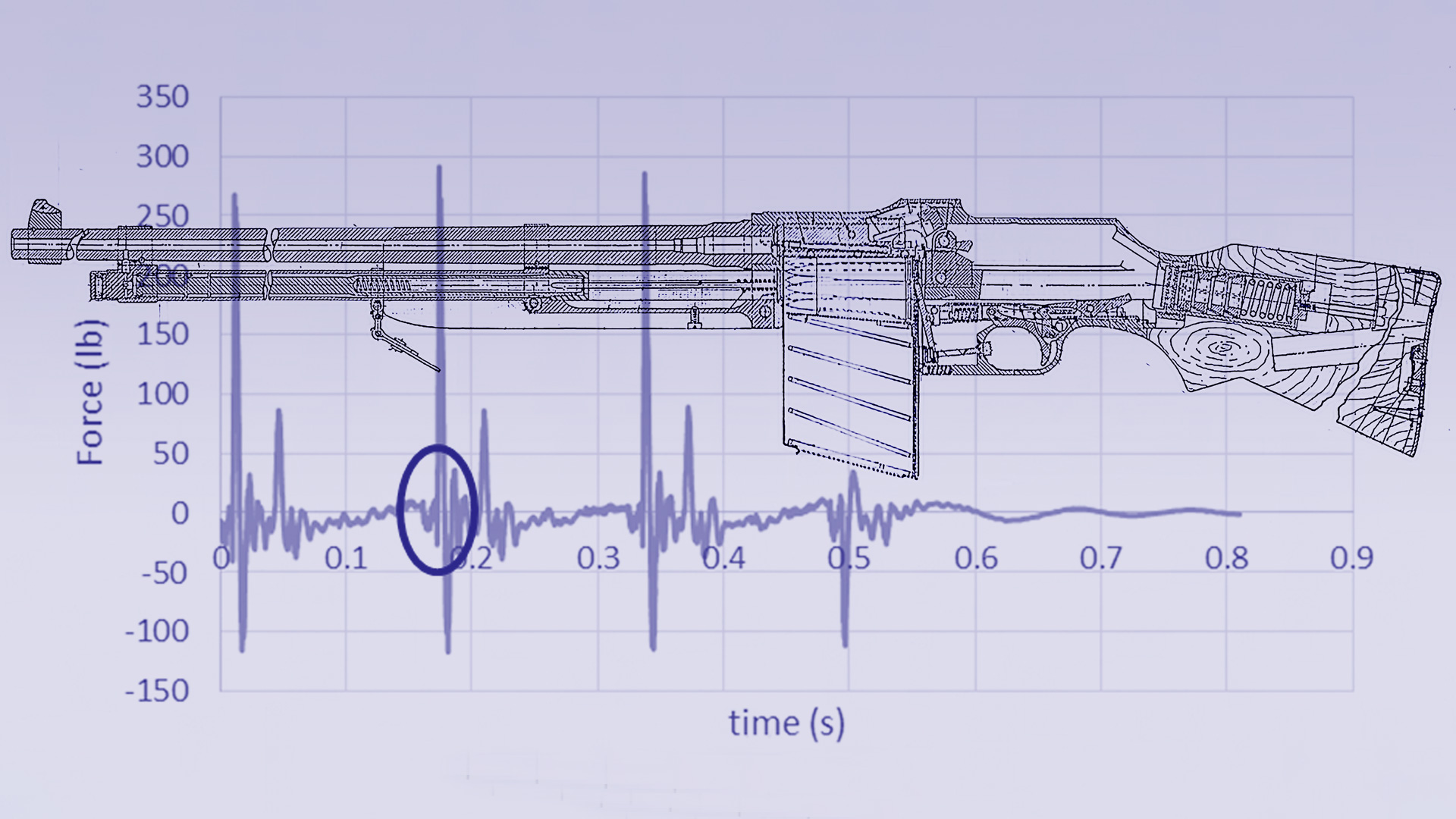
Think guns can’t talk? Think again. Guns talk in much the same way that you and I do. When we speak, sound energy is produced by forces causing vibrations in the air. This vibrational energy is transferred through the air in the form of sound waves in various frequencies. People can hear a wide range of frequencies, and most animals can hear even more.
So, what about guns? Whenever gun components go through a cycle, like a bolt locking or a cartridge being fed, vibrations are created by those actions as well. From what has been learned during an Army-funded study at Knight’s Armament Co., it’s possible to not only record and examine these vibrations, but also to understand what they’re saying.
As an example, when a cartridge feeds normally, it sets up a typical vibration, but if there is an abnormal feed or a jam, the vibrational characteristics are totally different than the norm. The intensity of these vibrations is significant, too. Low-level vibrations can be associated with smooth functioning, while a crash-bang during bolt lockup, for example, could either be the indication of a unique problem—like the sudden intrusion of dirt—or it could be a gun screaming for help due to a design flaw.
