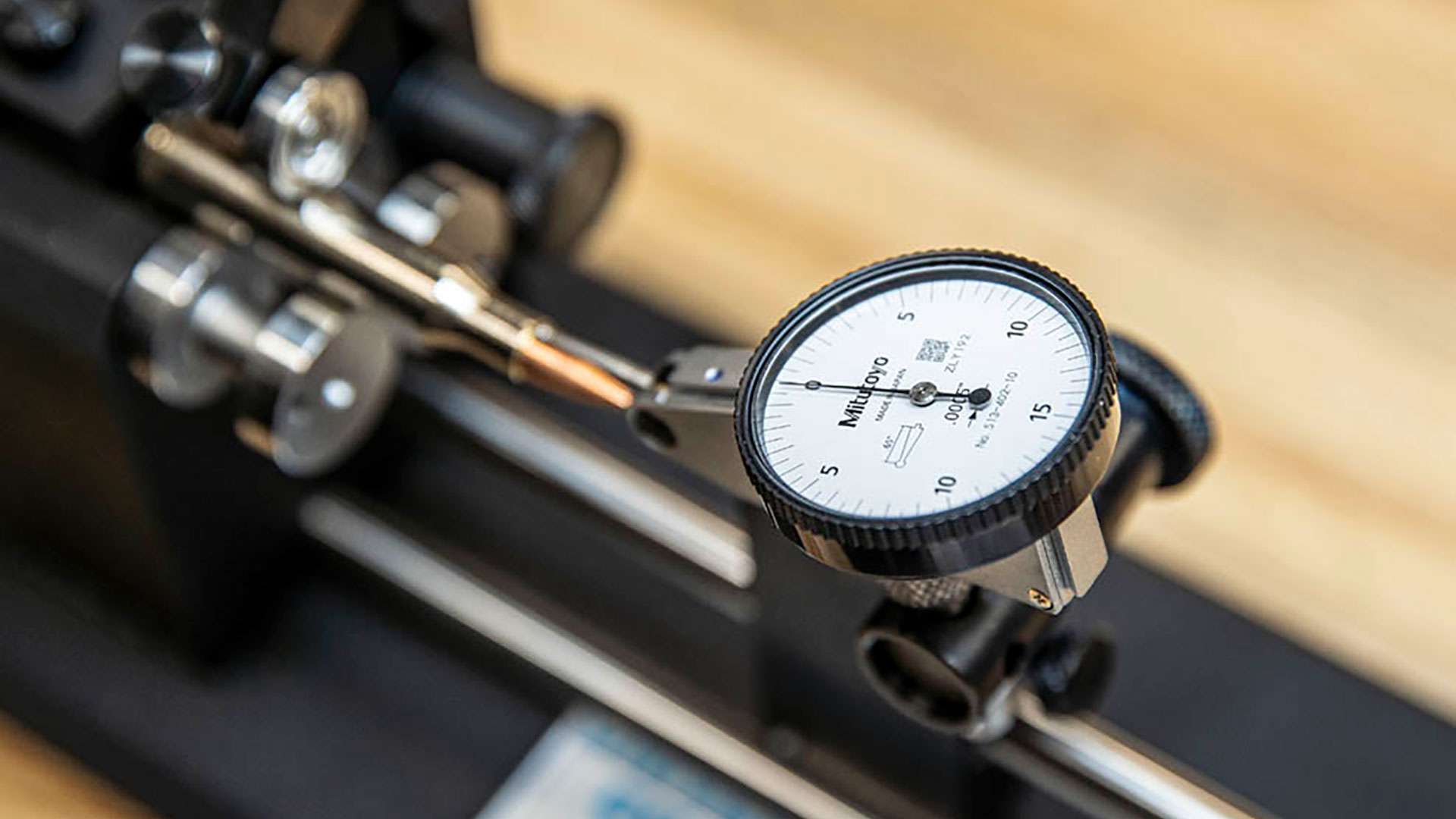
The ammunition shortage that began in 2020 continues and lack of inventory makes it a frustrating time for enthusiasts and retailers. It’s no pleasure cruise for manufacturers either, whose Herculean efforts have yet to refill shelves for a variety of reasons, including the underreported fact that commercial cartridge production is laborious.
