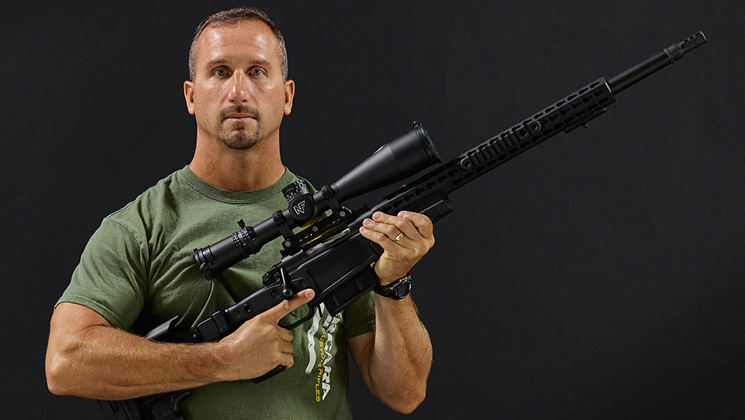
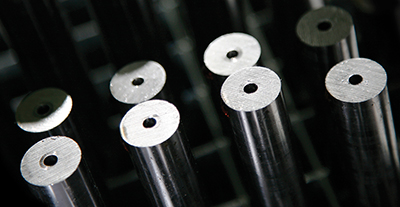
Dan Hanus, formerly a gun builder with the U.S. Marines’ Precision Weapons Section, brings hard-earned experience to BPI’s custom shop—where super-accurate builds start with only those barrels that pass his stringent quality checks (right).
Beginning in 1971, the Connecticut Valley Arms Co. sold affordable muzzleloaders to deer hunters. In 1999, CVA was purchased by BPI Outdoors and today remains its best-known brand. But that’s likely to change. The company, which is owned by Spanish parent Dikar, is undergoing a sea change in product diversity, manufacturing processes and, indeed, its entire approach to business. With significant investments in OEM barrel production, rifle actions, complete rifles and a Marine Corps armory chief who runs its custom shop, BPI is poised to impact much more than the blackpowder market. American Rifleman sent me down to Georgia for the scoop.
The Grand Tour
The full-body whitetail deer mount looked a little out of place in the cramped headquarters. This was no showroom, rather, the two corner offices and a dozen cubicles—along with a large warehouse and a garage-like custom shop—are home to 20 of the company’s 49 employees.
Dudley McGarity, the CEO of the operation, which is located just northeast of Atlanta off I-85 in Duluth, Ga., herded me into a small break room and pointed me to the jet fuel and donuts he’d bought for his crew that day. The flyer on the bulletin board read: “Company Fishing Trip, Sign Up Here,” followed by a dozen signatures. About then Nate Treadaway, president and chief operating officer, strode in and stuck out his hand, followed by 11-month-employee Taylor LeBlanc. Both wore the unofficial business casual Georgia-boy uniform of blue jeans, polished work boots and a plaid button-up. Treadaway looked awfully young for the president of a gun company. He told me he’s 42 and has been at BPI for 16 years.
“With our expansion into manufacturing, we’re looking to consolidate and move into a bigger facility,” he explained. “But for now we’re doing most of the machining at another location.”
Fifteen minutes later, I was hustled into another office building a few miles to the east in Lawrenceville, Ga. Right away I knew Production Manager Rick Wood was in a hurry because the next day was the turkey season opener. I studied the turkey fans and alligator teeth on his wall briefly before he ushered me into the manufacturing facility he operates.
I stepped up to the first CNC machine station and watched as 9 mm Luger pistol barrels were machined, checked for quality and rifled. The whole place was humming, but it wasn’t clanky. I told Treadaway that the janitor needed a raise, because I could’ve eaten my donut off the floor even if it were dropped chocolate-side down.
“Didn’t know you guys were into pistol barrels,” I said.
“Many people don’t,” Treadaway said. “We’re doing 20,000 this year, and a good many more in 2016.”
After walking by a dozen more CNC machines, inspection stations and cords of barrels in various stages of finishing (the blanks are made at BPI’s factory in Spain), we turned the corner and entered a full-fledged silencer operation. That’s right. Serving a growing market with products now legal in more than 40 states, the operation is a result of McGarity and Co. partnering with Mike Pappas (a founder of SilencerCo) and his newly formed company, Dead Air Suppressors. Before watching the 14-step process that involves CNC machining, computer-controlled MIG welding, Cerakoting, Stellite baffle assembly, polishing, inspection, serializing and laser engraving, I thought making a silencer was easy. I was dead wrong.
