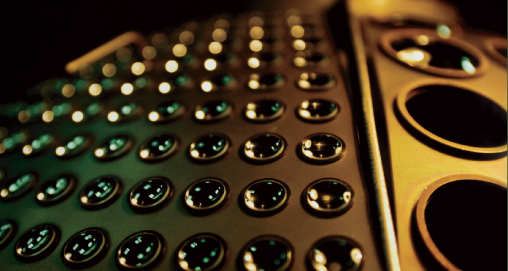
Originally printed in the November, 2008 American Rifleman.
Today’s binoculars, spotting scopes and telescopic sights are the best that have ever existed. Various factors account for this, not the least of which is an intense competition among optical manufacturers vying for market share. Most significant, however, has been the development and implementation of newer and better optical coatings. The broad categories include: anti-reflection (AR) coatings, reflective coatings, phase-correction (P) coatings, hydrophobic (anti-fog) coatings and abrasion-resistant coatings. All are important but foremost among these are the various anti-reflection coatings, which have improved over the decades to the point where they have nearly doubled the light transmission of sports optics. Light transmission denotes, as a percentage, the amount of usable light that passes through an optical instrument, relative to the amount that entered.
The Light Thieves
The spoilers that have bedeviled optics users since the invention of Galileo’s first telescope in 1610 are absorption and reflections, which dramatically reduce the amount of usable light that reaches the viewer’s eyes. Each optical element (individual lens, prism or mirror) inevitably absorbs some of the light that passes through it. Far more significant, however, is the fact that a small percentage of the light is reflected from each air-to-glass surface. For uncoated optics, this “reflective loss” varies between 4 percent and 6 percent per surface, which doesn’t seem too bad until you realize that modern optical instruments have anywhere from 10 to 16 such surfaces. The net result can be a light loss of as much as 50 percent, which is particularly troublesome under low-light conditions.
More serious, however, is the fact that the reflected light doesn’t just disappear, leaving a dimmer image. Instead, it keeps bouncing around from surface to surface inside the instrument, with some of the light from these second, third and fourth reflections eventually coming out through the instrument’s exit pupils and into the viewer’s eyes. Such scattered light is called “flare,” and is defined as “non-image-forming light, concentrated or diffuse, that is transmitted through the optical system.” The result is a veiling glare or haziness that obscures image details and reduces contrast. In extreme cases, it may even cause ghost images. An extreme example would be if you were trying to glass game on the shady side of a low ridge with bright sunlight streaming over the top and into the instrument’s objective lens. (Never look directly at the sun, either with or without optics, as it can cause serious eye damage.)
Single-Layer Anti-Reflection Coatings
The long awaited solution to the problem of reflective light loss came in the mid 1930s when Alexandar Smakula, a Carl Zeiss engineer, developed and patented the “Zeiss non-reflecting lens coating system” (now called anti-reflection or AR coatings), which was heralded as “the most important development of the century in optical science.” Soon thereafter the military needs of World War II accelerated the development of the coating, which was used by both the Allied and Axis forces in optical instruments ranging from field glasses (binoculars) to bombsights.
The theory behind AR coatings (see the illustration below) is a very complicated scientific concept. In application it consists of a transparent film, usually of magnesium fluoride MgF2, one-quarter of a wavelength of light (about six millionths of a inch) thick, deposited, by molecular bombardment, on a clean glass surface. Developing a method for applying such microscopically thin film, which is done in vacuum chambers, was a great technological triumph. This single-layer anti-reflection coatings reduced the reflective light loss from between 4 percent to 6 percent for uncoated surfaces to about 1.5 to 2 percent for coated surfaces, thus, increasing overall light transmission for fully coated instruments of about 70 percent, which, considering the accompanying reduction in image-degrading flare, was a remarkable improvement.
Multi-Layer Anti-Reflection Coatings
A major shortcoming of single-layer coatings, which are still widely used, is that they work perfectly well only for the specific wavelength (color) of light where the thickness of the coating is equal to one-quarter of the wavelength. This deficiency eventually led to the development of multi-layer broadband coatings capable of efficiently reducing reflective light loss over a wide-range of wavelengths. Today’s best multi-layer coatings can reduce reflective light loss to as little as two-tenths of one percent at each air-to-glass surface.
My introduction to multi-layer coatings came in 1971 when Pentax began using it’s “Super Multicoating” on camera lenses, where it nearly eliminated flaring and ghost images when photographing brightly backlit subjects. Sports optics manufacturers were a bit slow getting on the bandwagon, and it wasn’t until 1979 that Carl Zeiss introduced its “T*” Multicoating, which boosted the light transmission of Zeiss binoculars to slightly over 90 percent, while simultaneously improving image contrast. The reason it took so long getting from the first single-layer coatings to today’s multi-layer broadband coatings was because the latter, though based on the same scientific principles, are incredibly complicated, involving several thin layers of various fluorides, oxides, dioxides, etc. As you might expect, computers play major roles in the formulations and applications of such coatings.
Though overall light transmission continues to improve slightly, the highest levels with which I am currently familiar are about 92 percent for binoculars and 95 percent for riflescopes, which are well above the averages for such instruments. The primary reason why riflescopes tend to have slightly better light transmissions than binoculars is because they use simple erector lenses rather than complicated prisms for image erection.
