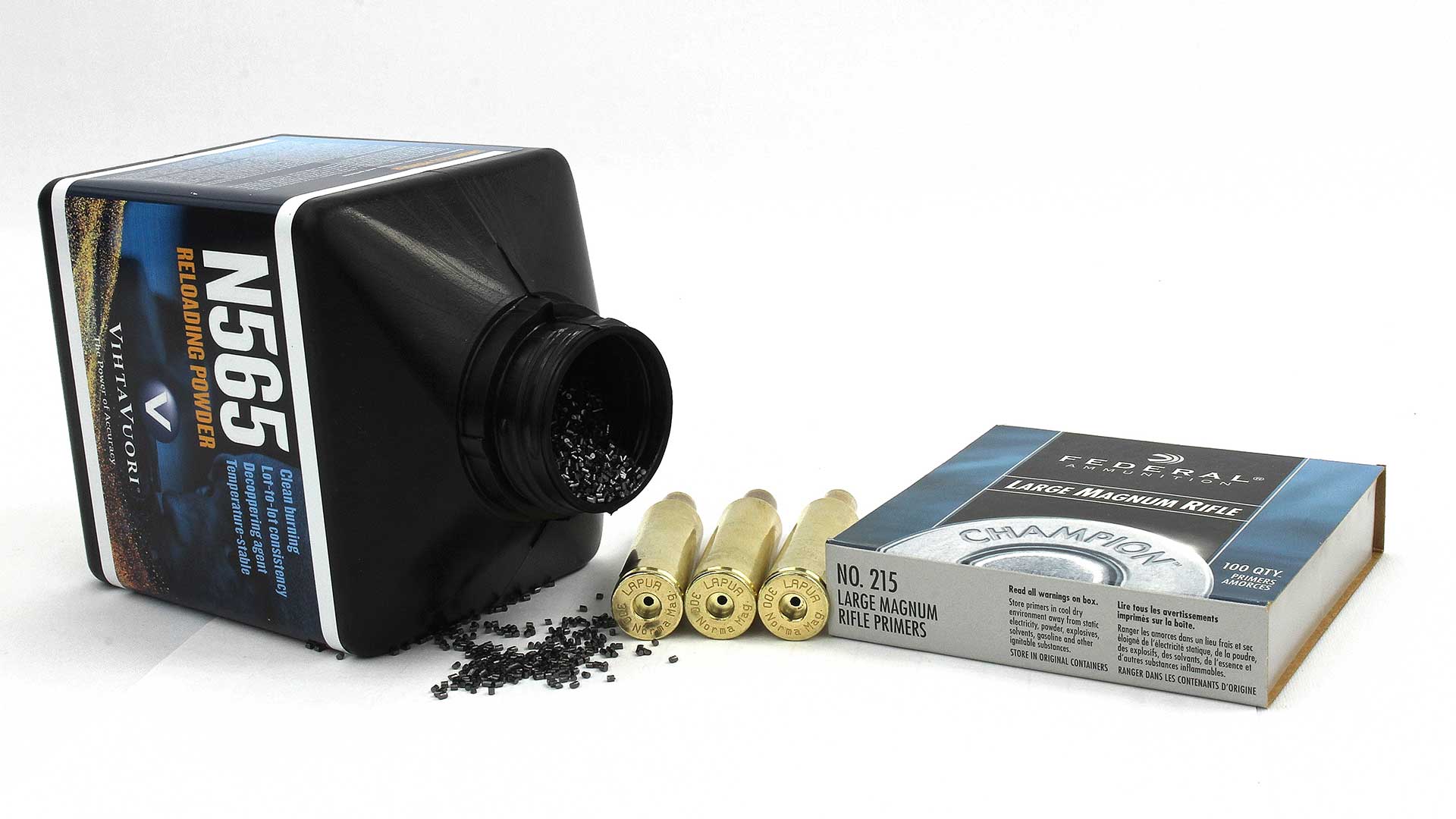
To say that factory ammunition is amazing would be quite an understatement. Imagine a recipe that performs admirably through nearly any rifle you can think of yet is mass-produced by the millions. This is terrific when you have an armory of rifles to feed, but what if you just have one gun?
