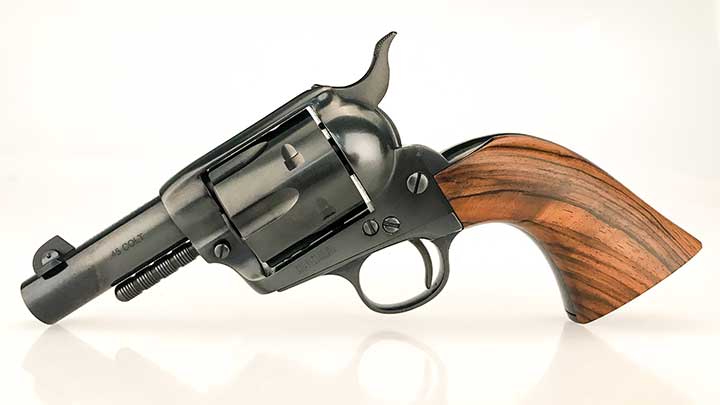
The old Colt was new in the first year of the 20th century. On March 21, 1901, when Colt's shipping department closed the package, this and nine other Single Action Army revolvers headed for needy frontiersmen in New Mexico territory. Serial No. 207264 was a blue-steel .45 Colt with a 4.75" barrel, a common and popular version of the classic revolver.
The century may have been new, but the established sidearm of the time was the Single Action Colt, which had 30 years of history in the Indian Wars. The Colt came in many variations of finish, caliber and barrel length. The variation that somehow managed to capture my interest was the gun that collectors called the “Sheriff's” or “Storekeeper's” Model. Colt called it the ejectorless model.
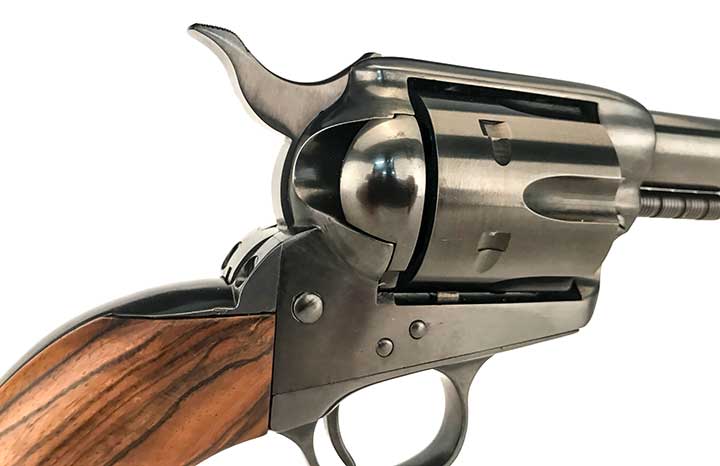
In those long-ago times, Colt was willing to customize its revolvers, and several batches of SAAs materialized with no ejector rod and housing on the lower-right edge of the barrel. Most of these guns had shorter-than-usual barrels. For some reason, this simpler, cleaner mechanism appealed to more than a few shooters, although it required another tool to poke out the empties.
This interest carried over to the post-World War II re-introduction of the SAA Colt. I was one such budding handgunner in the 1970s while working as a southern California peace officer. I found Serial No. 207264 (hereinafter referred to as No. 64) in King's, a famous southland gun emporium. Yeah. I bought the old brute.
No. 64 may have started as an entirely normal 4.75” .45 Colt with the fit, finish and case-hardening to die for, but that was in 1901. By 1979, it was a ruin—re-blued at least twice. It may have passed through many hands in 78 years, but none of the unknown number of owners would seem to have had sufficient monies to defray the cost of a bore brush and rod. After a couple of lengthy and diligent cleaning sessions, I had to accept that No. 64 was a lost cause.
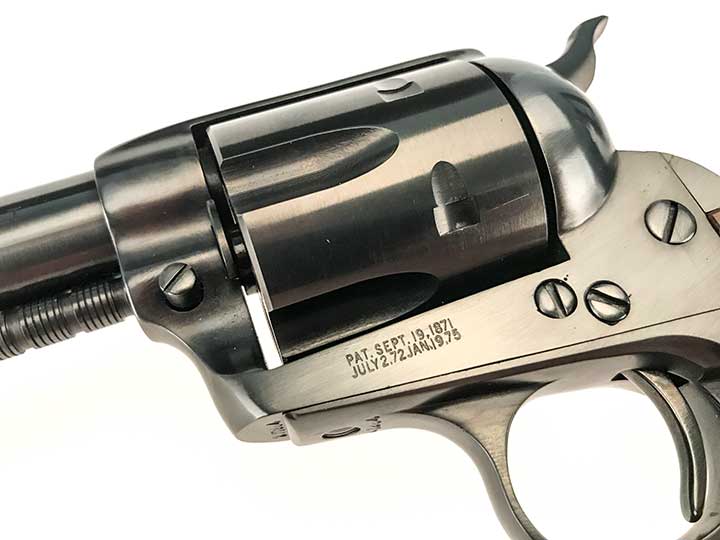
Some previous owner had apparently reached the same conclusion and decided to sacrifice the gun to experimentation. He removed and discarded the ejector rod and housing, then cut the barrel back to 3 inches. Worse than that, he cut and welded the front of the frame to do away with the loop that accepts the rear edge of the ejector rod housing. The gun could not be returned to original SAA configuration. Oh well, I bought it as a Sheriff's Model anyway—I just wanted a shooter.
