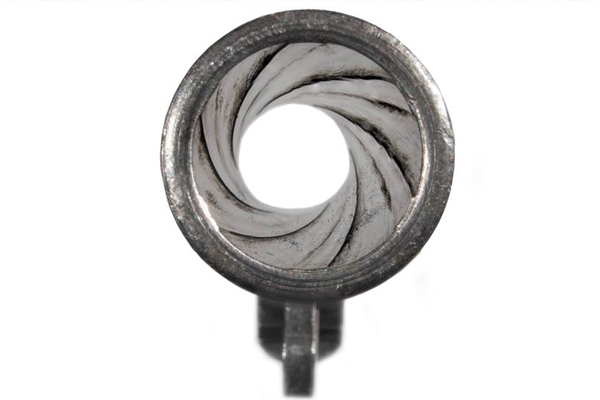
Rifling takes the form of one or more lands and grooves of differing widths, profiles, arrangements and twist (turn) rates. The spiral depressions in the bore surface between the lands are called the grooves; the lands are projections on the bore surface between the grooves. Land diameter is taken as the diameter of the circle formed by the top of the lands, and groove diameter is taken as the diameter of the circle formed by the bottom of the grooves.
The difference between these two dimensions is the groove depth. This is normally around 0.005" to 0.010". The groove depth selected depends upon the type of bullet to be fired in the barrel. For example, muzzleloading firearms and cartridge arms intended for lead bullets normally have deeper grooves than cartridge arms for jacketed bullets. Groove diameter is usually the same diameter as the bullet that is to be used (e.g., 0.308" diameter bullets are intended for a groove diameter of 0.308").
Width
The width of the lands and grooves depends upon the preferences of the barrelmaker and/or customer. Normally, land width is less than groove width.
Number
The number of lands and grooves may vary from one to 20 or more, depending on the preferences of the barrelmaker and customer. Most common are four, six or eight lands and grooves. Barrels with more than eight lands and grooves are sometimes called “multigroove” or “microgroove” types. An even or uneven number of lands or grooves may be used.
Profile
Lands and grooves will be found with differing profiles or shapes. The most popular profile is the type with sharp corners on the shoulders of the lands and grooves. This type of profile is often called “conventional” rifling. However, other profiles such as polygon, sloped or ratchet-edged, semi-polygon and others will be encountered.
There are five barrel-rifling methods in general use: cut, button, broach, hammer forging and ECM (electrolytic cationic machining). All have their benefits.
Cut Rifling
Cut rifling is the oldest method of rifling a gun barrel. The cut-rifling method removes metal from the surface of the bore to create the grooves using a single-bladed, hook-type cutter of groove width that is pulled through the cold barrel. It is sometimes called “hook rifling” after the fishhook-shaped cutter used. Cutter depth is adjustable, so that it removes only a small amount of metal on a pass. Each groove must be cut individually with multiple passes of the cutter. The cutter is indexed to each groove in turn and positively rotated by the rifling machine using a sine bar.
Advantages:
- The shape and number of grooves and groove depth can be easily changed as necessary.
- Rifling twist rate may be easily changed as required.
- Rifling twist is consistent from one end to the other.
- Little or no additional stress is imposed on the barrel.
- Cut-rifled barrels may be contoured after rifling.
- Close tolerance can be held.
Disadvantages:
- The process is slow and not well adapted to mass production.
- Cut barrels normally cost more due to the slower manufacturing process.
- Some metal alloys can not be cut.
- A mistake or machine malfunction at the end of the process can prove wasteful.
- Cut-rifled barrels must be lapped.
Many target shooters prefer cut-rifled barrels for their uniformity and close tolerance. The cut-rifling method is normally used on prototype or test barrels where only a small number will be made to experimental purposes.
Button Rifling
Button rifling is a modern method that creates the grooves in the cold surface of a rifle bore by displacing metal utilizing a bullet-shaped, superhard button of tungsten carbide. The rifling button has the reverse pattern of the groove profile ground into its surface. As the rifling button is pushed or pulled through the barrel, the groove pattern is ironed into the bore surface by displacement. There are several variations in button rifling procedure. Some barrelmakers prefer to pull the button through the bore while others prefer to push it through. In most cases, the button remains free to rotate during this process, dependent on the angle of the grooves in its surface to cause the desired degree of rifling twist. As variations in rifling twist may occur during this procedure, some barrelmakers affix the rifling button to a rod and positively rotate it with a sine bar.
Advantages:
- The procedure is fast and very economical, as only a single pass of the button is required to rifle a barrel.
- Button rifling is well suited to mass-production methods with high output.
- Button rifling leaves a smooth, bright finish inside the barrel that need not be lapped.
- Button-rifled barrels are very accurate.
- Bore and groove dimensions are very consistent.
Disadvantages:
- Button rifling creates stress in a barrel; high-quality button-rifled barrels must be stress-relieved after rifling.
