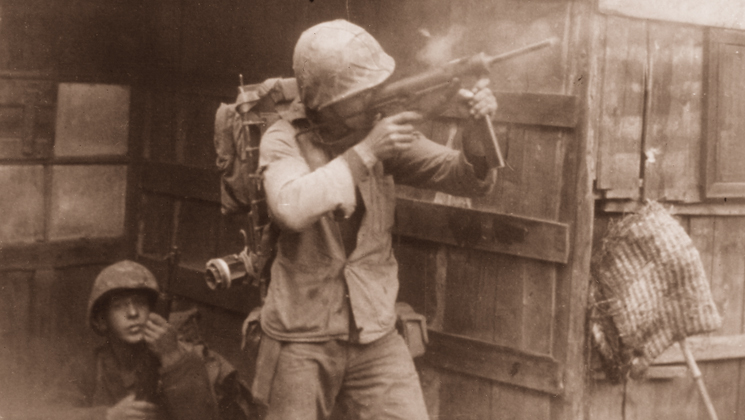
This article was first published in American Rifleman, September 2005
At the time of America’s entry into World War II, the standard U.S. military submachine gun was the famous Thompson M1928A1.While a reliable and effective submachine gun, the Thompson had several disadvantages as a military arm. Among its biggest drawbacks was the fact it was expensive and time-consuming to manufacture. To address that, the U.S. Army Ordnance Department initiated the development and adoption of a simplified version of the Thompson that featured many manufacturing shortcuts. The new variant, standardized as the “U.S. Submachine Gun, Cal. .45, M1,” dispensed with the unnecessary and over-engineered Blish locking system of the M1928A1 Thompson. The Cutts compensator was also eliminated, and the cocking handle was moved from the top of the receiver to the right side. The M1 Thompson was followed by the even more simplified M1A1 variant, which featured a fixed firing pin instead of the separate hammer-actuated firing pin of its predecessor.
While the M1 and M1A1 Thompsons could be manufactured much more cheaply and quickly than the M1928A1, they still required a substantial amount of machining work. The Ordnance Department recognized that the basic Thompson design had been simplified as much as possible, and a totally new type of submachine gun would be required to meet burgeoning wartime demand. Both our allies and adversaries had previously addressed that issue by developing and adopting submachine guns that made extensive use of stamped and welded sheet-metal parts rather than costly and time-consuming forged steel components. The German MP40 outwardly resembled its MP38 predecessor, but it was welded together from stamped sheet-metal components. The British developed and standardized the Sten submachine gun, which took the use of stamped and welded parts even further. While less aesthetically pleasing than traditional arms made of wood and forged steel, such submachine guns offered an attractive combination of reduced production time and lower manufacturing cost.
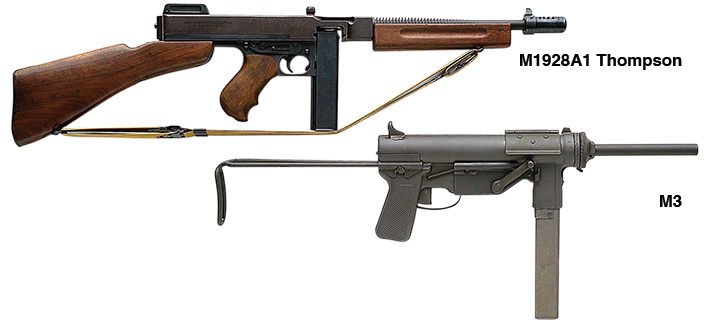
The U.S. Army Ordnance Department considered several designs for low-cost/high production-rate submachine guns fabricated from stamped and welded sheet metal. A design developed in large part by George Hyde, with the assistance of General Motors’ Inland Manufacturing Division, was given the prototype designation of T-15. It was chambered for the standard .45 ACP cartridge and featured a sliding wire stock, which substantially reduced its length when retracted. Army Ordnance Col. René Studler was an ardent proponent of the new submachine gun and was instrumental in its subsequent adoption. The T-15 prototype was refined and superseded by the T-20. Unlike the selective-fire T-15, the T-20 only fired in the full-automatic mode.