Meanwhile, Treadaway spat out numbers and the company’s production figures and goals like a talking calculator (I’m pretty sure he was a mathlete in high school), and my head began to spin. What registered is that BPI has come a long, long way from when it was selling muzzleloader kits at Cabela’s for $129—not that it doesn’t still do that.
As we turned to leave the production facility I noticed a distinctive barrel from one of the more unique AR-15 manufacturers out there—one that’s known for its expensive, accurate, large-bore rifles. Treadaway, per a non-disclosure agreement with the company in question would not confirm it.
“Most [gun owners] would be surprised to learn who we supply with barrels,” he said.
Then Treadaway wheeled and removed a polymer AR-15 magazine from the laser engraver and handed it to me, still smoking. It had my name on it. It was cool alright—and forever mine—but I’m not that easily impressed. I wanted to see his celebrated custom gunsmith build a rifle. Then I wanted to handle the new line of production rifles. And finally, I wanted to shoot them all and put a bullet or three through a silencer.
Back at the main office, Treadaway pointed me to a door at the far end of the hallway. Dan Hanus’ 30x20-ft. shop is lined with wooden work benches, hammer-and-punch-studded pegboard, leather padded vises and copious work lamps. There were a couple of tables on which various rifles lay. At one end was a lathe. All told, the shop looks like any small gunsmith operation in a serious hobbyist’s garage. But there were three men laboring, each leaning over a rifle, head and hands fastidious in effort, and they are more than mere hobbyists.
One of them looked up, wiped his hand on his apron, poked it in my direction and said, “Dan Hanus.” Finally, I’d cornered him. Over the next several hours, he not only told me how, but he demonstrated how he builds accurate rifles while also allowing a little about himself.
The Man In The Apron
“You absolutely must start with a good barrel,” said Hanus as he plunged an eye in a bore scope and twisted it while sliding it down a Bergara barrel he’d chosen from a pyramid of them moments before. It reminded me of a doctor inspecting a child’s ear for infection. “Then it’s all about mechanical repeatability.”
Honestly, I was surprised Hanus showed me his secrets—albeit the nugget about starting with a straight tube was hardly a revelation. Other steps to custom rifle building and accurizing, like testing the hardness of both ends of the barrel for consistency and his technique for finding the true center of the bore and cutting the chamber was wholly interesting to a pen-pusher like me. He told me I’d be surprised how many barrels from all manufacturers do not maintain the same Rockwell hardness throughout their length.
After 30 minutes watching him work, I got the feeling that Hanus was meticulous—no, rather, compulsive even as a child. Solidly built, confident and unassuming, he’s the guy who’s reserved around the dinner table until he’s asked something he knows. Then he comes alive with facts, while saving the BS for the after party. I wanted to know how one of the U.S. military’s finest sniper rifle builders came to be employed in a small custom shop in Georgia. I also wanted to know how he made guns accurate. In essence, I wanted to be Dan Hanus for a day.
Hanus, on the other hand, originally wanted to be a cop. Instead, the then-18-year-old from Fort Dodge, Iowa, enlisted in the U.S. Marine Corps and shipped off to San Diego. Hanus specialized as a small arms repairman and was so intrigued by it that he requested to be transferred to the elite Precision Weapons Section (PWS) located in Quantico, Va. His enthusiasm, however, proved premature. Hanus was denied entry into the school not once but three times—as are most who apply. This 45-employee “Ivy League of armorers” gunsmithing school develops personal weapon systems and builds deadly accurate rifles.
By the end of his enlistment, Hanus was a micron away from returning to corn country to become a cop. But instead the corporal got married and discovered that a police officer’s wage wasn’t a ransom on which to raise a castle and a couple kids. So he re-enlisted and became a recruitment officer for the Marines. As a reward, Hanus got to choose his next assignment, and for that he chose, of course, PWS.
“Our first test was to make a perfectly square 1x1-inch aluminum block,” Hanus said, “… using only a hacksaw, hand file, square and a black Sharpie.”