Dressed in a light coat of grease and zipped into a proper gun rig, No. 64 rested easily in a big Browning safe for many years. Other SAA Colts would come and a few would go, but this one just lingered on. Then one day several years ago (and decades wiser in the custom gun field), I was looking for something else and ran across No. 64. Although the major shooting parts—barrel and cylinder—were a total loss, the frame, lockwork, butt and grips were not too bad. After all, it was an original Colt SAA with matching numbers where they were supposed to be—frame, butt and trigger guard.
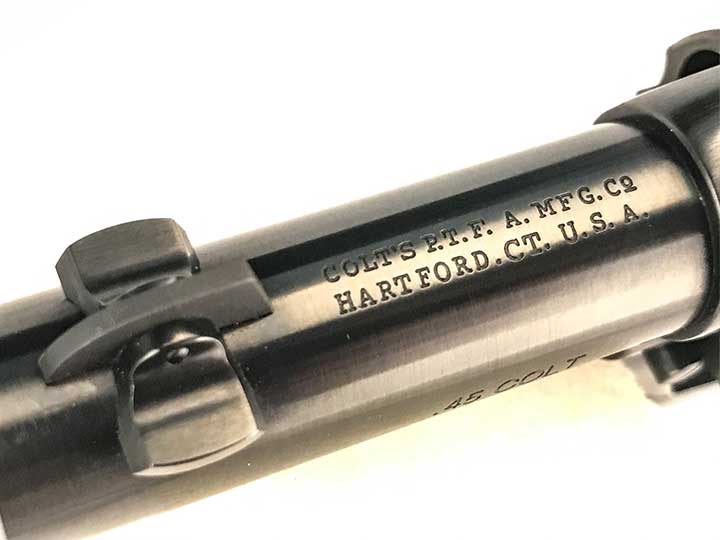
Always, I had been drawn to the clean good looks of a Sheriff's model, and that may have been part of the reason that No. 64 had not been summarily dismissed from my armory. A restoration just might be in order. I'll admit that I was puzzled with what the frontiersman armed with one of these things used to punch out the empties. Not likely to have a pencil in his pocket, nor a section of hardwood dowel. Certainly not a BIC pen.
I needed to resolve this dilemma before attempting a resurrection of No. 64. Several European revolvers, both SA and DA/SA, have a sort of folding ejector rod that went into the central axis of the cylinder. That would seem to be the only available space on the gun. Old No. 64 lived on my desk for several months while I did make-a-living work and fooled with the gun on breaks. Then one day—with no fanfare whatsoever—an idea came to me.
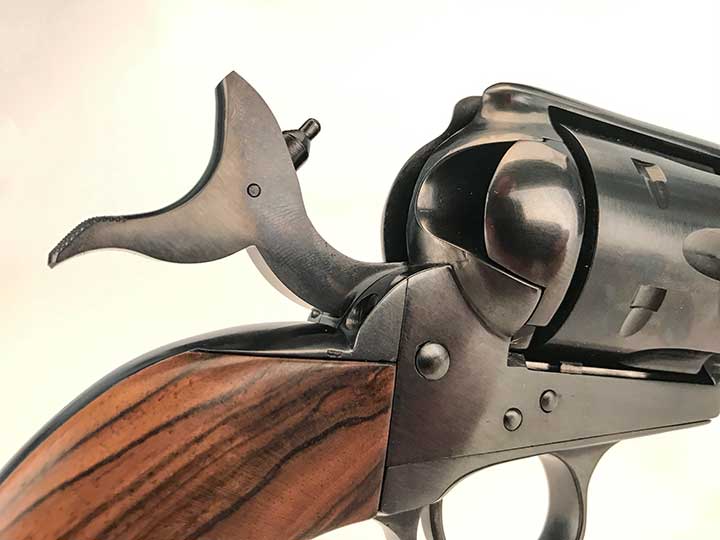
A Colt Frontier Model has what is called a base pin. It is literally the axle on which the cylinder turns. Early SAAs used an angled screw to hold it into the frame, but later (and current) guns have a spring-loaded latch that holds the base pin in place. When you take the cylinder out to clean one of these legendary revolvers, you pull the base pin forward out of the frame.
In doing this, I noticed that the pin itself—a steel rod about three inches long and a quarter inch in diameter—would make a great tool for punching out brass. If you pulled it out of the frame, however, the cylinder would be loose and would fall out of the gun. It occurred to me that a machinist with lathe skills might be able to make a special base pin. I carefully worked out my idea and made what I thought was a workable drawing of the modification that would get it done.

