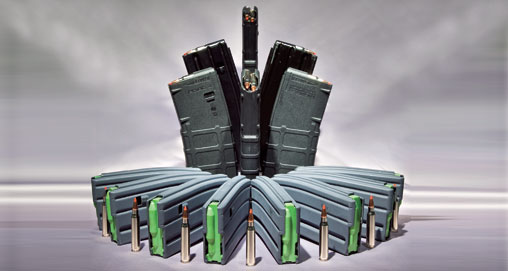
Cammenga EASYMAG
The Cammenga EASYMAG is distinguished from standard magazines by the way that it loads. The front portion of the magazine pulls downward, depressing the spring and follower, locking it into the lowest position. The cartridges are then loaded from the front. When the capacity of 30 rounds is met, the front of the magazine slides upward into place, releasing the spring and follower. The magazine is then ready to fire.
The EASYMAG has a continuous curve instead of the standard straight/curve shape. The continuous curve design allows the follower and track to remain in alignment throughout its entire range of travel, which results in less shifting and movement of the ammunition as it feeds out of the magazine. Cammenga believes the design contributes to the EASYMAG’s high level of performance in sandy conditions.
The follower performs the functions of compressing the spring, locking to the base plate, feeding the ammunition and pushing up the rifle’s bolt catch. The two samples I evaluated functioned as advertised. No malfunctions were experienced. It took some getting used to in terms of putting the rounds in the magazine. If the cartridges were placed improperly from the front, the base of the case would fall into the rib and would then have to be pulled out and set properly to load the next round.
Lancer Systems L5 Magazines
Lancer Systems of Allentown, Pa., produces one of the finest magazines available today. The L5 is unique, as the 30-round-capacity magazine is not all-polymer. The feed lips are steel and are molded into the plastic body. Lancer felt the steel lips would be an improvement, even though molding them into the body is a tricky process. Because of its translucent body and round-count markings of “20” and “30” molded into the magazine, the user can know with reasonable certainty how many rounds are in the magazine. The L5 uses the standard G.I. green follower, but, as of this writing, Lancer is working on an anti-tilt follower. The floorplate is rubber-covered with a large drain hole on the bottom. Disassembly is accomplished by pressing in two wings, one on each side of the magazine, which allows the floorplate to tilt out.
Last year, Lancer introduced two new magazines into its line, and the first is the long-anticipated 20-round magazine. The L5-20 uses a constant curve design, which veers away from the straight design as seen in the 20-round U.S. G.I. aluminum magazine. The other is the L5 Competition (L5C), which is a 48-round magazine intended for 3-gun competitions and the like, during which reloading costs time. The L5C uses a precision-machined aluminum coupler that accurately aligns 1 1/2 magazine bodies, ensuring constant curve shot columns. Lancer also produces a side-by-side magazine coupler as well as a floorplate removal tool for disassembly. I used this magazine extensively and had no malfunctions in several thousand rounds.
Diemaco (Colt Canada) Polymer Magazine
As early as the 1980s, several attempts had been made to make a reliable magazine out of polymer. Early efforts produced brittle magazines that were unreliable, as they were far more fragile than the aluminum magazines. The first successful attempt was by the Canadian firm Diemaco, now called Colt Canada. Development went poorly at first, as the units were rejected by the Canadian forces in favor of aluminum magazines. Not long after that, Diemaco completed the design and worked out all the bugs, producing the first combat-reliable synthetic magazine.
These Canadian polymer units are identified by the maple leaf on either side and should not be confused with aftermarket look-alikes. Diemaco has sold them to other military forces, including Denmark and the Netherlands. They have been used in many theaters of operation throughout the world. It’s unfortunate they are unavailable commercially in the United States, although some find their way here.
I have had several opportunities while visiting Colt Canada (Diemaco) to test its arms with these magazines and have had success every time. I have not experienced any malfunctions. These magazines were worth mentioning because of the pioneering work on Diemaco’s part in making the first successful polymer magazine for the AR rifle.
Beta Company C-MAG
The Beta Company was incorporated in 1983 and entered into an agreement with Leroy James Sullivan for the development of a higher-capacity magazine the same year. Sullivan was the designer of the 100-round C-MAG magazine, and he assigned all rights, title and interest in the C-MAG invention to the Beta Company in 1983. Sullivan made a metal prototype of the C-MAG, but there were no development or production activities until 1985. Starting in 1985, the C-MAG was developed by Beta engineers with only minimal initial input from Sullivan.
Production of the dual-drum, 100-round C-MAG for the M16 started in 1987. Through the years Beta made refinements, including changes in plastic material used for the drum housing to improve durability, variations in drum clip strap attachment to improve impact resistance, removable covers for easier disassembly, adjustments in the feed clip, the addition of linked spacer rounds for easier maintenance, and clear covers.
The C-MAG has served throughout the world. It is most effective in guns such as the Colt LMG and M4A1 with the heavy SOCOM barrel. The magazine is also best used like the Soviet drum magazines in defensive postures. Due to the way the cartridges rest in the drum they make a lot of noise when walking, running or moving. The drum I tested functioned flawlessly in a Colt M4 carbine.
Magpul PMAG
Although Magpul is a new company, it has created quite a name for itself with its polymer magazine, the PMAG. At the 2007 SHOT Show, factory reps were throwing them on the ground, stomping on them and grinding the heels of their boots into them to demonstrate the product’s durability.