Likewise, Porro prism binoculars tend to have better light transmission than roof prism binoculars of similar optical quality. Notable exceptions are the Carl Zeiss binoculars that use Abbe-Koenig roof prisms instead of the widely used Pechan-type roof prisms, which have one mirrored (usually aluminized or silvered) surface where between 4 and 6 percent of the available light is lost during internal reflection. (In a process called “total internal reflection,” Porro prisms and Abbe-Koenig roof prisms get 100 percent reflection on all their internal surfaces, without having any coatings.) Some leading manufacturers’ solution to the Pechan-prism problem are special multi-layer reflective coatings that get 99.5 percent reflection on the mirrored surfaces.
The caveat here is that one shouldn’t get too carried away in their quest for a few extra percentage points of light transmission. Consider, for example, that a 5 percent gain in light transmission in a high-performance optical instrument is roughly equal to a 150 f.p.s. gain in the muzzle velocity in a .300 magnum rifle—you’ll never notice the difference.
Will 100 percent light transmission ever be achieved in sports optics? One should never say “never,” but, apart from modifying the laws of physics, the answer is almost certainly no!
Coating Colors
Many believe that the quality of AR coatings can be determined by the color of light reflected from the surfaces. Perhaps, but to do so with any certainty requires considerable expertise. The color seen is not that of the coating material itself, which is colorless, but the reflective color or combined reflective colors of the wavelengths of light for which the coating is least effective. For example, a coating that is most effective in the red and blue wavelengths will produce a green reflection. Conversely, if the coating is most effective in the green wavelengths, the reflection will be some combination red and blue, such as magenta. The reflections coming from single-layer coatings of magnesium fluoride usually range from pale blue to dark purple. While the colors reflecting from the latest multi-layer coatings can be almost any color of the rainbow, with different colors showing on various optical surfaces throughout the system, a bright white (colorless) reflection usually indicates an uncoated surface.
Though unscientific, the following do-it-yourself test for evaluating AR coatings is both educational and informative. The only tool needed is a small flashlight or, lacking that, an overhead light. The trick is to shine the light into the instrument’s objective lens so that when looking along the beam you can see images of the light reflecting off the various air-to-glass surfaces within the instrument. (Note: Reflection will be coming from both the near and far sides of lenses and prisms.) Now, based on the above information, regarding color, you’ll get some idea concerning the types of coatings used and, more importantly, whether some surfaces are uncoated.
Other Types of Coatings
Lacking space for in-depth coverage of the other types of optical coatings, I offer the following brief summaries.
Phase-correction (P) coatings: Developed by Carl Zeiss (who else?) and introduced as “P-coating” in 1988, phase-correction coating is second in importance only to anti-reflection coating in roof prism instruments. The problem (nonexistent in Porro prisms) is that light waves reflecting off opposite roof surfaces become elliptically polarized so as to be one-half wavelength out of phase with each other. This results in destructive interference and a subsequent deterioration of image quality. The P-coatings correct the problem by eliminating the destructive phase shifts.
Reflection coatings: These mirror-like coatings—which often owe their effectiveness to constructive interference—are used more often in sports optics than one might think. Examples include: most laser rangefinders and the few riflescopes that employ beamsplitters; red-dot sights where a wavelength-specific coating is used to reflect the image of the dot back to the shooter’s eye; and, as previously discussed, in roof prism instruments with Pechan prisms.
Hydrophobic (water repellent) coatings: The archetype for water-repellent coating is Bushnell’s Rainguard coating that sheds water and resists external fogging. I extensively tested Rainguard coating in cold climates where inadvertently breathing on a scope’s eyepiece lens would have obscured one’s view of the target. The results were that, even when I intentionally breathed on both the objective and eyepiece lenses causing them to either fog or frost over, I could still see targets well enough to shoot.
Abrasion-resistant coatings: A persistent shortcoming with some anti-reflection coatings is that they tend to be soft and, therefore, scratch easily. Thankfully, today’s “tough” coatings, though still not universally used, are greatly improving the durability of outdoor optics ranging from eyeglasses to riflescopes. The toughest coating, by far, that I have tested is on the T-Plated external lens surfaces of Burris’ Black Diamond 30 mm Titanium riflescopes. I couldn’t scratch it, even with the cutting edge of a razor-sharp pocketknife. The latter is not recommended.
Coating Designations
The following terms are often used by optics manufacturers to describe the extent to which their instruments are protected by AR coatings.
Coated optics (C) means that one or more surfaces of one or more lenses have been coated.
Fully coated (FC) means that all air-to-glass surfaces have receive at least a single layer of anti-reflection coating, which is good.
Multicoated (MC) means that one or more surfaces of one or more lenses have received an AR coating consisting of two or more layers. When used by reputable manufacturers, this designation usually implies that one or both of the exterior lens surfaces are multicoated and that the interior surfaces probably have single-layer coatings.
Fully multicoated (FMC) means that all air-to-glass surfaces should have received multi-layer anti-reflection coatings, which is best.
Unfortunately, not all AR coatings of a given type are created equal, and some may even be bogus. Lovely as they are to behold, I am very skeptical regarding the value of the so-called “ruby” coatings, which reflect a dazzling amount of red light, making viewed objects appear ghastly green. When leading manufacturers, such as Carl Zeiss, Leica, Nikon and Swarovski, start using ruby or other offbeat coatings, I’ll start believing in them. The first line of defense against inferior and bogus coatings is to buy from a manufacturer with a proven track record for honesty. That isn’t to say that even the best companies are above hyping their proprietary coating. It’s usually the advertising people who get carried away.
References used in preparing this article include: The Photonics Dictionary, Bausch Facts about Telescopic Sights by Bausch & Lomb (which is out of print), Melles Griot’s Optics Guide 5 and the Encyclopedia Britannica.