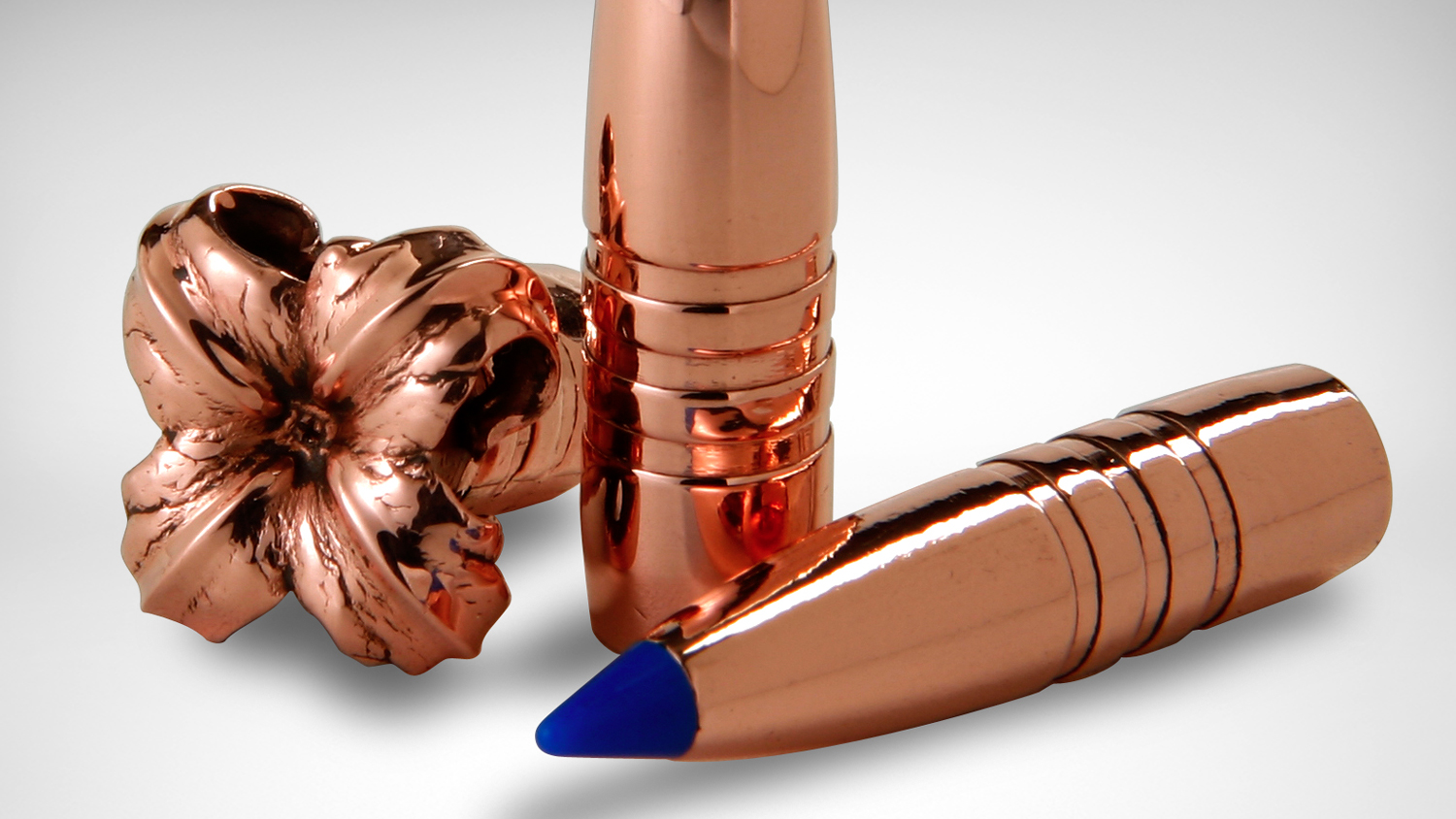
If not for sluggish demand for Southwestern jewelry in the early 1970s, a Utah cowboy named Randy Brooks might have become a noted silversmith. Instead he made his mark in copper. You could say that mark is an “X,” since Brooks’ signature achievement, the all-copper Barnes X Bullet, has greatly influenced contemporary rifle and pistol ammunition. In the 25 years since the X Bullet’s 1989 introduction, big-game hunters have come to expect previously unattainable levels of penetration, expansion and weight retention, factors that add up to superior terminal ballistics. Pistol and tactical shooters now have X Bullets to call their own, and several major ammunition and bullet producers have piled on the copper-bullet bandwagon.
