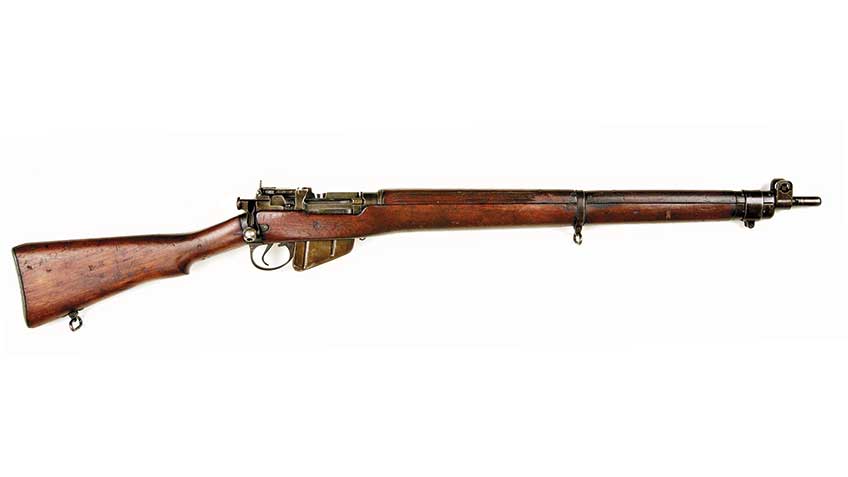
This article, "Exploded View: Lee-Enfield No. 4 Rifle," appeared originally in the April 2004 issue of American Rifleman. To subscribe to the magazine, visit the NRA membership page here and select American Rifleman as your member magazine.
In 1939, the British soldier was still armed with the same rifle his father, or perhaps even his grandfather, carried. The Short, Magazine Lee Enfield (SMLE) delivered sterling service from the mud of Flanders to the farthest reaches of the Empire. With Hitler's war machine on the move, the British needed an accurate, mass-production rifle. Thanks to inter-war development, an improved and simplified design was waiting in the wings, and the No. 4 Mark I rifle was adopted on Nov. 15, 1939.
The No. 4 Mk I, chambered in the same .303 British cartridge as the SMLE, retained the better features of the SMLE (in 1926, the SMLE was renamed the No. 1 rifle), but changes were made to the receiver, bolt, stock, sights, barrel, nose cap and bayonet. While being similar in appearance and features, very few parts were completely interchangeable between the No. 4 and No. 1.The No. 4's receiver was strengthened and squared off; requiring less milling and simplifying manufacture. A simple one-piece charger bridge to accept five-round stripper clips was fitted into grooves on the top of the receiver, as opposed to the No. 1's rounded bridge. The SMLE's complex-to-manufacture nosecap was discarded in favor of a milled, and later stamped, front reinforcing band and a simplified sight guard. The No. 4 also had a heavier free-floating barrel, which protruded from the fore-end and eliminated the need for precision full-length bedding.
No. 4s had four types of aperture backsights. The Mk I micrometer backsight was made of milled steel with a battle sight set for 300 yds., which when flipped up was adjustable for elevation out to 1,300 yds. The Mk II had a simple, stamped, two-setting aperture sight. The Mks III and IV were also made from stampings, but, like the Mk I, had provisions for sighting from 300 to 1,300 yds.
New government ordnance factories set up to produce the No. 4 were Royal Ordnance Factory (ROF) Fazakerley in Lancashire and ROF Maltby in Yorkshire. Birmingham Small Arms (B.S.A.) Gun, a private company, also established B.S.A. Shirley in Birmingham to turn out the No. 4. All three began producing No. 4s in 1941. Despite its role in developing the design, the Royal Small Arms Factory Enfield did not produce any of the 2 million-plus No. 4 Mk Is made in England during the war.
In early 1941, while America was still officially neutral, the British Government contracted with Savage Arms Corp. to build 200,000 No. 4 rifles at the former J. Stevens Arms Co. factory in Chicopee Falls, Mass. After the entry of the U.S. into the war, Savage continued to make the No. 4 under the auspices of "lend-lease" agreements. The lend-lease Savage-made rifles were marked "U.S. Property."
Long Branch Arsenal, located near Toronto in Ontario, Canada, produced about 330,000 No. 4 Mk I and I* rifles. In sum total, not only did North American orders bolster British production, but actually exceeded it during the war. The No.4 Mk I* was not actually adopted until 1946, despite being produced at the North American factories as early as 1941. The principal variation was in the method of bolt release. The bolt ribway had a new slot cut for the bolt head to be pivoted upward, out of the ribway. The machining at the rear of the ribway, the bolt-head catch, spring and plate were then no longer necessary.