So, how do Knight’s engineers listen to guns?
Getting Analytical
Knight’s Armament Co. has been listening to guns speak for a decade now, but only recently has it begun to understand what they’re saying. It all began with an Army-funded project to study recoil and the controllability of firearms. The topic had been studied extensively in the past, but most prior studies had used humans as “test fixtures.” Unfortunately, there is so much variation in how people hold and fire a gun that the results were inconsistent, and little of any value was ever learned.
During the course of its most recent study, Knight’s developed what is called a Weapon Recoil Simulated Shoulder (WRSS)—it’s a firing fixture designed to hold shoulder-fired arms of up to .50 caliber. Firing guns from the WRSS allows for consistent measurements of recoil force and locates shot impact locations for multiple rounds. With the human variable removed from the equation, the WRSS gives an accurate comparison between gun models.
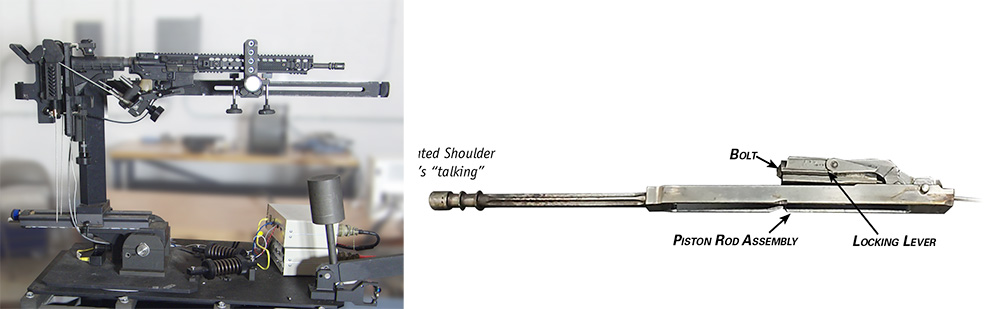
In order to design the WRSS to mimic the human body, Knight’s took the approach of measuring the vibrational characteristics of a human body shooting a firearm. Using this data, it built a mechanical fixture with the same characteristics. The end result is a shooting fixture that eliminates the inconsistencies introduced by flesh-and-bone soldiers.
During full-automatic fire, the WRSS records where the first, second, third—up to the fifth—shot will impact the target, providing a quantifiable measure of firearm controllability. Additionally, accelerometers can be placed anywhere on the gun to measure the g-load at that location (at a g-load of 1, a 1-lb. rifle scope weighs 1 lb., while at a g-load of 100, the same scope weighs 100 lbs.). These g-force measurements are important in the development and mounting of relatively fragile accessories such as scopes, laser pointers and night-vision devices. It was from the vibrational measurements given by these accelerometers that the engineers realized the guns were talking.
Knight’s engineers initially looked only at the peak of these acceleration waves to find the maximum g-level, but during their upgrade to the next-generation WRSS, they noticed the vibration patterns were similar during normal operation but wildly different during an abnormal function. The guns were talking—but what were they saying?
The situation became clearer when they compared a set of parts known to function poorly to a set that worked properly. From the frequency-response measurements in the results, it became obvious as to when and where the malfunction incident occurred. The higher- and lower-than-normal peaks of these measurements were, in effect, the gun crying out in pain from the abnormal operation. In further testing, similar data from the WRSS system was used to identify the cause and effectiveness of the corrective action.
One additional device important to the study was the high-speed video camera. These new cameras not only produce slow-motion videos of gun components moving through their cycle but can also track them and determine their precise position at any given time. Coupling the accelerometers with the high-speed video output gave the Knight’s engineers data not only on what these vibrations were saying in the language of “Gun,” but where in the cycle they were saying it.
Same Family—Different Language
An interesting comparison in “cycle talk” was noticed between the .30-’06 Sprg.-chambered Browning Automatic Rifle (BAR) and the 7.62 NATO-chambered M240—a machine gun known worldwide as the MAG-58. The BAR was invented by John Browning and used during both world wars. The M240/MAG-58 was invented by Fabrique Nationale in Belgium and fielded in the early 1960s. The action and operating cycle of the M240 is almost identical to the BAR. The major difference is that the BAR feeds from a magazine inserted into the underside of the rifle, while the M240 uses linked ammunition fed from the top—their two cartridges are not too different. Both arms are known for high reliability, and it was expected that the instrumentation would demonstrate very similar results for the two guns. This was not the case.
