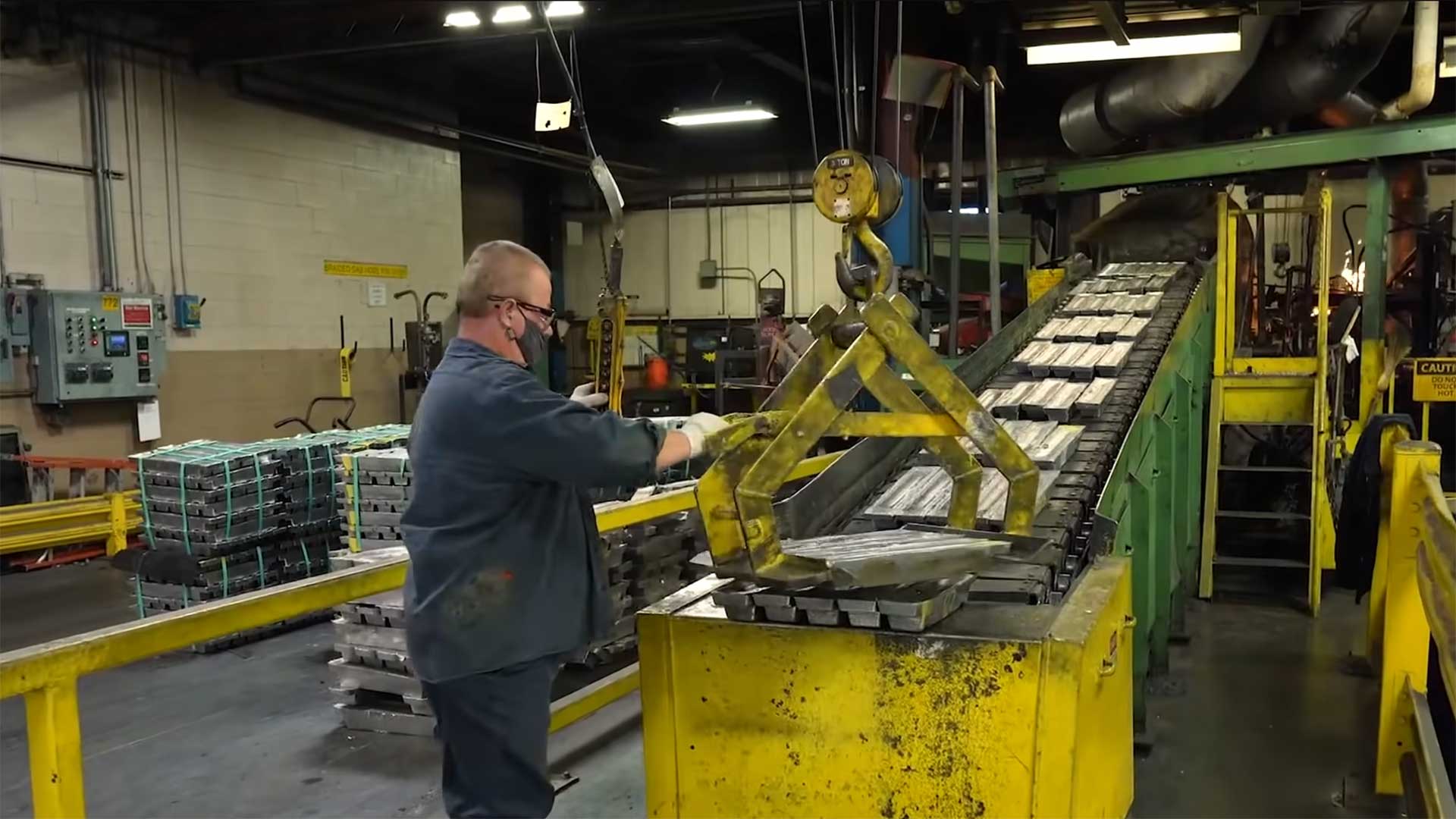
Aftershocks from the historic collision of COVID-19 and social unrest are not over, and the rumblings are still being felt by firearm companies. The industry’s finest have harnessed a variety of approaches to avoid chronic raw material shortages in the future—which will undoubtedly reduce the magnitude of the next event—but survey results released last week indicate things are still shaky, and that uncertainty will likely continue through next year.
Fifty-one percent of the U.S. companies queried by SAP—a Germany-based firm and global leader in supply-chain software for manufacturers—said strains in the supply chain will continue into 2023. The impact, according to comments SAP Board Member Scott Russell made to CNBC is, “The supply chain rules have changed and they’ve changed for good … The chaos and the disruption is proving that the supply chain just wasn’t as robust as they expected it to be.”
Financial Impact
For most in the gun industry, however, it wasn’t the cost of raw material that hit bottom lines the hardest. Hauling it to their factories, however, did.
Bill Wilson, CEO and president of Wilson Combat said, “The disruption of and huge increase in the cost of shipping actually hurt us more than any material shortages.” Tom Taylor, chief marketing officer and executive vice president of commercial sales at SIG Sauer, concurred. “We will figure out how to get raw materials. It’s the dramatic cost increases, fees and shipping costs that are the bigger issue,” he said.
Varied Industry Response
Ruger has already adapted to the challenges. “I think we’re seeing our ability and our strong balance sheet to buy forward on raw materials helps us both in terms of something like protecting against inflation as well as making sure we have available steel, aluminum, etc. to weather any downturn from a supply standpoint,” Chris Killoy, Ruger president and CEO, told investors during a conference call earlier this year.
The approach is slightly different at Wilson Combat. “We’re not necessarily keeping more raw material on site, but we’re booking a lot of material for release delivery as we need it,” Wilson explained.
Ripple Effects
The Russo-Ukrainian War is another factor, and it’s affecting more than just shipping. The Century Aluminum plant in Kentucky—one of the nation’s largest aluminum manufacturers—closed in late June. Officials cited a conflict-driven tripling in the cost of energy as the reason for idling its 600 workers. According to Louisville, Ky., news radio WDRB, management hopes to reopen by next summer. The firm’s future could depend entirely on international developments.
Inflation may dominate the headlines, but behind the scenes, there’s another factor at fault. Results from the SAP survey indicate an overwhelming majority of U.S. manufacturers understand sweeping changes are needed in their supply chain. That isn’t free and, as Russell noted, “The costs to be able to build that resilience are ultimately being borne by the consumer.”
Shipping concerns continue to weigh heavily on the manufacturing sector, including the gun industry. So don’t be surprised if that needle moves again next year, hopefully not with the Richter magnitude we experienced during 2020 and 2021.