- Buttons are expensive and difficult to make.
- Different groove configurations and different rifling twists require a new button.
- The button-rifling system is not flexible.
Button-rifled barrels can be extremely accurate; more bench-rest records are held by such barrels than by any other type. Button-rifled barrels are very common on modern center-fire and rimfire firearms.
Broach Rifling
Broach rifling is a modern, production-orientated variant of cut rifling that addresses some shortcomings of the cut-rifling process. While cut rifling utilizes a single-bladed cutter, a broach is a metal bar with sets of progressive cutting blades in its outer surface corresponding to the number of grooves. The cutting blades are fixed in spiraled succession, each blade cutting to slightly greater depth than the one in front of it. As the broach is pushed or pulled through the cold barrel, all the grooves are cut on a single pass. In some cases, a series of ever-larger broaches is run through the barrel until the desired groove depth is reached.
Advantages:
- Fast and well-suited to mass-production methods.
- Little or no stress is imposed on the barrel.
- Rifling twist is consistent from one end to the other.
- Broach-rifled barrels may be contoured after rifling.
- Adequate tolerances can be held.
Disadvantages:
- Broaches are expensive and hard to make.
- Different groove configurations and different rifling twists require a new broach.
- Broach-rifled barrels must be lapped.
- The broach-rifling system is not flexible.
- Match-grade barrels are not compatible with this system.
Because broach rifling was well suited to high-volume production, it was the rifling system of choice in making military rifles during the first half of the 20th century. In the second half of the 20th century, button rifling replaced broach rifling for the manufacture of rifle barrels with few exceptions. Today, broach rifling is commonly used to rifle some handgun barrels.
Hammer-Forged Rifling
Hammer forging is an ultra-modern method of rifling a gun barrel that is well suited to high-volume production by large manufacturers such as government arsenals and commercial corporations that can afford the sophisticated machinery. This method begins with a metal barrel blank about 12" long and 2" in diameter with a hole in its center honed to a fine finish. A tungsten carbide mandrel with the pattern of the rifling lands and grooves machined into its surface in reverse relief is then inserted into the hole of the blank. A forging machine with a series of radially opposed hammers is then used to compress the blank inward against the mandrel. As the hammers compress the outer surface, the blank is reduced in diameter and lengthened, simultaneously creating the bore and rifling. If needed, hammer forging can form the chamber and throat as well as a fully profiled outer surface. The spiral tracks of the hammers can often be seen on the outer surface of hammer-forged barrels. Some manufacturers turn the barrels to remove this surface, while others leave it in place. Barrel blanks may be hammer forged cold or hot. Hot hammer forging reduces the amount of effort that the hammers must exert on the blank and can result in better grain structure and improved strength. However, hot hammer forging is more expensive and requires more sophisticated machinery. The cold hammer-forging process produces barrels of excellent quality.
Advantages:
- Hammer forging consistently produces high-quality barrels.
- It can form chamber, throat and outer profile if necessary.
- It does not remove metal—no waste or chips.
- It produces barrels with excellent grain structure and high strength.
- Hammer forging produces superb bore finish, no lapping needed.
Disadvantages:
- Machinery and mandrels are expensive.
- Inflexible; changes in rifling require new mandrel.
- Quality is very good, but not match grade.
- Hammer tracks are left on outer surface.
- Process introduces stress in the barrel; must be stress-relieved.
Hammer-forged barrels are very common on high-volume center-fire hunting rifles and pistols where their consistency and strength outweigh their accuracy capabilities. They are not common on match-grade or varmint barrels, as their accuracy is perceived to be inferior to cut- or button-rifling methods.
Cation Rifling
A recently developed method of rifling a gun barrel by removing metal using acid is called the cation system. In this system, the barrel blank is first drilled and reamed in a normal manner. Next, a rod with a series of groove-width wipes is pushed through the bore while being positively rotated at the desired twist rate. Each wipe deposits a groovewidth trail of very strong acid that immediately begins eating into the surface of the bore. The strength and type of the acid and the dwell time it is allowed to remain on the bore can be varied to obtain the desired groove depth and to suit the metallurgy. When the acid has eaten into the surface the desired amount, a neutralizing liquid is flushed through the bore to stop the acid’s action. In practice, very close tolerances can be held. This system works very well on metal alloys that cannot be easily cut, buttoned or hammer forged.
Advantages:
- Uses no cutters, no buttons and no mandrels.
- Flexible system that can easily vary size and number of grooves and twist rate.
- Produces excellent bore finish.
- Does not impose stress on the barrel.
- Will rifle hard or exotic metal alloys that cannot be rifled by other methods.
Disadvantages:
- Equipment is expensive.
- Requires storage and handling of strong acids and neutralizers.
- System not yet well known.
As its advantages become better known, the cation system may become more popular. The cation system may very well be the only way new metal alloys can be rifled.