After abandoning the jewelry trade, Randy and his bride, Coni, landed in their hometown of American Fork, Utah, and soon returned to a former avocation, loading custom ammunition. Just scratching out a living, the young couple shifted focus to a dormant specialty bullet company. Its founder, Fred Barnes, had for some time been encouraging them to rescue his namesake business from a new set of owners barely keeping it alive. Soon the family’s basement was doubling as a workshop where the elder Brooks and their young daughters, Jessica and Chandra, seated bullet cores in jackets.
Within a few years, Randy Brooks identified a need and developed a new dangerous-game solid, working through succeeding versions before settling on a copper-zinc alloy. The Barnes Solid built an avid following among safari hunters, and while the market niche was comparatively small, it garnered valuable attention from gun and hunting magazines to help put the company back on stable footing.
A big boost came from a 1980 American Rifleman article by Col. Charles Askins, Jr., who had contacted Brooks seeking solids for a Cape buffalo safari. Wrote the senior field editor: “In Africa, the professional hunter always glares at me suspiciously when I show him my so-called Barnes ‘solids.’ My stock answer to this is, ‘Just wait and watch, Bwana.’ I have shot 18 buffalo over the past three seasons … . Brother, let me assure you, these slugs really get the job done!”
Brooks was experimenting with lead-core designs, too, trying to devise an expanding bullet that would hold together without bonding and yet perform consistently over a wide spread of impact velocities regardless of the game animal’s size and angle. One attempt led him to revive the 1940s-era Controlled Expansion (CE) bullet, a collaborative effort by Fred Barnes and P.O. Ackley featuring an abbreviated lead core in the nose only, encapsulated within a unified jacket and shank. Though it penetrated well, the nose-heavy design produced poor accuracy and too often on bigger animals the bullet would “spit” its core.
While pondering the dilemma during a 1985 Alaska brown bear hunt, Brooks hit on a new thought: Why not get rid of the core altogether?
That was the easy part, relatively speaking, since Brooks simply started with common 3/8" solid copper rod, and then set to creating a drill bit that would create a conical nose cavity. After drilling the nose, he closed it up to form a point, leaving a narrow cavity extending in from the tip. Brooks then shot a few of his experimental .375-cal. bullets into water and, encouraged by the way they expanded, he decided Barnes was going to produce an all-copper bullet.
In fact, the trust in copper was part of the firm’s DNA going back to the Barnes Original. Rather than relying on the customary gilding metal alloy (95 percent copper/5 percent zinc), Fred Barnes had chosen to jacket his bullets in pure copper on the belief it made them less likely to fragment, thereby enhancing penetration. That competitive difference was a big reason why the company had once been America’s biggest bullet supplier to handloaders.
Brooks continued to work on his core-less concept, particularly in making it open up exactly the same way every shot. At times the expanded “mushroom” was off-center, an inconsistency that bothered the bullet maker. After much trial-and-error he came up with a hand punch that would score the inside of the cavity in four precisely equal sections. On impact, the result was four wide-open “petals” in the shape of an X. Though the sharp-edged petals curled back a bit, they expanded to roughly twice the original bullet diameter to form a lethal punch that destroyed tissue, smashed bone and caused incredible trauma.
For a final test, Brooks, mostly using hand tools, fashioned 20 of these all-copper bullets that would form an X upon impact, and headed back to Alaska, once again hunting brown bear.
He found his bear along a tidal beach and flattened it with a shot that broke both shoulders. “I knew right then this was going to be the future of our company,” he recalled. “I guess I was an eternal optimist, because it still didn’t shoot all that well. But I knew I would learn how to correct that.”
Though utterly convinced his revolutionary all-copper design would succeed, many obstacles blocked Randy Brooks’ way. Some of them, such as the need to improve accuracy, he readily understood, but there were others no one could have anticipated.