The T-20 had number of advantages as compared to most other submachine guns, including the fact that its internal parts were fully enclosed, which reduced the possibility of the mechanism being clogged by dirt, mud or sand. In addition, it was designed with rather generous dimensional tolerances to allow functioning even when subjected to extreme dust or mud conditions. The bolt traveled along two steel guide rods, which prevented contact with the inside of the receiver and resulted in increased reliability and smoothness of operation. The gun could be quickly disassembled, and the barrel and bolt were easily removed. It did not have a conventional safety, but the ejection port cover prevented accidental firing when closed.
The T-20 prototype was extensively tested at Aberdeen Proving Ground and proved to be more reliable in the mud and dust tests than any other submachine gun ever tested by the U.S. Army. In addition to the Army’s Infantry Board, the new submachine gun was evaluated by the Airborne Command and Armored Forces Board. These latter two organizations were especially interested due to its compactness, which had obvious advantages for airborne use or in the cramped confines of a tank.
After conclusion of rigorous testing, the T-20 was recommended for adoption in December 1942 as the “U.S. Submachine Gun, Caliber .45, M3.” Official approval came on Jan. 11, 1943. Shortly after formal adoption, a contract was awarded to General Motors’ Guide Lamp Division for 300,000 M3 submachine guns. The Guide Lamp plant, located in Anderson, Ind., had extensive experience in the fabrication of stamped metal components, so it was a logical choice to manufacture the new submachine gun.
Following initial price adjustments, the contract price for each M3 submachine gun, less the bolt assembly, was set at $18.36. Production of the bolt was subcontracted to the Buffalo Arms Co. at a price of $2.58, which brought the total per-unit cost of an M3 to $20.94. This was about half the cost of the simplified M1A1 Thompson. The M3 also had the great benefit of a much faster production rate than the Thompson. Other than the bolt, the only major component of the M3 that required any degree of machining was the barrel, which was rifled by the efficient cold swaging method. The exterior metal surfaces were Parkerized, a provision was made for a cylindrical oiler on the left side of the receiver, and the sling swivels were welded on the gun. In order to keep costs down and simplify logistics, the same oiler and sling used with the M1 Carbine were standardized for use with the M3 as well. The front end of the wire stock was threaded to allow its use as a cleaning rod.
The M3 fired fully automatically at the rate of about 400 r.p.m. from a 30-round detachable box magazine. This relatively slow rate of fire aided in controlling it and permitted an experienced user to easily fire single shots with proper trigger manipulation.
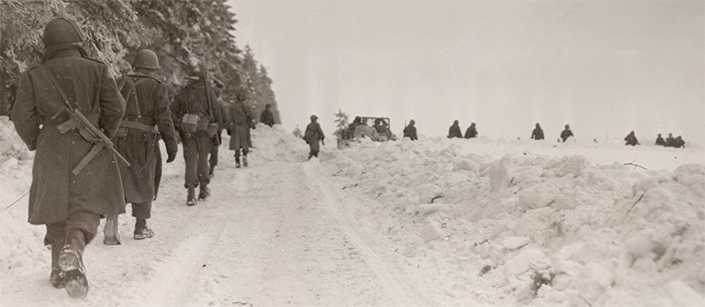
Less than six months after its adoption, the first M3 submachine guns came off of Guide Lamp’s assembly line in May 1943. This was a very brief period of time as compared to most other military arms, which are typically in development for a number of years. Despite the simplicity of the stamped and welded sheet-metal construction, there were the normal production glitches. One of the most troubling problems was that the heat generated from welding together the two stamped receiver halves tended to warp the metal. This and other production difficulties were eventually corrected, but production lagged behind initial projections. It was envisioned that some 20,000 M3 submachine guns would be produced by July 1943, but the actual production was only 900 guns by that date. This delay in delivery of sufficient quantities resulted in contracts for additional M1A1 Thompsons until the supply of M3s could meet the demand.