I took the gun and the drawing to my friend and ace pistolsmith Terry Tussey of Tussey Custom, who gets the credit for making a reality of the Trython and other custom handguns. I admit that his response to my design and idea was, to say the least, deflating. He looked at the drawing for about, oh maybe 10 seconds. Then he grunted something about “won't work—we'll do it this way.” The next time I came by his shop, he handed me a working version of the idea.
On the finished gun, the shooter moves the hammer to the “half-cock” position and opens the loading gate. Then he presses the base pin latch on the front of the frame and pulls the base pin forward and out of the gun. The cylinder remains in place and capable of turning as normal. Our pistolero now uses the base pin as a punch to reach in the chambers and push empties out of the gun in sequence. When he needs to load up for a stroll down Allen street, he pushes the pin back in place in the gun. It works.
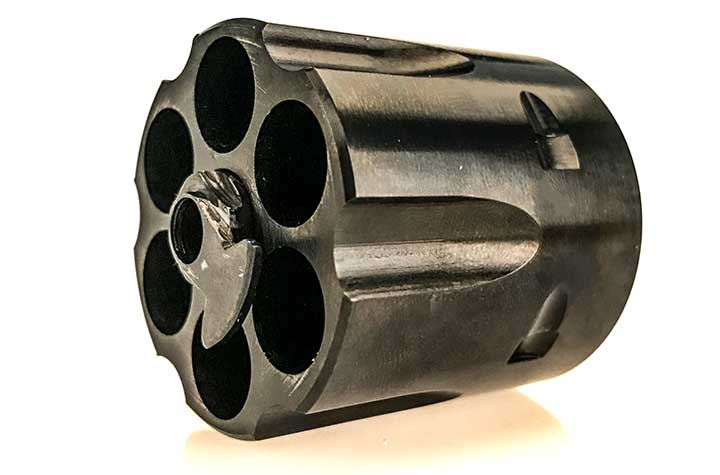
I will admit that the first time, we worked with a much used replica single action that I picked up at a local gun show. Terry gave this project to Steve Duell, one of the well-qualified pistolsmiths working in his shop. It came out perfectly on the recent production SAA, so we went ahead and made the modification to old No. 64.
When they did that one, I was so pleased with the result that I had to do it up right. Terry was backed up with other work and couldn't complete a total renovation of my Sheriff's model, so I appealed to Hamilton Bowen of Bowen Classic Arms. Bowen is well-known in the world of wheelguns and has done special projects for me on other occasions.
Bowen got No. 64 with the base pin modification we have just examined, but no other work performed. Both barrel and cylinder were in terrible shape with deep pitting. Bowen offers a special dovetailed-in front sight that replicates the ones used by Sedgely and other pre-World War II 'smiths. He fitted one to a special barrel on No. 64.
To get a little heavier-than-normal barrel, he made a new barrel from stock. The cylinder was also new, but not the original caliber. At my request, the new cylinder was chambered for the .45 ACP cartridge. I am uncommonly fond of.45 ACP revolvers—as opposed to .45 Colt—simply because of the cost of ammunition. I can almost always find cheaper .45 ACP ammo.
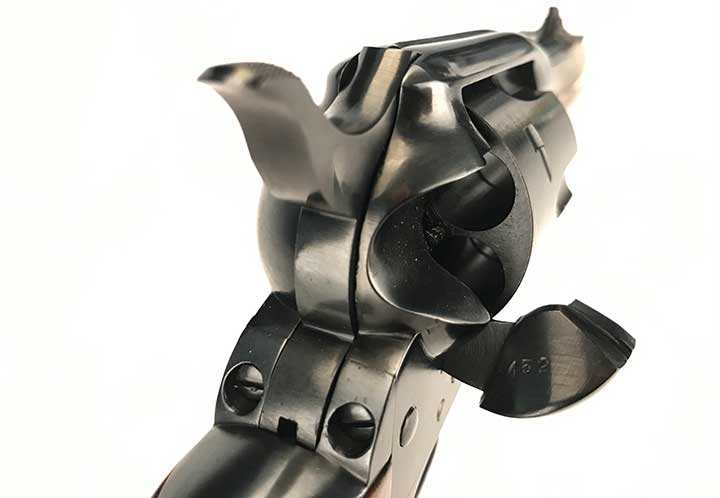
Bowen's accomplishments thus far described made the gun a great new shooter, but what he did for the cosmetics made it no small triumph of the gunmaker's art. Hamilton Bowen has developed a technique of preparing steel parts that results in a subdued luster to the final blue job. He did not case-harden the frame, but rather just blued it.
He also had to pretty well rebuild the action in order to finish it up properly. I sent the gun to Joe Perkins at Classic Single Action in Tucson for one-piece style grips. Joe selected a piece of walnut where the natural grain mirrored the classic butt curve. It is an uncommonly handsome little custom revolver.