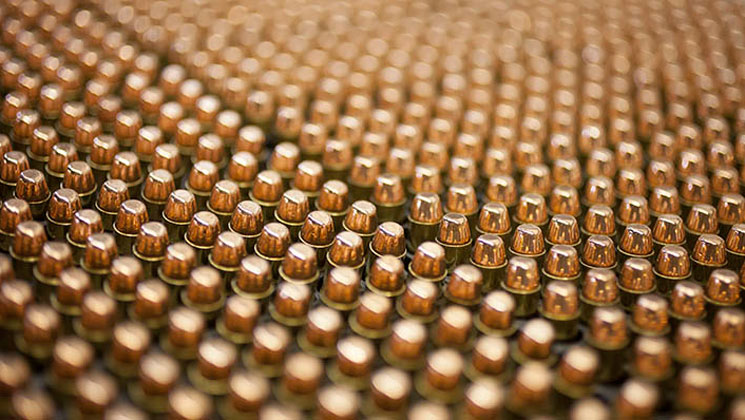
The firm opened its doors in 2013 in a modest set of buildings on the outskirts of Fayetteville, N.C. Brothers Huxley and Haywood Jones are the owners, with the latter sibling overseeing day-to-day operations and serving as company president. Both are former members of the United States Armed Forces and four of the seven employees are also veterans.
The small company escaped my notice until Aaron Cress, Director of Training for Force on Force Concepts, called. “I taught a two-day Glock New Equipment Training Course for four members of the U.S. Army Special Operations Command,” he explained. Each student went through 1,000 rounds during the training and, “To include my ammunition count for demonstrating the live-fire drills, we expended over 4,500 rounds of Defender Ammunition—we did not experience any malfunctions with the ammunition.” If you’re wondering, they were using the 124-gr. 9 mm load.
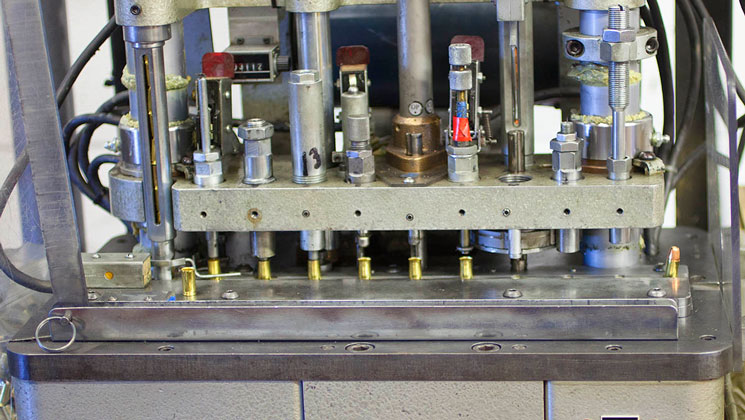
Defender Ammunition Company produces remanufactured cartridges, not reloads. Haywood’s appreciation for those who roll their own shows, but he emphasizes there’s a world of difference.
Most hobbyist reloaders are in it to save money, shave that last 1/10th of an inch off their precision rifle’s groups or help satisfy their budget-strapped friends’ range-time addiction. But, when center-fire ammunition on gun-store shelves was rarer than unicorn sightings down the freezer aisle, some amateurs burned the midnight oil to fill the void. Less-than-diligent hobbyists churned out the most, naturally, and that only increased the amount of sub-par fodder that found its way to the firing line.
Remanufacturing, however, is an automated process with quality checks built into every step. Defender Ammunition’s machines have the capacity to crank out 100,000 rounds a day, and still maintain the consistency shooters deserve. “Everybody is involved in quality control,” Haywood said.
The process begins with sorting and visual inspection of spent casings. Steel and aluminum goes in a barrel for recycling and brass that looks remotely tarnished suffers the same fate. It’s then tumbled to a new-ammo shine before pressure testing and manipulation to identify potentially dangerous imperfections. Those that survive the probes and prods and meet SAAMI specs are on their way to becoming a cartridge, an automated process that begins and ends with even more mechanical checks. The staff ensures machinery is calibrated by introducing a bad casing periodically, dutiful measurement of charges being dropped before and after each lot is run (including spot checks during the process), and I’ve never seen so many sets of calipers in my life (OK, once, but it was in an engineering class).
You’d be wrong if you assumed by the time it reaches the packaging department quality control is over. Here blemished cartridges that snuck by are pulled, and primers, casings and bullet seating get one last visual inspection. Any problems encountered are readily traceable to their source because, “Every load is checked and recorded by lot number,” Haywood explained.
That attention to detail helped the company’s sales increase by 200 percent from 2013 to 2014, and so far this year it’s experiencing another 100 percent of growth. Krissy Jones, Haywood’s wife, handles the office and phone. She said another key is the fact that, “We use all USA-made components.” Haywood’s accounting degree is serving him well in the venture, and he’s strictly adhering to a business plan gelled long before the centerfire shortage reached crisis
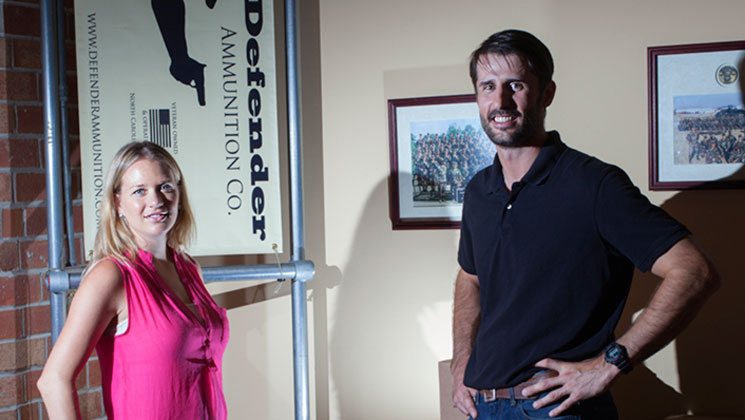
The day I visited, the youngest of their three children (10 weeks old) was in the office and didn’t approve of some of my questions. Well, the one about family, anyway. His presence provided the answer. Family run, veteran owned, made in America—small business is the backbone of this wonderful nation, and nowhere else is it more evident than in the firearm industry.