When its production problems were solved, M3 manufacture rapidly increased, and the gun began to be issued to the using services. Among the first combat operations in which the M3 saw use was in the hands of some paratroopers of the 82nd and 101st Airborne Divisions during the Normandy drop as part of the D-Day invasion. Initially, many soldiers who were issued “grease guns” were not impressed with them and were reluctant to give up their trusted Thompsons. However, as the M3 began to see combat use, its reliability and lighter weight were seen as positive attributes, and most G.I.s, albeit grudgingly, came to accept the roughly hewn grease gun as a worthy successor to the finely crafted Thompson.
Another problem with some of the M3s became evident in early 1944 when complaints were forthcoming from training camps regarding the propensity of the side-mounted cocking handle to break. This was caused primarily by the use of low-grade steel and improper heat treatment. Other less serious problems were reported regarding the barrel ratchet pad and the durability of the rear sight. Also, the magazine release could be accidentally depressed, so a metal guard was developed to correct that problem. These various deficiencies were rectified as soon as they were identified, and later production versions of the M3 grease gun were quite reliable in service.
Even though the M3 was an uncomplicated design, it was believed that it could be simplified and improved even further. Guide Lamp was directed by the Ordnance Department to come up with an improved design. The firm developed an even more simplified grease gun, designated as the M3E1. Six prototype models were fabricated and tested in April 1944. The most significant changes to the M3E1 included:
- Elimination of the side-mounted cocking handle, to be replaced by a recess in the bolt that permitted the bolt to be withdrawn by merely inserting a finger and pulling it to the rear. This required an enlarged ejection port.
- Strengthening of the rear sight by welding support ribs to both sides. This feature had previously been added to later production M3 submachine guns.
- Elimination of the separate oiler on the left side to be replaced by a larger internal oil reservoir housed in the grip.
- Modification of the wire stock to allow its use as a wrench to remove the barrel and also permit it to be utilized as a magazine
loading tool.
After testing, the M3E1 was found satisfactory and it was standardized on Dec. 21, 1944, as the “Submachine Gun, Caliber . 45, M3A1.” Upon standardization of the M3A1, the M3 was reclassified as “Limited Standard.” This meant the M3 would no longer be manufactured, but those already in service would remain in use. Since the new M3A1 was adopted and put into production very late in the war, the M3 was the only variant to see any significant combat service in World War II. A total of 606,694 M3 and 15,469 M3A1 submachine guns were manufactured during World War II.
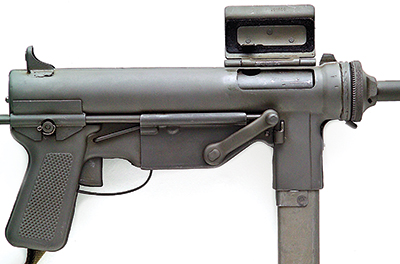
Several interesting accessories were developed for use with the grease gun. During World War II, the Office of Strategic Services (OSS)—forerunner of today’s Central Intelligence Agency (CIA)—required a silenced or suppressed submachine gun for certain clandestine operations. A suppressor for the grease gun was developed by Bell Laboratories with High Standard Mfg. Co. and Guide Lamp as subcontractors. One thousand of these suppressors were reportedly produced and saw limited use during and after the Second World War.
There was also a request for a conversion kit to permit the grease gun to fire 9 mm rather than the standard .45 ACP round. This would allow it to be used by partisans and OSS operatives who had only British or captured German ammunition. The design of the grease gun made it easy to switch from .45 to 9 mm by simply replacing the barrel, bolt and inserting a magazine adapter to allow use of the British Sten magazine. It was originally envisioned that some 25,000 of the 9 mm conversion kits would be manufactured, but only about 500 are believed to have been made in late 1943 and early 1944. Virtually all of these 9 mm conversion kits were made for the M3 rather than for the M3A1.
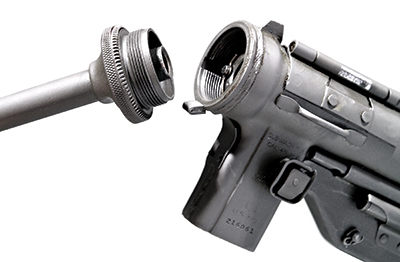
A funnel-shaped flash hider that clamped on the end of the barrel was developed. The flash hider, designated as the T-34, was made only in prototype numbers during World War II, but it was put into production in the early 1950s and standardized as the “Hider, Flash, M9.”