Companies added staff, increased shifts and invested in equipment to address the record-setting demand. The Remington ammo plant is once again operating at full capacity and many retailers are finally reporting 9 mm and 5.56x45 mm NATO FMJ loads are in stock. It’s a different story for other cartridges, though, particularly self-defense, match and hunting loads.
Several manufacturers explained to AmericanRifleman.org the variety of steps required to make a single cartridge. The process is not a simple one.
Safety, Quality, First and Foremost
A manufacturer’s operation is more complex than that of a handloader, who may spend an entire evening cranking out a couple hundred rounds for their next range session. The companies make the bullets and cases, for example, from scratch—when raw materials arrive in a timely fashion. There are also multiple and painstaking quality-control layers at a commercial operation not required when creating cartridges for personal use.
A cutaway diagram of a 9 mm cartridge. Photo courtesy of Hornady.
“Once a round starts production, it continues to undergo rigorous quality testing across every step of the production and packaging process,” explained Joel Hodgdon, Remington Ammunition’s marketing director. “Remember, we are making ammunition here that needs to meet stringent requirements. Our Arkansas factory takes copper, steel, lead and other raw materials through the entire production process at a scale and pace unimaginable to someone who hasn’t been through our factory. I wish getting more ammo out the door was as simple as turning on an extra couple RCBS loaders but it’s not.”
“One of the cornerstones of our company is quality and consistency—and I can assure you that we’ve cut no corners in quality and testing,” said Hornady Marketing Communications Manager Seth Swerczek. “Another extremely important factor in our manufacturing is safety—which we take very seriously—and we’ve not cut any corners there either.”
Ingots of lead used in making bullet cores. Photo courtesy of Freedom Munitions.
“SIG Sauer is doing everything possible to accelerate production of the very complicated process of manufacturing both rifle and pistol ammunition,” said Tom Taylor, chief marketing officer and executive vice president of commercial sales at SIG Sauer. “There is a very fine line between accelerating production and maintaining the highest possible standards."
"We know there continues to tremendous demand in the marketplace and we do not see an end in sight for this demand. But we know that for both the civilian market and the hundreds of military, government and law enforcement contracts around the world, we must maintain the highest possible standards.”
Symphony in Each Round
The companies stay in business by somehow orchestrating raw material arrival in concert with scheduled production runs, while maintaining strict quality control during the entire process, and finally preparing boxes for shipping. Idled machinery, manpower and even inventory on the warehouse floor are expensive. The first and last steps became and remain a daunting challenge with the COVID-19 pandemic.
“The shipping companies that deliver materials to us and ship our product across the country are extremely busy,” Swerczek said. “Everyone has experienced shipping delays, whether that be us at Hornady manufacturing ammunition or someone at home ordering toilet paper. While we know the shipping companies are doing their best, it is sometimes taking longer to get our finished product to its final destination.”
Some of the raw materials used in making ammunition. Photo courtesy of Freedom Munitions.
That transportation shortage is impacting more than schedules, according to a statement made by Chris Metz, Vista Outdoor CEO, during a quarterly earnings conference call earlier this year. “But as I mentioned, it is freight, as you talked about it’s container shortages, which we’re going in negotiating every day, different rates to make sure that we’re being smart about getting product on the water…,” he explained.
Truckers to haul semi-loads of cartridges are also in short supply and those still willing to get behind the wheel are reaping some serious financial benefits. Rich Jennings is vice president of Regional Supplemental Services, a company specializes in providing drivers to manufacturers. He told a reporter from Business Insider this month that, “I've never seen drivers get paid what they are paid today. They are getting well into the six figures and they can easily make $3,000 a week.” Despite the pay, the story ominously explains one perishable food company, “…lost 40 percent of its drivers and warehouse workers during the pandemic.”
