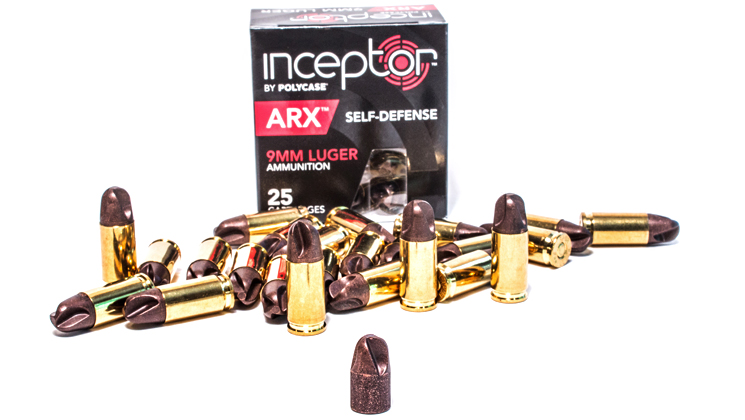
Many of the new products rolling out onto the shooting market each year are variations or improvements of existing designs. But once in a while, something unique arrives. Earlier this year, I had the opportunity to travel to Savannah, Ga., and meet with the team at PolyCase Ammunition to learn more about the company’s fundamentally new approach to bullet design and manufacturing.
The ARX bullet came about in the pursuit of creating single-use ammunition for national security forces. In many countries, terrorist organizations and cartel members pick up spent brass cartridge cases (the single most difficult ammunition component to obtain) that were left behind by government security forces, and reload them with homemade lead bullets and propellant extracted from fireworks. Starting in 2011, retired Lt. Col. Paul Lemke teamed with Juan Carlos Marin, an engineer from Spain, to develop a nylon-based cartridge case that can be loaded only one time. Thus the company name of PolyCase. The firm’s first success was a .380 ACP cartridge case with a zinc-alloy base and nylon body.
The nylon and polymer materials in these cases, however, do not work reliably with conventional, copper-jacketed, lead-core bullets. So, the team at PolyCase had to devise a projectile containing enough polymer to function reliably in the nylon cases. This lead to the development of the Inceptor line of bullets.

Unlike conventional jacketed bullets, which require several steps and a good deal of heavy equipment to shape, Inceptor bullets are made by the high-pressure injection molding of a heated blend of powdered copper and epoxy/polymer resin. After it cools a bit, the mold opens and a cluster of bullets fall onto a conveyer belt to be collected and smoothed before loading. The excess molding material (called sprue) is ground up and reused. Injection molding is fast and efficient, allowing for high production volume with very little waste.
The result is a lightweight projectile with several desirable qualities. The bullets are lead-free, allowing them to be used in jurisdictions and facilities that restrict or ban the use of lead-based ammunition. The polymer/copper material maintains its integrity as it travels down the barrel and strikes soft targets, but it fractures when it hits hard targets such as steel plates or building materials—greatly reducing the chance of ricochets. After the bullets have been fired, the copper can be reclaimed by heating the bullet fragments to burn off the polymers.
It’s a fairly straightforward process to make solid, round-nose bullets using the injection-molding process. However, the polymetallic blend of materials does not lend itself to the production of the hollow-point bullets commonly used for self-defense. The formulation has to be tough enough to survive loading, firing and flight into the target, which means it’s too hard to expand on impact. With that in mind, PolyCase went back to the drawing board once more to find a way to manufacture a non-expanding bullet with effective terminal ballistics comparable to a hollow point.
The end result of the company’s R&D is the ARX bullet, a patent-pending design that takes full advantage of the flexibility provided by injection molding. PolyCase ballistics engineers—along with third-party aerospace and fluid engineers—spent months experimenting with aero and fluid dynamics using Finite Element Modeling (FEM), which led to the design of uniquely shaped flutes, or channels, the company calls Power Blades. The flutes act to displace the target material using the bullet’s forward and rotational momentum, or “lateral force dispersion.”
Imagine an outboard boat motor running at full speed with the propeller blade suspended in the air above the surface of a lake. The blade’s fast rotation might generate a bit of a breeze but not much else will happen. Now imagine plunging that spinning blade into the lake. It would cause quite a splash as the kinetic energy is dispersed into the water, a much denser medium than air.
The ARX bullet functions in a similar fashion. As the bullet spins through the atmosphere, the flutes do little to disrupt the air it passes through. But as the bullet comes into contact with a fluid medium, such as 10 percent ballistic gelatin, the fluid within the target is suddenly and forcefully churned by its flutes. The fluids are thrust out and away from the bullet at velocities that are anywhere from one-and-a-half to two times faster than the velocity the bullet is traveling.
For example, if a 74-gr. 9 mm Luger ARX bullet is traveling 1450 f.p.s., the fluids will move through the flutes and away from the bullet at somewhere between 2175 to 2900 f.p.s. When the ARX bullets are launched at rifle velocities, the effect is amplified. Firing a .45-cal., 140-gr. projectile from a .458 SOCOM cartridge at 2500 f.p.s. generates fluid displacement at velocities ranging from 3750 to 5000 f.p.s. Due to the law of energy conservation, this increase in fluid speed also creates a decrease in pressure (known as the Venturi Effect), which, in turn, increases the effect of cavitation. Thus the terminal effects of the ARX bullet in a fluid medium include the production of a large temporary cavity, a generous permanent cavity and deep penetration without bullet deformation.