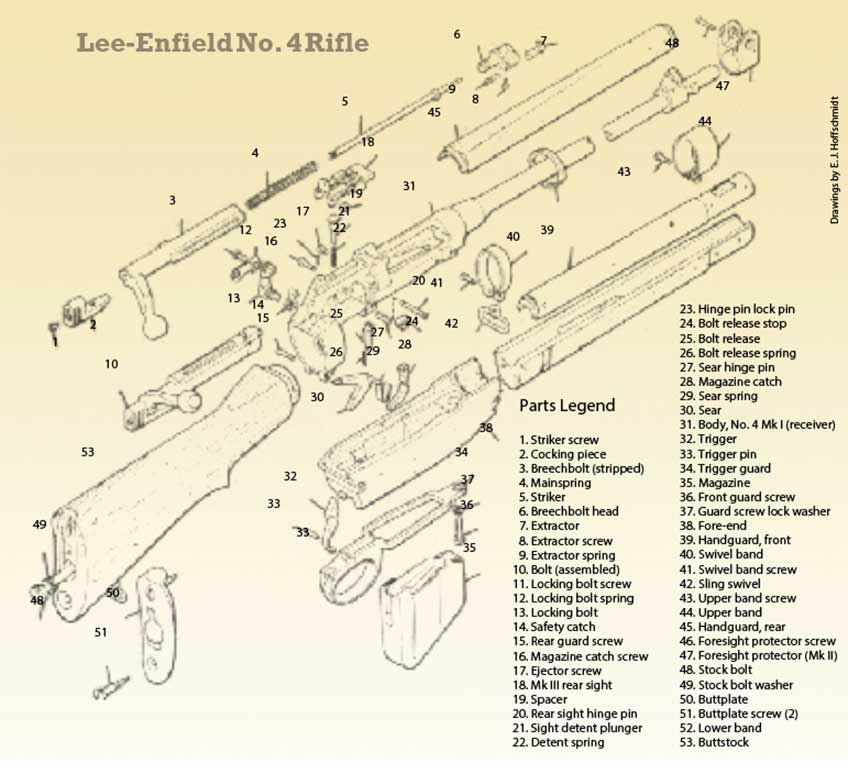
No. 4 Rifle Disassembly
Disassembly of the unloaded No. 4 Mk I begins with depressing the magazine catch (28) and removing the magazine (35). Open the bolt (10) and move it partially rearward, then depress the bolt release (25) and allow the breechbolt head (6) to ride on its rail over the release
(Fig. 1).
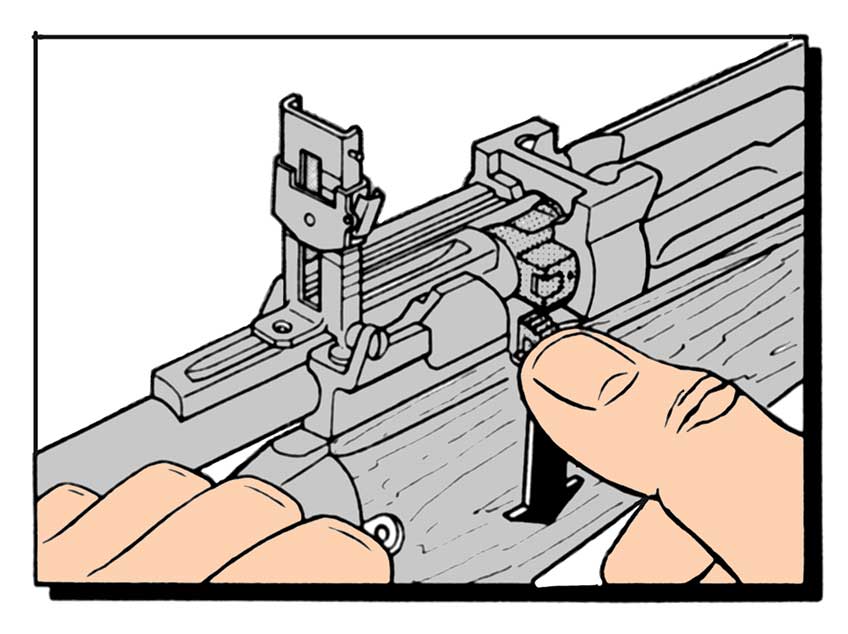
Rotate the breechbolt head upward and draw the bolt assembly rearward and out of the receiver (31). For the No. 4 Mk I*, open the bolt and ease it backward until the breechbolt head lines up with the recess in the bolt guide rail, rotate the bolthead upward and remove the bolt to the rear.
(Fig. 2). It may be necessary to flip the backsight (18) to allow the bolthead to clear the receiver on both the Mk I and Mk I*.
Turn the breechbolt head counterclockwise and off the breechbolt body. Twist the cocking piece (2) until it moves to the lower of its two notches, taking most of the compression off the mainspring (4). Turn out the slotted striker screw (1) on the rear of the cocking piece.