Brass wire often used to make pistol cartridge cases come in long, industrially heavy spools that must be shaped, have a primer pocket punched and even undergo an annealing process before cartridge creation begins.
The gun industry doesn’t have the volume to demand priority transportation services, either. When raw materials finally arrive, however, they begin a step-by-step production process.
Hornady Loads
“It all starts with making a cartridge case,” Swerczek explained. “The brass we use for cartridge cases shows up and undergoes a lengthy process of being drawn, annealed and shaped to its proper form. Once a case is complete, the flash hole must be pierced and a primer inserted. Remember, brass is an alloy of copper and zinc. Copper is used extensively in various manufacturing and construction materials—with demand up, the cost of copper has increased as well.”
There are a variety of steps required for a single piece of brass to be molded into a cartridge case. Here’s one company’s process, beginning at the right and ending with a ready-to-load casing at the left.
“A round of ammunition must have a bullet. The bullet jacket material arrives and is drawn into cups. At the same time, lead shows up and gets processed into wire and then cut into cores. Once on the press, the copper jacket is drawn into shape, the lead core inserted, and final swaging operations are done. The bullet press operator then refines his adjustments until the bullets meet our accuracy standards—which we test at regular intervals."
“Once the case is manufactured with a primer inserted and the bullets are made, it’s time to load ammunition. The ammo press operator feeds the machine bullets, powder and cases and adjustments are made to ensure the ammunition meets our quality standards. At regular intervals, the ammunition is tested in our ballistics lab to ensure proper performance."
A large container full of bullets ready for assembly into complete cartridges. Photo courtesy of Freedom Munitions.
“Once the ammo manufacturing is complete, Hornady ammunition is hand inspected before it is packaged into boxes, boxed into case quantities, and ready for shipping. By hand inspecting our product, it helps us ensure that we are delivering the best product we can."
“The process mentioned above is something we’ve being doing for quite a while—and we’re really good at it. That being said, the process running smoothly is contingent on several factors, such as: raw materials showing up on time, the time it takes to get a bullet to perform to our accuracy standard before the run can start, the availability of primers and powder, the time it takes to get the ammunition to perform to our quality standards, the availability of cardboard boxes to package the ammo into, and the fact that there are only 24 hours in a day, just to name a few.”
SIG Sauer Loading
The volume of steps and their sequence are basically the same at SIG Sauer’s ammo plant in Jacksonville, Ark. Taylor summarized them as:
- Rifle cases formed from brass cups in a multi-die/punch press (pistol cases are sometimes formed from brass wire);
- Annealing if required to relieve stress from the brass-forming process;
- Lead wire extruded from lead billets;
- Bullet cores formed from lead alloy wire and cut to length;
- Jacket material punched from copper strips;
- Bullet assembly machines form copper jackets in which lead cores are inserted and sealed at the base of the bullet;
- Priming is normally done as a separate process from loading;
- And loading is finally done on multi-stage reloading machines or high-volume plate loaders where hundreds of cartridges are worked simultaneously with each press stroke (powder charging, bullet seating, crimping).
It takes time. Rimfire cartridge manufacturing is equally laborious and detail-oriented, a fact covered in an earlier video report from American Rifleman.
Manufacturers Working Overtime
Despite the challenges, and quality-control steps, manufacturers are doing their utmost to refill empty shelves. “Our Remington ammo team in Arkansas is ramping up production and doing everything we can to get more ammo to hunters and shooters, but we won’t sacrifice quality or safety to make more ammo,” Hodgdon said.
Finished rifle cartridges. Photo courtesy of Federal.
Taylor explained, “…even though we cannot compromise quality for speed, we are doing everything in our power to both invest in new equipment and look for ways to introduce new technologies to increase our production rates.”
“In summary,” Swerczek added, “there are a myriad of things that can slow down or hinder the process of making ammunition. While we have experienced our share of them, what remains certain is Hornady’s unwavering dedication to the industry and to their employees. We are making and shipping more products than we ever have, we are continuing to make the highest quality possible, all while being safe and valuing our employees.”