Recently, I’ve been doing a bit of work with a Barrett MRAD chambered in .300 Norma Magnum, and I have been lucky enough to get my hands on more than 100 rounds of Berger’s new 215-gr. factory loading that was built specifically for that rifle. While this ammunition produced some terrific groups, I wanted to see just how well it could shoot if I developed a handload specifically for it. That might resonate to some readers as strange, because it would appear that was already done at the factory by Berger. The truth is, no matter how good of a job the boys in the lab did for the masses, there is still a bit of customization that can be done.
My story starts with the brass itself. Berger isn’t shy to admit that handloading is and always will yield better ammunition than store-bought. After all, part of its marketing strategy (back when ammo was hard to sell) was that, after shooting its factory loads, you have fresh, fire-formed Lapua brass left over. That statement conveys the essence of why handloads outperform factory ammunition nearly every single time.
A Barrett MRAD shown with its reloading components.
When a cartridge is fired, the case swells until it contacts the chamber walls. In that moment, it is molded to your gun's unique characteristics. As it forms this concise fit, the case's mouth and neck self-center to the bore, ensuring an even straighter alignment than the original loading. Lapua brass is among the finest in the world and is sought after by long-range marksmen, benchrest shooters or rifle enthusiasts looking to make the best ammunition that they can. Most of its allure comes from the consistency that exists from case to case in respect to the neck, primer pocket and weight.