He passed, and four months later he was building rifles. To the chagrin of Iraqi insurgents everywhere, after three years of perfecting his craft, Hanus was deployed to Fallujah to maintain our snipers’ rifles. There can be no downplaying the impact his instruments had upon the cause—certainly his rifles contributed to the speedy demise of many a jihadist. At the request of our guys on the ground, Hanus modified M40/M40A5 rifles with detachable magazines. His wartime mods no doubt saved lives, although it also earned him some Marine-style discipline because he had done it without approval.
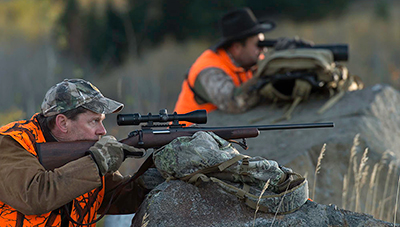
“It was worth it,” he said.
Nearly three years later Hanus returned home, unscathed by war and wiser in his art. As a veteran builder he returned to PWS as chief instructor and production chief, where he used his battlefield-based knowledge to enhance the M40 and M40A5 by way of a detachable magazine and other mods such as forward accessory rails. This time he did it officially—a big deal considering the red-tape-hampered pace at which the service’s arms evolve. He also worked on the Corps’ EMR (Enhanced Marksmanship Rifle) and M45 CQBP (Close Quarters Battle Pistol). While instructing at PWS, Hanus learned another trait that prepared him for corporate life: staff management and leadership.
After 22 years of service, Hanus retired from the Corps. Back in his blue jeans, the NRA Life member, avid hunter and pistol shooter attended a Brownell’s career fair, packing a resume. While there, he bumped into Mark Hendricks, vice president of technical development for BPI.
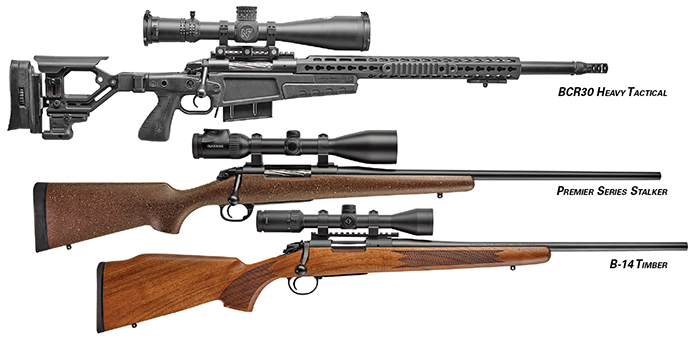
CVA, BPI and Bergara
Despite its foreign ownership, BPI’s products are conceived and marketed in the United States for American sportsmen. Most, excluding the muzzleloaders and barrels, are made here. In addition to CVA, Dead Air Suppressors and PowerBelt Bullets, its other brands include Quake accessories, DuraSight scope rings, Bergara barrels and now Bergara rifles. The brands are managed and marketed by the men I spoke of earlier—not slick guys in matador tights, but good ol’ boys who like to hunt, shoot, fish and eat chili dogs at Braves games.
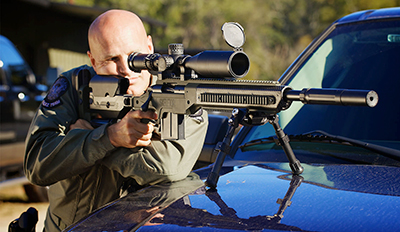
Around 2003 the muzzleloader market began to taper off, so McGarity looked for ways to sustain BPI’s growth. CVA was hamstrung by the growing price and the shortage of barrels it purchased from third-party suppliers. So he, Hendricks and Treadaway pow-wowed with Dikar’s execs. They had a manufacturing plant in Spain … what if they expanded it … and made their own barrels?
It sounds like a no-brainer, but there’s a reason only a handful of good barrel makers exist. It’s tough to do on a large scale with quality and consistency. Regardless, Dikar invested heavily in state-of-the-art CNC barrel machinery and hired legendary barrelmaker Ed Shilen to consult. What ensued was a computerized, repeatable system of milling, drilling, honing and rifling—i.e. barrel production. (McGarity credits its triple honing process as key to Bergara barrels’ accuracy.)
What BPI had now were quality barrels, manufactured en mass, produced exactly like it wanted them with no mark-up. It named its barrel-making company Bergara after the town in north-central Spain from which it hails.