Thanks to its popular Solid and the market’s most diverse line of component bullets, Barnes’ sales were strong in the mid-1980s. Nonetheless the company was saddled with high-interest financing obtained at the height of Carter-era hyperinflation to expand its production workshop. That choked off resources needed for further development and tooling up to manufacture the new bullet. “Coni and I were not real smart about dealing with bankers back then. We persisted, but it was a challenge. It had taken me a long time to make those first bullets since we had no tooling to speak of and I just had to shape and score them in a crude set of dies, and did all the extrusions with a hammer and various punches I had made,” recalled Brooks. Moving to mass production would be a far different matter. “We had zero experience with impact extrusion, and I had no equipment for it. I bought an old 15-horse rotary index press and made some crude tooling. That’s how we made our first X Bullets.
“That proved to be a very long process,” said Brooks, “and we finally had to go to 35-ton transfer presses we got from Lake City Arsenal. Also we brought in a real tool-and-die maker to help me.
“We worked all of ’87, ’88 and into ’89 before we really started bringing the X Bullet to market,” said Brooks. “Those big presses ran about 60 [bullets] per minute, but the down time was just nuts.”
Though just a single raw material was involved, a crash course in metallurgy also proved necessary. “I started out thinking pure copper was pure copper,” said Brooks. “But in fact there are different grades of copper. Because I couldn’t compare it to anything in the shooting industry—gilding metal wasn’t conducive to what I wanted to do—I had to go to copper processors and talk to their engineers. I learned about grain size, the strengths of different grains and about the molecular lay of the grain. If it’s not right, it’s like scar tissue in the copper. The lay has to be a certain way for the bullet to open evenly and be strong enough. The engineers taught me, but at that time it was difficult to get the kind of copper we needed. However a couple companies began to make it for us because they could see we would become a good customer.”
When the product finally did emerge, early reviews were mixed. While penetration and weight retention were unprecedented, the new copper slugs also gained a rap for fouling bores and being inaccurate in some rifles. Critics voiced concerns about high pressures. “We weren’t one of the ‘good old boys’ of the bullet business,” said Brooks, “and so the X Bullet was treated quite badly. There was a lot of misinformation.
“The bullets in those early days had some problems, no doubt. But we also had people who really liked the concept, like our safari customers, who reported the bullets shot well in their rifles. And some writers came on board, too—Col. Askins; Ron Spomer from American Hunter; Ken Elliott and Craig Boddington from Petersen’s Hunting; and Handloader magazine—they all treated us very well, and we attracted a cult-like following that kept it going.
“I had to promote it a lot, had to reach out to all the writers and customers I possibly could and emphasize, ‘You need to keep your gun squeaky clean,’” said Brooks. “That’s what we learned from all the testing we do—at least 10 rounds out of every 5,000 made on the presses, we shoot for quality control.” In its campaign to teach shooters how to optimize the X Bullet, Barnes even introduced its own high-strength cleaning solvent, CR-10, which soon became a market leader in removing copper fouling.
An apparent solution came in the late-1990s with the surge in coated bullets. Molybdenum and other substances were used to treat bullet surfaces on the premise they would reduce friction, which in turn would lower pressures, raise velocities and decrease fouling. Promises of tighter groups, higher downrange energy and longer barrel life were abundant. Barnes went with a dry-lube treatment, XLC, adapted from coatings used to protect race-car cylinders.
Early results from the bright-blue XLCs appeared rosy. “It upped the ballistic coefficient and in my test rifle, they shot well,” recalled Brooks. “But across the board, accuracy was terrible. And then the whole moly-coating market went south, and so did ours.
“When that happened, I wondered, ‘What are we going to do now?’” said Brooks. Although the X Bullet had built an avid following, and was being offered in factory loads by high-profile companies such as Federal, Weatherby and PMC, the all-copper bullet remained suspect to some shooters.
“I thought back to a bullet we’d been making for a military application, a solid brass bullet. I had put grooves on it so it wouldn’t foul. That project was just a trial, nothing more, but that one simple step led to solving the two biggest problems that had plagued us from the beginning,” he said.