After firing every last factory round that I had, I stood in my workshop with a pile of brass that was still a long way from being the best ammunition this gun has ever seen. I started the process by cleaning it with an old reliable Lyman Turbo Twin vibratory tumbler. I taught this old dog a new trick by adding Lucas’ Gun Metal & Tumbler Media Additive to the mix, as I find it cuts cleaning time in half (or less). I do this to remove any leftover grit left inside of the cases, which will change internal volume slightly from shot to shot. Another reason is to remove anything on the exterior that might scratch my dies or, if it makes it that far, my chamber.
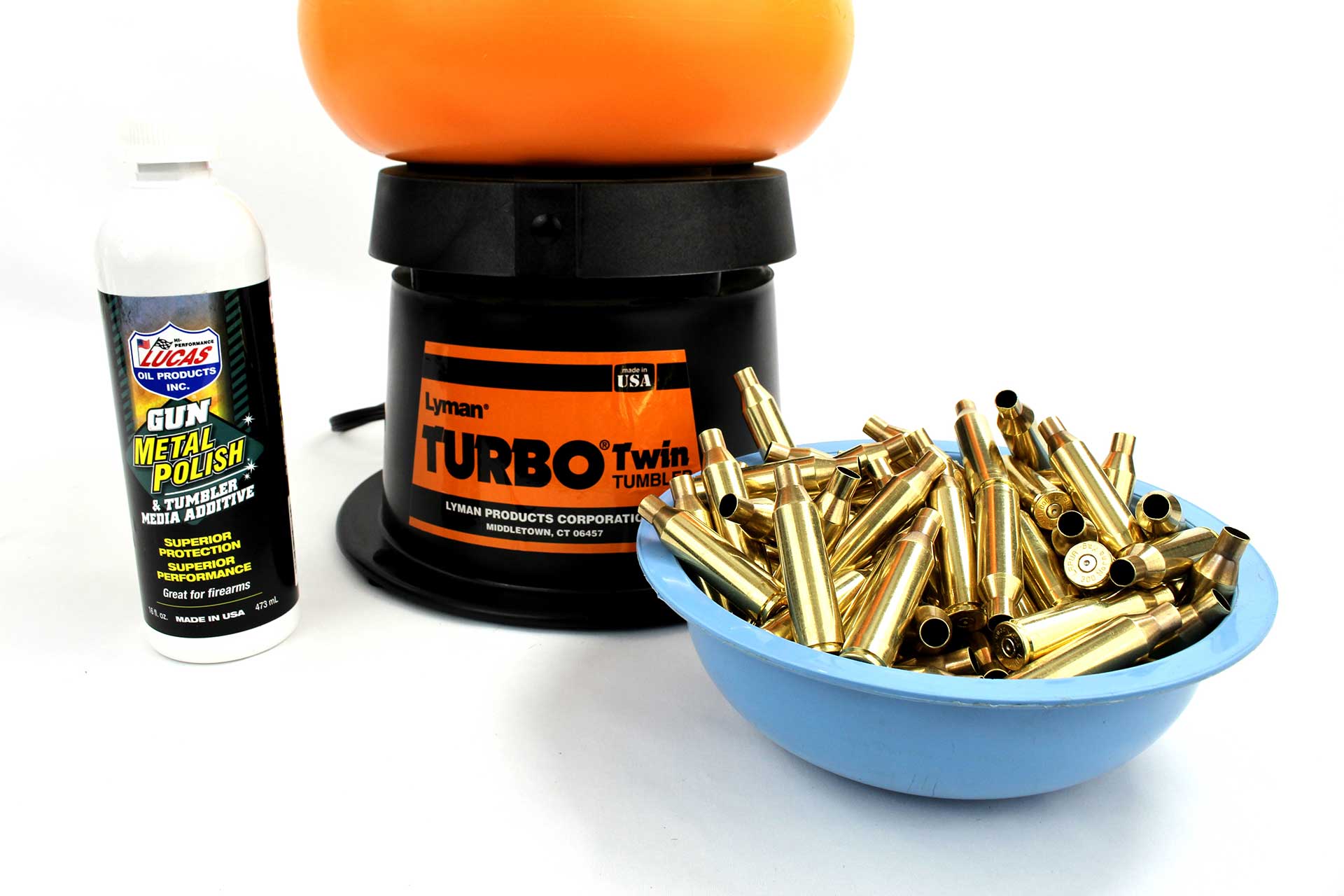
With polished brass in hand, it was time to resize these, though in a minimal way. Those beautiful, fire-formed dimensions would be completely erased if I ran these cases through a full-length sizing die, as that would just knock everything back to SAAMI specs. Instead, I opted to use an RCBS Match Master bushing die, which is a more precise spin on traditional neck sizing. These dies use an interchangeable neck bushing system that allows you to get away with sizing the neck down just enough to hold a bullet. To determine which bushing you need, you can use one of two methods.
One method requires measuring a loaded factory round, which I didn’t have. The other involves measuring the case walls of a fired round and doing a bit of math. It was then that I gained an appreciation of the work put into a piece of Lapua brass, as the neck wall thickness was consistent the whole way around, and even the same from case to case. This is a feat the typically requires the arduous process of neck-turning each case by hand on a tiny lathe-type tool. After crunching the numbers and installing the correct bushing, I enjoyed a lubricant-free sizing process and had loadable brass in just a few minutes.