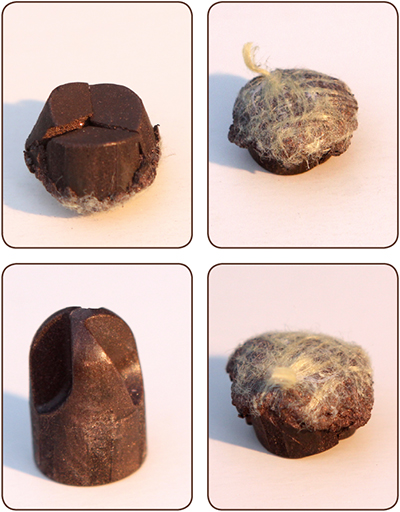
As it turns out, PolyCase bullets function reliably in either the company’s proprietary polymer cartridge cases or in industry-standard brass cases. Rather than wait until the polymer cases are ready for market, the company opted to introduce the shooting public to its unconventional approach to bullet making by launching the Inceptor lines using traditional reloadable brass cases. As of this writing, Inceptor ammunition is available in round-nose (RNP), defensive (ARX), and tracer (FireFly) configurations for .380 ACP, 9 mm Luger, .40 S&W, and .45 ACP pistols—with more chamberings on the way.
Everything I learned at the factory appeared promising, but what I really wanted was to see the ammunition in action. PolyCase obliged by providing the media members in attendance a good deal of trigger time at local indoor and outdoor shooting ranges. At the indoor range, we fired hundreds of rounds through dozens of guns in all of the available pistol calibers along with the .458 SOCOM load through rifles.
Firing the relatively lightweight bullets produced notably reduced levels of felt recoil, especially in pocket-size, concealed-carry pistols. The PolyCase loads ignited without the choking clouds of smoke that accompany some brands of ammunition. Downrange accuracy was on par with other premium defensive handgun loads.
But the number one question with any new type of ammunition is: Will it function reliably? The PolyCase ammunition I fired in a variety of calibers and all tested firearms fed, fired and ejected without any malfunctions. We then did some shooting with sound suppressors. Again, no problems occurred. Lastly, the company broke out a couple of submachine guns for full-automatic fire. That test proved that the Heckler & Koch MP5 select-fire submachine gun had no troubles digesting PolyCase ammunition.
At the outdoor range, we took turns firing single ARX rounds into calibrated 10 percent ballistic gelatin with and without cloth barriers, a Class 2 bullet-resistant vest, and informal targets including water jugs and watermelons.
The ballistic gel results were impressive, demonstrating terminal effects comparable, or superior, to typical hollow-point pistol ammunition. Because the bullet retains its original shape on impact, the ARX is not significantly affected by layers of fabric or intermediate barriers. As a result, it provides deep penetration like other non-expanding bullets. However, when the ARX was fired into a bullet-resistant vest, it fractured and stopped before penetrating the vest’s Kevlar plate.
The permanent wound cavities in the gel exhibited an unusual three-pronged shape—as if a spinning blender blade had passed through the block. The bullets continued to penetrate after they stopped spinning, often flipping over so that their flat base was facing forward by the time they came to a stop. In most cases, the only evidence to be found that the bullets recovered from the gel had been fired were the rifling marks.
The terminal effects of the ARX bullet become even more pronounced with greater velocity. Firing a .458 SOCOM cartridge into bare gelatin caused about 10" of the 16" gel block to blow apart. After causing such massive damage, the bullet broke apart inside the gel block with the fragments creating multiple secondary wound channels. In short, rifle-velocity ARX bullets are simply devastating. Shooting into water jugs and melons produced a similar effect. They didn’t just split or break open, they exploded.
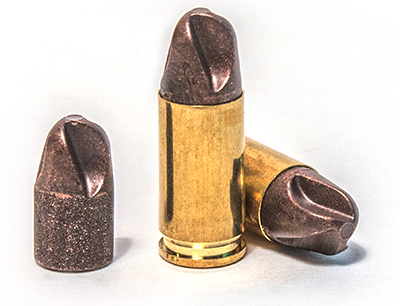
Since attending the PolyCase writers event, I’ve had the opportunity to fire more ARX ammunition in additional test guns. It continues to perform flawlessly with respectable accuracy and reduced levels of felt recoil. The company recently introduced a .50 Beowulf ARX load in conjunction with Alexander Arms, and more new cartridges are expected soon, including .38 Spl. and .223 Rem.
The PolyCase ARX bullet is just one of several innovations this new company plans to bring to market. Just as Glock’s polymer-frame pistols inspired critics to pontificate at length when they arrived on the U.S. market 30 years ago, I expect some folks will be skeptical about adopting injection-molded bullets for target practice and self-defense. Based on what I’ve seen so far, the ammunition lives up to the hype. My hope is that the shooting community will give this exciting new bullet design, and the company producing it, a chance to grow. To learn more, visit polycaseammo.com.