By producing X Bullets with prominent annular grooves cut into the shank, fouling abated and rifle-to-rifle accuracy was far more consistent. Copper displaced by contact with the lands could now “flow” into the grooves rather than melding onto the bore, and bearing surface area was reduced. That made it easier for X Bullets to shape themselves to each individual bore, as is the case with softer lead projectiles. Barnes settled primarily on a three-groove pattern and named it the Triple-Shock (TSX). Word spread via the shooting media, gun counter talk and campfire word-of-mouth, and interest in all-copper bullets spiked.
The X Bullet idea has since been adapted to a host of uses—muzzleloading, handgunning (hunting and personal defense), long-range tactical and more. Indeed, an entire X Bullet family now exists. The ground-breaking TSX begat the Tipped Triple Shock (TTSX), which, in addition, utilizes sharp polymer tips and deepened nose cavities to cut weight. That boosts velocities while maintaining respectable ballistic coefficients so that downrange trajectories are very flat.
Equally important, smaller calibers shooting lighter bullets are now able to perform tasks once delegated to bigger guns. Almost to a man, hunting guides have told me they approve of clients showing up with Triple-Shocks to shoot from their favorite deer and elk rifles. My No. 1 all-around load for anything short of moose and grizzly utilizes the 130-gr. Tipped Triple Shock in .300 WSM. At 400 yards, it drops just 12½ inches below point of aim (250-yd. zero) and still packs 1580 ft.-lbs. of knockdown energy. Before the X Bullet and its influence, it would have taken a heavier, harder-kicking .300 Wby. or .338 Win. Mag. shooting bullets no lighter than 180 grs. to yield that kind of downrange performance. The principle works especially well with the even smaller rounds appropriate for beginners, such as .260 Rem., 7mm-08 Rem., .308 Win. As such, we can ethically encourage novices to rely on rifles that are comfortable to carry and shoot for all but the very largest game.
Is it any wonder that practically all major ammo and bullet companies now produce or offer copper-based monometal projectiles? Brooks admits that he was initially angered by the copycatting, but reflects that ultimately it pushed Barnes to work harder to find new applications for the X Bullet concept.
If ever there was a quintessential American family business this was it. Husband, wife, kids, grandparents, aunts, uncles, cousins, neighbors—many hands pitched in to help the small-town bullet factory grow and prosper. And so the shooting industry was caught off guard in early 2010 when news hit that the company had been sold to Freedom Group (now Remington Outdoors). Soon after came the debut of VOR-TX, loaded ammo made to Barnes specifications and standards.
Though he now answers to corporate management, Randy Brooks still works at Barnes. He arrives early at the firm’s attractive new facility at the base of Mount Nebo near Mona, Utah, starting his day while the graveyard shift is still busy at the presses. He knows his workers, knows how to do their jobs and knows how to fix their machines if need be. In eleventh-hour negotiations with Freedom Group, at the risk of losing the deal, Brooks insisted his employees’ seniority benefits must be respected.
Coni Brooks no longer has to be a one-woman accounting/receiving/shipping dynamo, but she still has a full-time grasp on operations. Nowadays she assists daughter Jessica Brooks-Stevens, brand manager, who for years has guided the company’s classy, capable public image. Both women are skilled big game hunters, as made clear by the fabulous trophies on display at Barnes’ headquarters.
Looking ahead, the family behind Barnes Bullets won’t back off. Randy no longer must build his own hand tools, sift through countless iterations of every new product or count on intuition as his R&D blueprint. Now he works with engineers who employ computer modeling.
While Barnes remains devoted to serving hunters, it is equally excited about how all-copper bullets can empower Americans increasingly relying on handguns to protect themselves and their families. Brooks, an Army veteran, also is pleased by Barnes’ growing impact on national security. “Using X Bullet technology, we’ve been making products for our soldiers guarding embassies from suicide attackers. These men need a bullet that can penetrate straight through windshields,” he said. “We’re also making a frangible-core bullet for other military uses. It is designed to hold together while cycling through automatic weapons, but when it hits soft tissue, expands instantly and leaves a pair of smoking boots. If it misses the target and hits a harder object, it fails, no collateral damage. I don’t want to say too much, but these bullets are playing a big role in the War on Terror. They’ve been responsible for the deaths of some very bad guys. I get chills when I hear about those things. All of us here at Barnes are so proud that we can contribute in some small way.”