Initially, the three-cell canvas magazine pouches made for the 30-round Thompson SMG magazines were used with the grease gun magazines. However, a slightly different three-cell pouch was subsequently manufactured and widely issued for the grease gun magazines.
In early 1945, it was recommended all Thompsons in use be replaced by the M3/M3A1, but this was not accomplished before the end of World War II. In fact, limited numbers of Thompsons remained in the U.S. military inventory until the late 1950s, although the number on hand was far exceeded by the number of grease guns. World War II ended with the M3/M3A1 firmly established as the U.S. military’s front-line submachine gun, and it saw extensive service during the Korean War. As was the case previously, the grease gun proved that production cost and cosmetic considerations had no bearing as to the utility or effectiveness of a combat arm.
In order to augment the supply of submachine guns, a contract was awarded to the Ithaca Gun Co. circa 1954 for the manufacture of 70,000 M3A1s. Production did not get under-way until 1955, by which time the pressing need for additional submachine guns had passed. The Ithaca contract was cancelled after 33,227 M3A1s had been manufactured. Except for markings, the Ithaca M3A1 was virtually identical to the World War II Guide Lamp M3A1.
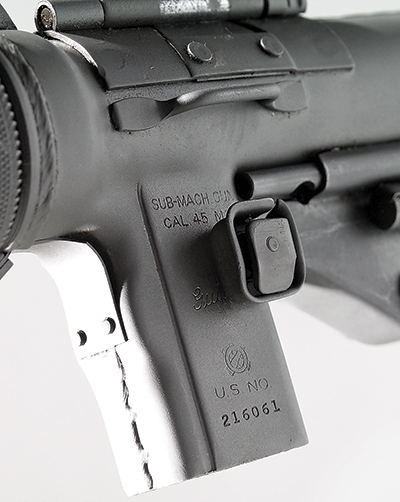
Several foreign nations adopted submachine guns that were almost direct copies of the grease gun or were at least heavily based on it. These nations included China, Argentina and Portugal.
Following the Korean War, the M3 and M3A1 submachine guns remained a mainstay of the U.S. military arsenal. Grease guns saw some use by American troops in the early years of the Vietnam War, and large numbers were supplied to various friendly indigenous personnel during the course of the conflict. The grease gun continued as part of the U.S. military’s arsenal and has been used in virtually all U.S. military conflicts since World War II. Some silenced M3A1 submachine guns were utilized in several post-Vietnam military operations including Operation Eagle Claw, the ill-fated rescue attempt of the American hostages in Iran in the spring of 1980.
M3 and M3A1 submachine guns remained in service in the U.S. armed forces, mainly as armament for armored vehicle crewmen. They saw use during the Gulf War in the early 1990s, and limited numbers of grease guns are reportedly still being utilized in the Iraq and Afghanistan campaigns even today.
Original M3 and M3A1 grease guns are surprisingly uncommon on the collector market today as compared to other U.S. submachine guns, such as the Thompson and Reising. Their long tenure of service meant that the vast majority remained in Uncle Sam’s inventory, thus, few were properly registered and available for sale on the civilian market. Today, an original registered and transferable grease gun will typical sell for as much as, or more than, a World War II Thompson.
From the time of its inception, the M3 submachine gun was often considered a cheaply made and inferior replacement for the finely crafted Thompson. However, the grease gun was a portent of things to come regarding military arms. The finely crafted designs of previous eras were correctly viewed as unnecessary extravagances in wartime, when cost, rate of production and reliability trumped aesthetic considerations. The grease gun may have been ugly in the eyes of some, but it was inexpensive to make and functioned very well. The fact that its venerable predecessor—the Thompson submachine gun—has been long relegated to being a museum piece while the ugly duckling grease gun is still seeing some use in combat zones today speaks volumes as to the excellence of its humble design.