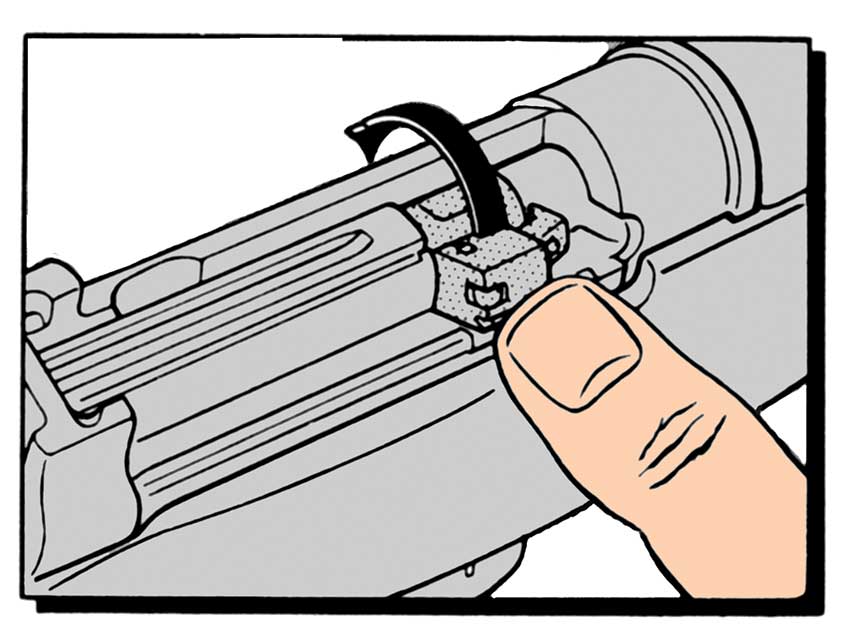
The striker (5) is screwed into the cocking piece. There are two notches on either side of the strikerユs shoulder about 1” down from the strikerユs tip. To remove the striker, insert a takedown tool from the front until the projections on either side of its point engage the notches. Then, simply turn out the striker (Fig. 3).
Fore-end (38) removal begins with unscrewing the front band swivel screws (41 & 43) and removing the two front barrel bands (40 & 44) and the front sling swivel (42). Next, turn out the front guard screw (36) and the rear guard screw (15), allowing the trigger guard (34) with the trigger (32) attached to be pulled off of the fore-end. The fore-end is now free to be pulled off the bottom of the barreled action.
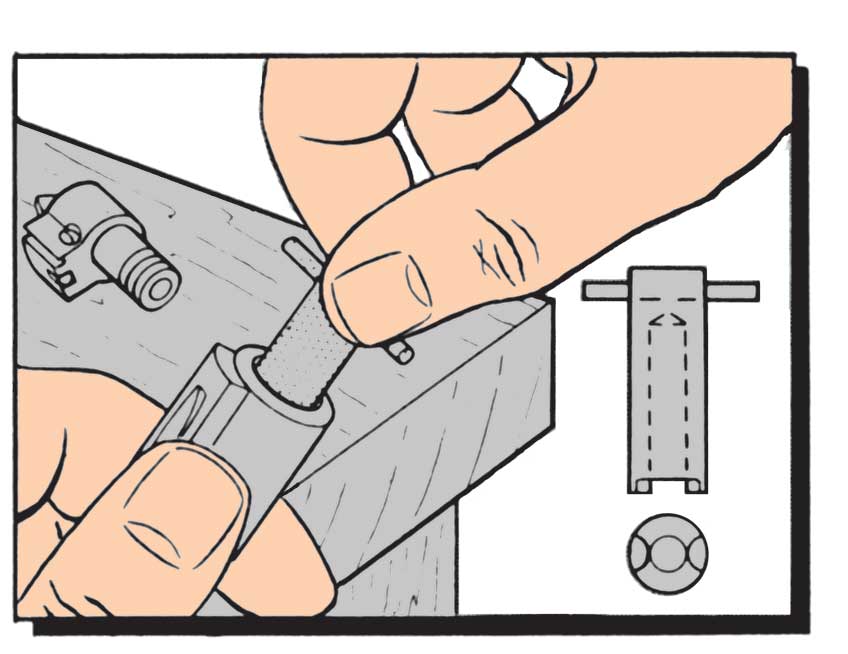
To remove buttstock (53), flip up the buttplateユs (50) trap, insert a long-bladed screwdriver into the recess in the buttstockユs rear and turn out the stock bolt (48) and its washer (49).
Reassembly is in the reverse order.
Editor's Note:
No. 4 rifles have comprised some of the largest batches of surplus guns to ever come into the United States. Many early rifles were imported through Interarms and Century Arms International, starting in the 1960s and continuing into the 1990s. Royal Tiger Imports has imported the most recent batch of No. 4 Lee-Enfield rifles, which were discovered in storage in Ethiopia. You can read about the discovery here.