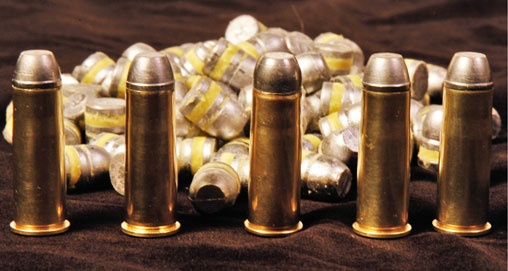
Parts 1 and 2 of Bullet Casting instructed how to choose and accumulate a supply of lead alloy and then turn that supply into raw bullets. Now it’s time to finish and load them into cartridges.
Sizing and Lubing
One advantage of casting bullets is that they can be custom-fitted to your individual firearm. Even with today’s super-accurate machinery there are tolerances in manufacturing. Sizing your bullets to match your gun will help ensure they fly to the same point on target from shot to shot.
Even with the relatively hard alloys we use today, cast bullets perform much better with some form of lubrication. Bullet lubes are as varied as the alloys, and like the alloys, each has its proponents who will vigorously defend the merits of their chosen lube over another. The easy way out is to purchase a commercial bullet lube, but those of us trying to save a buck often choose to make our own. Most bullet lubes utilize beeswax as a base, to which a softener is added—everything from Murphy’s Oil Soap to peanut oil and a lot in between—and finally a super-slick lubricant, which can be anything from molybdenum disulfide to STP oil additive. Those who wish to delve into the dark alchemy of bullet lubes and their recipes can explore to their heart’s content at the Cast Boolits website.
More Gear
You’ll need a few more tools to complete this project—a lubrisizer, the proper die and top punch and, of course, the lube. A lubrisizer is simply a tool that holds the sizing die, top punch and the lube (in a reservoir) and provides a means of running the bullet through the die while squeezing some lubricant into the grooves in the bullet. Lyman, RCBS, Saeco and Star all make lubrisizers that work well. For years I used an old Lachmiller lubrisizer, but today I use a slightly updated version of the same tool from RCBS.
Recall that I mentioned obtaining a supply of pure lead round balls in the calibers you shoot? Here’s why: They’re very handy for slugging the bore. In order to choose the correct sizing die, you should slug the barrel of your firearm. To slug your barrel, take a round ball as close as possible to the caliber of your gun; coat it liberally with gun oil, along with the barrel and push the ball down the bore. Of course, it’s always preferable to work from the breech, but you can still do this from the muzzle if you are careful. I start the ball with a brass hammer until just a bit of it protrudes, then I use the largest hardwood dowel that will run down the barrel and tap the ball through the barrel. Once the ball is a couple of inches down the barrel, give it a hard rap or two to ensure the ball upsets to full groove diameter. Make sure you have a soft rag for the ball to fall on so that it doesn’t get distorted as it exits the barrel. Measure across the top of opposite lands with a dial caliper or micrometer to obtain your groove diameter. Typically, you’ll want your cast bullets to be 0.001 to 0.002 inch more than the groove diameter, so order that size die.
The bullet you pour will dictate the top punch you need in the lubrisizer. As you look over the bullet mould catalog, the top punch is usually specified with the mould. The top-punch profile is important so that the front end of the bullet doesn’t get distorted during the sizing and lubricating process.
Running Them Through
Let’s say, for example, you are casting bullets for your .44-caliber revolver. One of the popular bullets for these guns is the Lyman 429421 semi-wadcutter designed by Elmer Keith. This usually falls from my mould at 243 grains, slightly less than the 245 grains it is specified. No matter, as long as they are consistent, they’ll perform splendidly. All of my .44-caliber revolvers—both Special and Magnum—have groove diameters right at 0.429 inch. Fortunately, my 429421 bullet mould drops bullets measuring .430 inch, so I am perfect at a thousandth of an inch oversize. I have a .430-inch sizing die that barely burnishes the riding diameter of the bullet as it injects the lubricant in the groove. This is a perfect setup because you do not want to have to resize the bullet if at all possible. The more bullet metal you have to move, the better the chance something can go awry and distort the bullet—and adversely affect accuracy.
All lubrisizers have a mechanism to put pressure on the lubricant in the reservoir, causing it to flow into the die through the lube holes and into the lubrication grooves of the bullet. Lubricants made for relatively high-velocity bullets—sometimes referred to as “rifle lubricants”—are stiffer than other lubricants primarily because of an increased ratio of beeswax to softener. These require more pressure in order to get them to flow, especially in colder shops. Some install a reservoir heater, available from Lyman, others use a heat lamp to get these stiffer lubes to work in their lubrisizers.
Assimilating Your Bounty
Most casters toss their ready-to-load bullets into a box until they need them. Most of the time that works OK, but there are a couple of considerations. Keep these bullets away from even moderate heat sources, lest the lubricant melt and fall out of the grooves. Also, if you are using a soft, sticky lubricant—like those used in blackpowder cartridges—consider using a storage box with individual cells for each bullet so the lubricant remains in the grooves. If you live in a warm environment and use soft lubes, consider storing your ready-to-load bullets in an outside refrigerator to keep the lubricant where it belongs.
I try not to keep a heavy inventory of cast and lubed bullets on hand. The reason for that is that the longer they stay out of a loaded cartridge, the greater the chance they can get bumped, nicked or dented, or lose their lubricant. For long-range rifle bullets where the need for accuracy is paramount, there isn’t a good reason to keep 2,000 of them on hand if you only shoot 500 per year.
Load ’Em Up
There aren’t a lot of differences in loading cast bullets over their jacketed brethren, but there are some things to keep in mind. First is, do not assume that loading data for jacketed bullets is interchangeable with cast bullets of equal weight. If you drive cast bullets at maximum velocity for a jacketed bullet, you’ll strip a lot of lead off in the barrel. At the very least this will have an adverse effect on accuracy, and if you don’t clean the lead fouling from the bore it can result in unsafe pressures.
I usually bell the case mouth slightly more for cast bullets. The reason for this is that all of the bullets I cast have square bases, and the larger bell lessens the chance of a base hanging up on the case mouth. These bullets require a square, clean base to get their best accuracy. I also don’t like having to straighten bent case mouths.
Cartridges used in repeating guns—revolvers, semi-autos and repeating rifles—need to be crimped firmly in order to prevent bullet drift within the case during firing. Most cast bullets have a crimping groove, but you need to examine it closely and ensure the bullet is seated just right in order to utilize that groove correctly. Specifically, that means to seat the bullet so that the case mouth is exactly in line with the top of the crimping groove. Rimmed and bottlenecked cases can be roll crimped—where the case mouth is turned inward within the crimp groove. Semi-autos, especially those that headspace cartridges the on the case mouth, perform better with a taper crimp. A taper crimp actually tapers the last fraction of an inch without turning the mouth over. Most die sets come with a roll-crimp die; if you want a taper crimp, you’ll need to purchase that die separately.
Keep an eye out for bullets starting to seat deeper during the loading process. Bullet lube can start depositing in the seating plug and push the bullet further into the case. A wooden toothpick can clear out the offending lube without disassembling the die and having to reset the seating depth.
If you haven’t shot cast bullets, it will open a whole new world of shooting to you. What I have presented here is just to get you started. There are ramifications and minutiae regarding alloys, lubes and heat treatment of bullets. As to the cost issue, I can’t truly argue that shooting cast bullets will save you money. Considering the tooling costs, the amount of money and time you spend scrounging lead alloys—or in some cases actually buying it—you’ll likely spend as much, if not more, money than you do now. But you should get more shots per dollar.