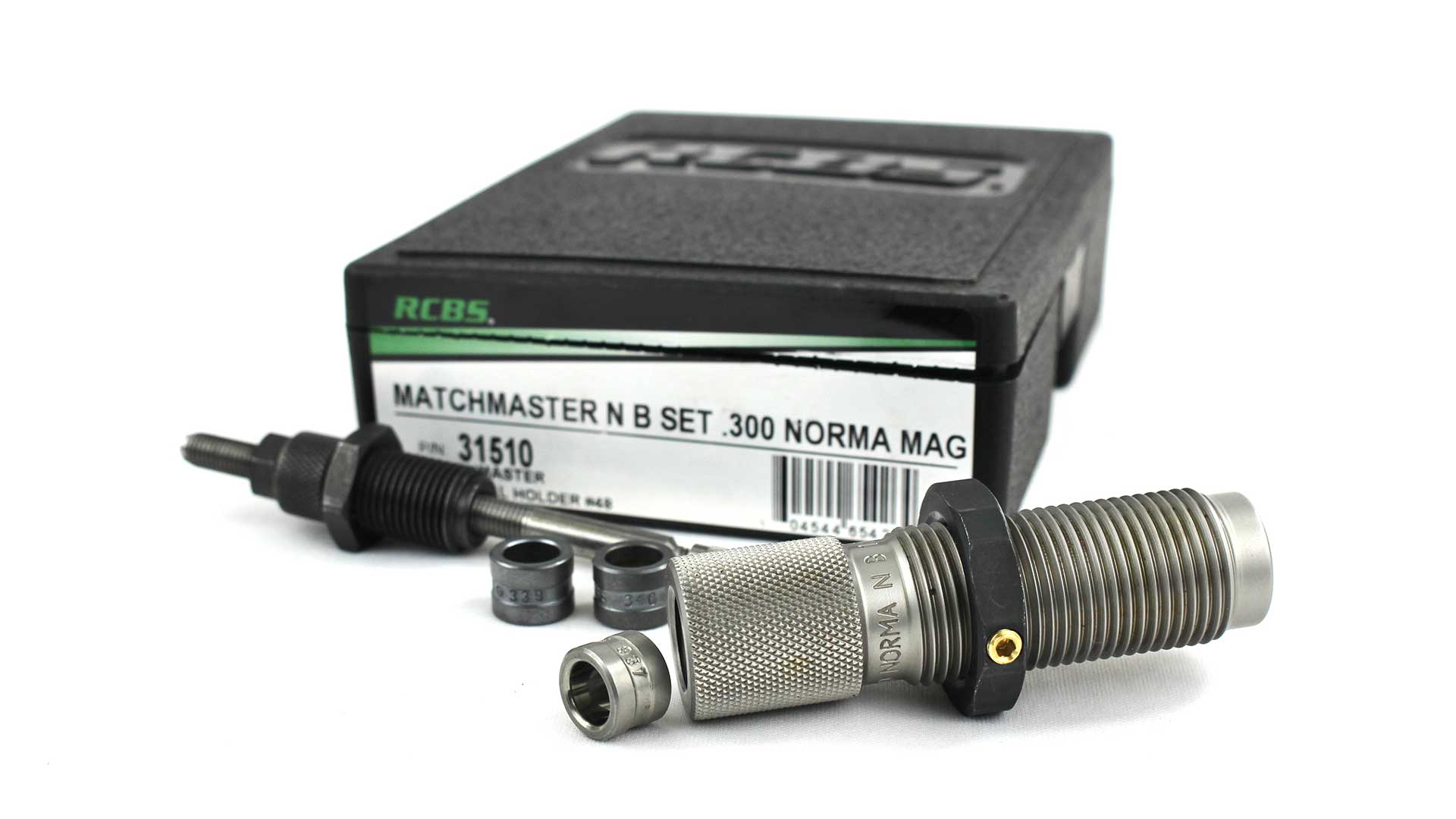
With the primers removed, I turned my attention to the typical primer pocket uniforming and flash-hole deburring that makes up most of my match-prep on a new lot of brass. Uniforming removed next-to-zero material, as did running the deburrer down into the case. These processes are designed to remove excess material that is left over from hasty manufacturing; it’s no surprise that there wasn’t much to be removed. Last, I like to segregate cases by weight but, again, Lapua quality intervened and indicated that my time was better spent elsewhere as my first 20 cases were within one grain of the batches 313-gr. median weight, indicating tolerance of only about +/- 0.3%.
After researching the VihtaVuori website, I deduced that N565 was going to be one of the best candidates for powder. This data sheet also pointed me to Large Rifle Magnum Primers. Typically, when I’m splitting hairs, I opt for match-grade primers but with things being the way they are these days, I had to make do with standard fodder. On the bright side, they were Federal primers, which have always left me with satisfactory results over the years.
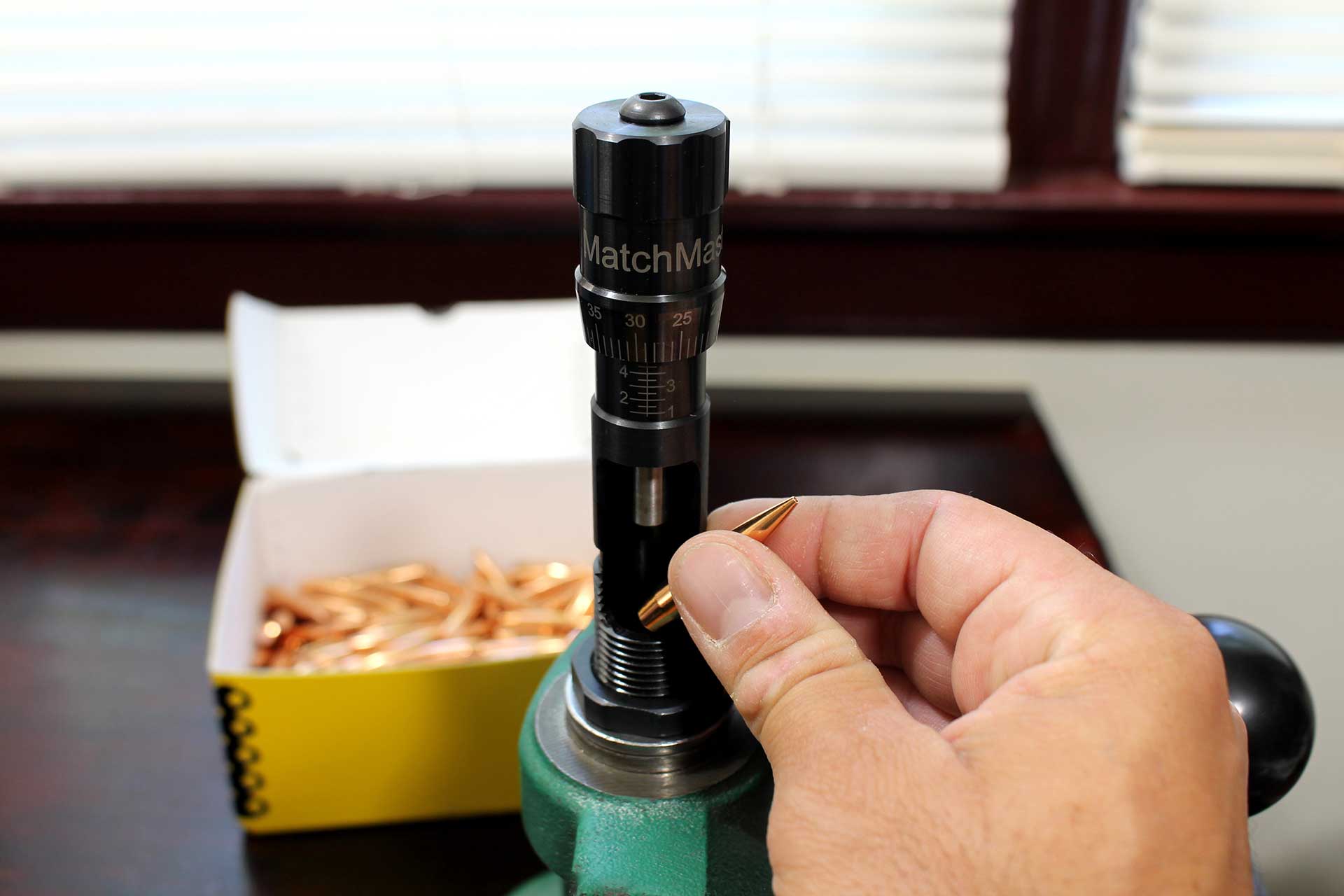
As the cases can hold upwards of 80.0 grains of powder, I opted to use .5-gr. steps in my development instead of my typical .3-gr. increments. I also only loaded three rounds per step in interest to save components, again due to the national shortage. My bullet selection was the same 215-gr. Berger Hybrid Target that shoot so well in the factory ammunition and I loaded each to give me with a COAL of 3.600”. This fit well inside of the magazine and put about half of the bearing surface into the case. As I finished each load, I placed them into a carefully labeled MTM H-50 XL box, which was surprisingly large enough to carry them tip-up, and headed directly to the range.
My range day had conditions that I could only dream of, as the wind was completely absent and the ambient temperature was a comfortable 65 degrees. I sped through my load testing and was blessed with a sea of half- to quarter-MOA three-shot groups at 100 yards, with charge weights 74.0 and 78.0 being the most consistent. As the day was young, I had enough time to run home, make 10 of each and return to the range to fire off two five-shot groups. This time, I also grabbed my Caldwell G2 Chronograph on the way out the door.

After firing two rounds into the dirt to check my chronograph and warm the barrel, I fired my 20 test loads. While each charge weight produced groups that were nearly the same in size, I found that 78.0 grains have a better standard deviation, which was 38 FPS to the 74.0’s 97 FPS. I suspect that the fuller cases have a more consistent ignition because there was less room for the powder to shift around. Well, whatever magic is happening in there, I had two groups that were almost mirror images of one another, with the smallest measuring just .570” from center to center.
Results like this are typical, especially when high-quality components are used. Handloaded ammunition fits a chamber like a tailored suit fits an individual. For this reason, there is no other way to get accuracy like this unless you go after it with your own two hands. As I loaded another 100 pieces of brass for a long-range trip that I had coming up, a little voice in my head was whispering that I should play with seating depth, or perhaps try harder to source match-grade primers.