An innovative feature of the PMAG is a cover that fits over the top of the magazine. It protects the feed lips from damage and dirt and, most importantly, when installed, pushes downward on the top cartridge, releasing tension against the feed lips. The benefit is long storage life for a fully loaded magazine. The cover can also serve as a feed lip gauge to determine if the lips are damaged. The PMAG 30-round magazine is designed for easy insertion into a rifle with a closed bolt. Some magazines are so stiff on the 30th round that it is difficult to insert the fully loaded magazine in the rifle. The PMAG also has a proprietary magazine follower that is 100-percent anti-tilt. Magpul has also introduced 20-round PMAGs in all the same colors as the 30-round counterparts, although they are not offered with the anti-tilt Maglevel system.
Currently, there are three different versions. The first is the standard PMAG, which is a solid color—the newest version permits the cap for the magazine to be attached to the base of the magazine. The second model includes the Magpul Maglevel system with two witness windows showing the number of unfired cartridges. When the orange mark on the magazine spring is visible in the top of the window, it is either empty or near empty. The third offering is called the EMAG or Export Mag, which has some design changes to the body to make it a more universal magazine with European arms that do not use the U.S. mil-spec magazine well, including the HK416, SA80 and Beretta rifles. It has a smooth exterior with one window on the left side, and it works perfectly well in the AR-15. MagPul offers its PMAG and EMAG in black, foliage green, olive drab, tan and orange.
MagPul PMAGs are the only magazines in my range bag and tactical gear. I cannot count the number of rounds that I have put through the magazines. The magazines have been in multiple rifles and I have never experienced any failures of any kind. PMAGs are in service throughout the world, including Iraq and Afghanistan. They’re gaining an incredible reputation for their combat reliability; many soldiers appreciate them and the potential exists for the PMAG to be the next standard-issue magazine for the U.S. military.
Magazines are one of the most important elements of any firearm design. They are responsible for the feeding portion of the cycle of operation. Even in the most proven arm that reliably extracts and ejects, the magazine has to be 100-percent reliable for it to consistently feed properly. Colt offered the semi-automatic-only SP1 AR-15 for commercial sale in 1963, the same year the U.S. Army adopted the selective-fire M16. Since that time, a variety of magazines have been made for AR-type rifles, and some are better than others. Due to the sheer number of manufacturers and variations, it is impossible to cover them all completely in these few pages, but here is a review of some of the best available today, including the specific characteristics and features that make them stand out.
Standard G.I. Aluminum Magazines
The mainstay since the introduction of the AR-15/M16 has been the aluminum magazine. Originally, the 20-round-capacity—later increased to 30-round capacity—aluminum magazine was intended to be carried pre-loaded and discarded after use. They were even listed in the military supply chain as disposable, but in reality the magazines were used repeatedly. Problems resulted because the lightweight aluminum was easily damaged from dropping or rough handling and, since they were designed to be kept loaded for limited periods of time, the top cartridge pushed on the magazine lips and eventually spread them apart, causing malfunctions.
There have been two iterations of followers for 30-round magazines: the original black follower, and the later green follower, which originated as a Marine Corps design. The latter was part of a reliability enhancement program for the M16A2. Because of the cyclic rate of the M16, it was possible for the bolt to push the cartridge into the front of the magazine. This, subsequently, could push the bullet into the cartridge case. To remedy this, the green follower featured extended legs at the front to keep it aligned with the magazine body. All G.I. magazines now feature this improvement.
According to some recent U.S. military reports, the most reliable aluminum magazines are Colt/Okay Industries magazines. Okay Industries of New Britain, Conn., has manufactured magazines for Colt since the 1970s. Okay has the capacity to produce more than 140,000 magazines per month, according its last completed government contract. A recent report indicated some other G.I. contractor magazines were failing to meet military specifications and were causing malfunctions because of out-of-specification dimensions and processes. During the early part of the Global War on Terror, the Army stopped shipments into theatres of war all manufacturers’ magazines other than Colt/Okay Industries. Colt/Okay units are identifiable by Okay Industries’ cage code “33710,” which is marked on the lower left side of the magazine body along with the month and year of manufacture. The floorplates are marked either “Colt” or “Okay.” Through the years I have had extensive experience with these magazines and have never had any issues with reliability, so long as they were not abused or left loaded for long periods.
Aluminum magazines may be on their way out of the U.S. military. There has been a requirement to replace them with polymer magazines, and Picatinny Arsenal in New Jersey is working on its own design as well as testing several commercial, off-the-shelf (COTS) magazines. The original 20-round straight magazines are still in production, but these are mainly used by shooters who have difficulty with the longer 30-round magazines when firing rifles from the bench. Additionally, 20-round magazines are well-liked by Special Operations troops with their Mk12 Special Purpose Rifles, as they enable lower prone-position shooting.
Heckler & Koch High-Reliability Magazine
The H&K High-Reliability magazine stemmed from the German company’s attempt to fix the horrendous deficiencies in the British SA80 (L85A1) rifle program—particularly with English-manufactured magazines. The design was carried over to both government and law enforcement sales as an improved magazine for the AR-15 platform and was later used by H&K with its HK416 family of rifles.
The High-Reliability magazine body is made of steel rather than aluminum and is coated with a special maritime finish to keep it from rusting. The coating also has self-lubricating properties in the inside of the magazine to aid feeding. The feed lips have the same strengthened design as the standard G.I. 30-round magazine. The profile of the magazine is somewhat different from a standard U.S. G.I. magazine with two bends. The H&K magazine features a constant curve that allows the cartridges to follow a natural path, increasing reliable feeding of the magazine. The steel follower is 100-percent anti-tilt inside the magazine body.
A rubber plug was inserted underneath the magazine behind the floorplate. Its purpose was to prevent unintentional release of the floorplate when firing the M203 grenade launcher without any rounds in the magazine. As one comes to expect with German engineering, these are the most expensive and, by far, the heaviest of the 30-round magazines in this lineup.