bores showing no signs of fouling of any kind, just well-cleaned barrels.
Throughout testing, Ballistol worked pretty close to advertised. Mixing it with water produces an emulsion that can be used as a flush. When allowed to evaporate, the mixture leaves behind an oily residue. Straight Ballistol removes carbon with no more work than other solvents, all while inhibiting the barrel with a rust-resistant barrier of oil. It even removes some copper. But then, the company never claimed it would remove all copper. In addition, Ballistol was easy on the hands, with no signs of issues that are so common when using harsh chemical solvents without latex gloves.
Ballistol has a lot of uses, and makes a lot of claims. For the most part, the product lives up to those claims. It cleans, lubricates and conditions a variety of gear, including firearms. And from the color, it would provide a nice oil-stained sheen on an unfinished stock.