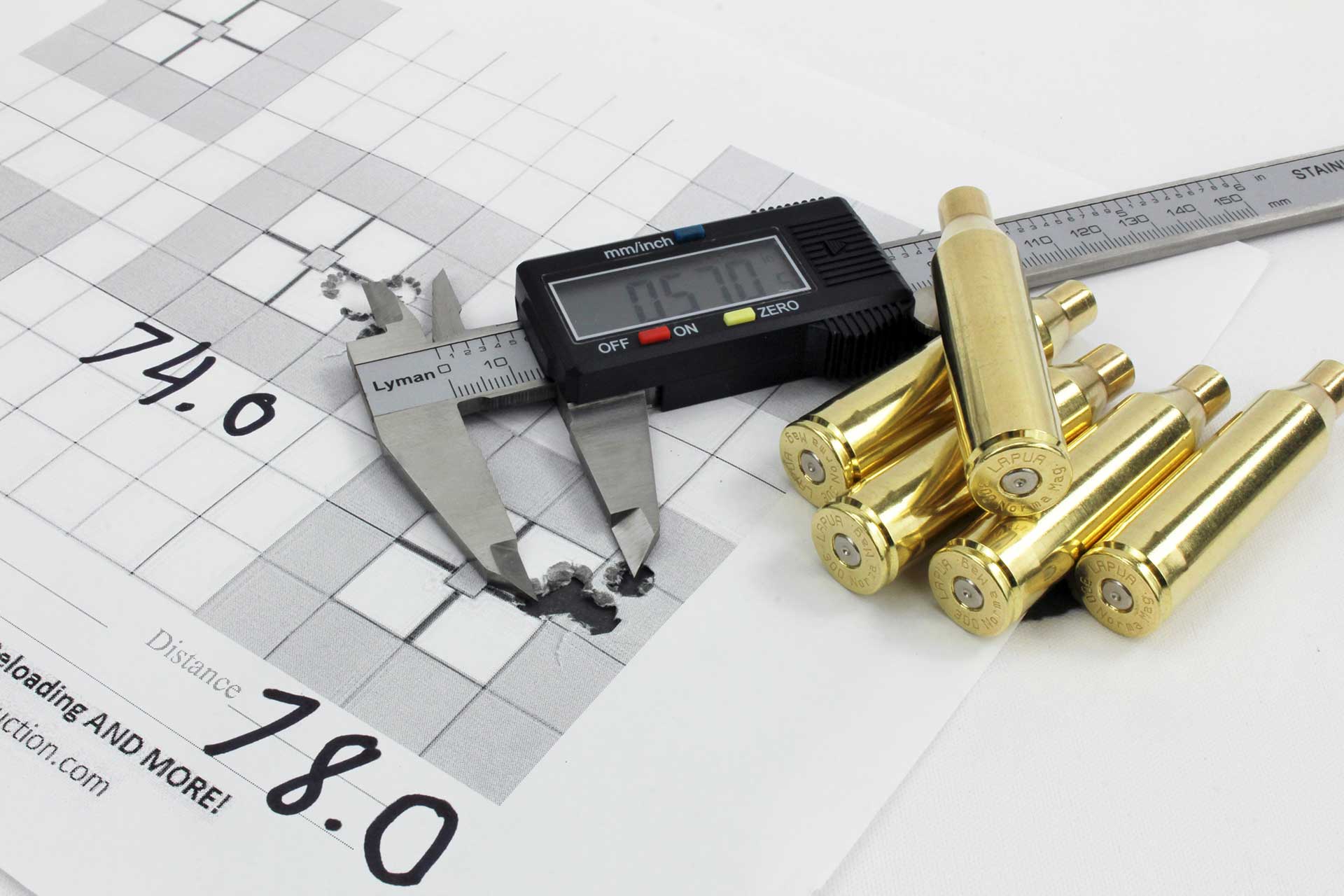
That same voice kicked in later in the reloading session and suggested I try .02 grains higher or lower to see if the group tightens even further. While that voice made a lot of sense, there comes a time when you have to decide whether you want to spend your time on the loading bench or the shooting bench. That has always been my struggle, and if you ask my closest friends, they will likely tell you that the only reason I shoot is so I’ll have brass to reload.