When Knight’s studied these two examples, it recorded the noisy ammunition feed as the bolt stripped a round from the link belt of the M240. Other interactions, such as bolt lockup and rear buffer impact, were noisy as well. In contrast, the BAR whispered throughout its cycle, smoothly drawing a round up out of the magazine followed by a precise chambering and bolt lockup. It seems that the more we analyze Browning’s firearms, the more we are amazed by his mastery of gun design.
Using the first generation of the WRSS, the Army has found it to be a beneficial tool in evaluating recoil systems, muzzle devices and even drive springs. To date, it has documented the characteristics of the recoil and control characteristics of more than 50 weapon systems. With the new generation of WRSS, the Army is also looking at the vibrational characteristics during gun cycles and learning “Gun” language just like the Knight’s engineers.
A Diagnostic And Evaluation Tool
Why would any gun company need a WRSS? Imagine you’re a test technician developing a new firearm. After firing a few rounds, you notice one of the parts has an unexpected shiny corner or a curious abraded surface. You recognize this as a sign of a potential problem, and you know there isn’t supposed to be anything touching this part at any point in the cycle. So what caused the shiny spot? Locating the source might require cutting windows into the receiver or other parts to try to “catch” the event using a high-speed video camera. Thousands of rounds might be fired through several prototypes before the source of the interference is determined.
With the WRSS, it’s only necessary to record data from the accelerometers then move them to different locations in order to pinpoint the source of the interference; it doesn’t matter if the errant parts are visible or not. In a similar fashion, the WRSS can also be used to find components undergoing excessive vibration. Experience has shown it takes about 20 rounds to locate these anomalies, representing a huge savings in time and expense.
For new, untested components, the remotely fired WRSS is valuable in reducing risk to test operators since it mounts the firearm just the same way a person would hold a gun. Knight’s has found this to be particularly useful for evaluating muzzle flash, as tests are safely conducted in complete darkness with no test technician required for shoulder firing.
According to the Army, the WRSS has greatly reduced the time and cost for it to evaluate new and modified firearm components to predictively see how they will perform before they ever reach a soldier’s hands. It cites the example where the performance of a dozen muzzle-brake configurations were compared using the WRSS. It quickly narrowed down the selection to just two or three before actual human-in-the-loop evaluations.
The WRSS was able to test those dozen configurations in a matter of a few hours, whereas it would have taken days or weeks to run a statistically significant number of shooters through a test using those same muzzle brakes. In the past, it might have only machined two or three muzzle brakes because that is all it would have the funding and time to properly test. Now, with the WRSS, and the ability to use additive manufacturing (3D printing) parts, it can significantly increase the number of design iterations on a component in a fraction of the time. The cost and time savings are tremendous and results in the development of a more refined component.
The Army’s take is that, in many ways, the WRSS brings to hardware evaluations what additive manufacturing brings to prototype manufacturing—both are fantastic tools in a development engineer’s toolbox. At the end of the day, it does use actual soldiers in the final testing of components; it’s just that now the components have improved characteristics that are more refined and more thoroughly tested.
As for Knight’s Armament, owner C. Reed Knight, Jr., couldn’t be happier with what his engineering team has developed. In his own words: “The advantage the WRSS has given us as a research and development team is we have taken the variability of the human subjectiveness out of the loop. The incremental improvement can be attributed to an improvement, and not the operator’s subjective experience. And the WRSS can resolve very small variables that the human cannot detect, because the event is so transient.”
The first upgrade package was sent out recently to improve usability of the system and to incorporate refinements to the control box and software. All the previous data taken is comparable to the current system. Given the Army’s use of the system and the different applications Knight’s has found, future uses may be diverse and unexpected, and commercial sales are expected.
Knight’s engineers have figured out what guns are saying but haven’t yet come up with a way for them to relate their history. As for my own guns, I’ll probably never know who carved the image of a retriever on the stock of the M1 carbine my dad brought back after World War II. Neither do I expect to learn what was on the mind of the German officer when a young Alexander “Sandy” Patch liberated his Mauser Broomhandle—another gun I own—during World War I. And yet, I continue to be amazed by how far technology has taken us since I began my career in firearms. Maybe there is hope after all.
George Kontis has worked as an engineer at the General Electric Armament systems division designing and testing aircraft cannons and small arms. He developed new firearm testing methodology and was co-designer of the GPU-5A 30 mm gun pod. He has held engineering and senior management positions at: GE, FN, Barrett Firearms, Heckler & Koch and Knight’s Armament Co. Kontis is listed as a subject-matter expert in firearms by the U.S. Defense Systems Information Analysis Center. In 1998, he was awarded the Col. George M. Chinn award for his contributions to the field of small arms, and he holds numerous firearm-related patents. In 2015, he founded Gun IQ International LLC, a consultancy firm focusing on advancing firearm technology, failure analysis, patent issues and the use of advanced materials and processes. He has authored more than 50 articles with a primary focus on the technical aspects of firearms.—The Eds.