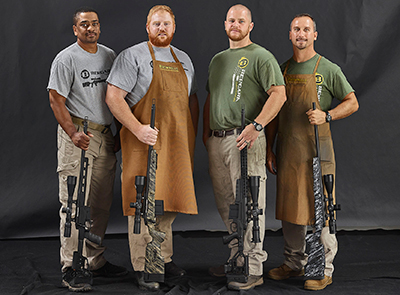
Soon Bergara rolled out muzzleloader barrels and center-fire barrels for its then-new line of CVA switch-barrel center-fires, as well as aftermarket drop-in barrels for its competition’s models, such as T/C’s Contender and Encore.
Then, in 2008, BPI found itself in an enviable position when guns sales and the tactical market boomed due to the election of Barack Obama. Sensing the demand, BPI mashed the gas pedal and began turning out barrels for many well-known gun makers, especially AR builders in dire need.
With Bergara rolling at full capacity, the trio devised yet another way to expand business. They suggested Bergara make custom guns to showcase the quality of its barrels, in much the same way Formula 1 race cars showcase an automaker’s capability. It sounded good in theory, but first they needed someone to oversee this would-be custom shop. So Hendricks ventured to the Brownell’s Career Fair.
“Up walks Dan Hanus,” Hendricks said, “with the perfect resume. He could build rifles, had his own personnel list and managerial experience. The only catch was, his resume was too good; he was out of our projected budget.” Hendricks paused for drama and leaned back in his chair before delivering, “But we hired him anyway.”
Hanus, in turn, hired a couple other PWS veterans and a guy who did gun work for the Department of Defense. Together they build Bergara’s custom rifles, inspect each other’s work, make repairs and fill orders.
I looked around Hendricks’ office that was cluttered with guns and triggers and stocks of all makes. On his desk was a naked rifle action that was employed as a paperweight. I inspected it. It was not a 700, not a 70, not a Mauser … .
“So the custom shop is rolling,” I said. “What’s next?”
“You’re holding it,” Hendricks said.
A New Action And Accurate Rifles
Turns out this pound-and-a-half forged hunk of 4140 chrome-moly steel has been some time in the making and the company’s biggest announcement since it founded Bergara.
Back in 2012, McGarity and company ventured back into the teepee. They noted that the trend in rifles during the past few years is to build them as cheaply as possible. McGarity believes Bergara can build quality rifles that perform and look better than the economy rifles from Savage, Remington and Ruger, yet he thinks BPI can build them relatively inexpensively—if it can make its own barrels and actions like those companies do. That way Bergara could better control its quality as well as costs. When McGarity told me this, I was naturally skeptical about his “pass the savings onto the customers” bit. But more on that later. At any rate, Bergara now has a new, robust rifle action, and while its viability as a benchrest and hunting rifle action for the ages will require time, it sure feels solid to me.
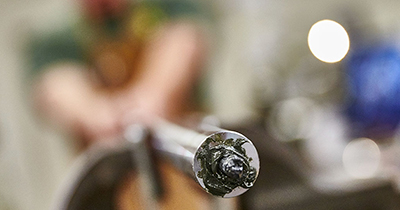
The action shares the Remington 700’s footprint, so it’s compatible with Model 700 aftermarket triggers and safeties. Yet it has several features the original gun lacks. The 16-oz. (short action) body is made by Bergara in America and features an extended collar that incorporates and conceals the recoil lug. It has an 8 1⁄16" overall length in short-action and 8 15⁄16" in long-action. Flimsy it is not.
Its bolt is partially made and assembled by a well-known OEM bolt maker whose name McGarity won’t reveal due to the maker’s existing contracts with other rifle makers. It features spiral fluting to minimize binding even when dirty, a floating bolt head to ensure perfect alignment to the receiver, a stationary gas shield, a sliding plate-style extractor, two locking lugs and a 90-degree throw. Hendricks told me the action will be standard equipment in two of Bergara’s three rifle lines.
Because this revelation was news to me, he explained that Bergara now offers three lines of rifles, all of which feature Bergara barrels. The Performance line features two rifles that both utilize the company’s Performance-branded action made in Spain. The walnut-stock version will retail for $950 while the synthetic will cost $825. The company will introduce a tactical version in 2016.
For $2,200, Bergara offers its Premier line including the BPR (Bergara Premium Rifle) 17 Tactical with an approximate No. 5 medium contour barrel and chassis stock, the BPR 16 Classic with a light No. 2 contour barrel and walnut stock and the BPR 16 Stalker that also features the light-contour barrel and hand-laid fiberglass stock. (The stock, I noted, looks just like a Brown Precision, and in fact it is, only it’s now made by High-Tech Specialties stock company.) All Premier rifles feature Bergara’s new Premium action and Timney trigger. All three of these custom-like production rifles are available in 6.5 mm Creedmoor, .308 Win., .270 Win., .30-’06 Sprg. and .300 Win. Mag.
Finally, the full-fledged custom guns that Dan Hanus builds are, except for the Bergara barrel, truly custom. Customers can pick nearly any feature à la carte, although certainly Hanus and custom shop manager Eric Hendricks will guide them on components they know to produce top accuracy every time. Custom rifle packages range from its 12.5-lb. Heavy Tactical rifle to its lightweight Mountain Hunter to a mid-weight, do-all Bergara calls its BCR 15 Long Range Hunter. At 8.5 lbs., it features a Bergara custom action, Timney or Shilen trigger, Badger bottom metal, McMillan A3 Sporter stock, metal bedding pillars and a Bergara-machined Picatinny rail. They range from $2,950 to $4,500 for the base models. But we all know rifles are more than the sum of their parts; it’s all about how they’re built. So, how are they?
“One at a time,” Hanus muses.
First he selects a Bergara barrel according to the customer’s contour preference on the order sheet, inspects its interior for flaws, tests it for hardness, chambers it, hand-laps it, trues it, mates it to an action and installs the trigger. The chambering and truing processes each take several hours of labor. Then the barreled action is fitted with bottom metal and pillar-bedded with Marine-Tex steel-filled epoxy in proven McMillian stocks unless the customer wants something else. The bedding process is Hanus’ forte and one he enjoys.
BPI Moving Forward
If Bergara’s new action and rifles do as well as its OEM barrel business, McGarity will likely have to hire new employees to fill the new headquarters, wherever in Georgia that may be. But for as many good moves as McGarity and the company have made, they are, of course, not without their share of mistakes. After all, this is the company that, in 2007, invested heavily in the production and launch of the Electra battery-primed muzzleloader. If you don’t see them on shelves, it’s not because they’re sold out. “It was received well by retailers,” said McGarity with a laugh, “but not so much by consumers!” The Electra was discontinued a few years later.
“Heck yes, we’ve made some mistakes,” said McGarity. But as in most avenues of life, learning from them often breeds positive futures.
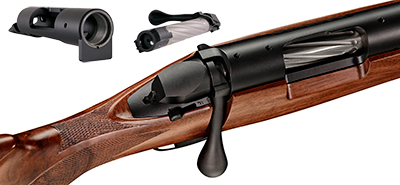
Right now business is booming for BPI, despite declining sales in some segments of the hunting and shooting markets. In May 2015 the Atlanta Police Department’s SWAT unit ordered custom Bergara Tactical Heavy rifles, all with the new actions. Then the Cobb County (metropolitan Atlanta) SWAT unit placed an order. The following day it became apparent to me why they did.
I turned in my second-best group ever while shooting prone off a wooden deck. The 100-yard group from the BPR 17 Heavy Tactical with a Dead Air Suppressor measured 0.23". With the other guns, including the Performance line, I dinged targets out to 500 yards from various field positions. They functioned flawlessly, and had a great feel. An $825 B14 Hunter produced some sub-minute-of-angle groups and felt like a much more expensive rifle. I especially liked the 6-lb., 11-oz. Premier Stalker; it averaged sub-m.o.a. groups with several types of ammunition. Its action was slick and, frankly, irresistible. So I asked McGarity how much it costs. When he told me $2,220 was the MSRP, I was surprised, because the 2015 catalog lists the rifle for a couple hundred more. Apparently he really is serious about passing on to the customer money saved by the company making its own action.
If it’s not obvious by now, I’m a big fan of BPI, because after years of using and testing its products in the woods and on the range, I believe it makes quality products at fair prices. In fact, when someone asks me what muzzleloader to buy, I suggest CVA’s Accura MR because I think it’s the best out there. It has wrested market share away from competitors not just by marketing, but because it’s accurate and affordable.
Time will tell, but I believe the old-guard gun companies are in for a horse race with Bergara’s new production rifles. And that’s a good thing for American gun owners everywhere.
For more information, contact Blackpowder Products, Inc., (800) 320-8767; bergarausa.com.