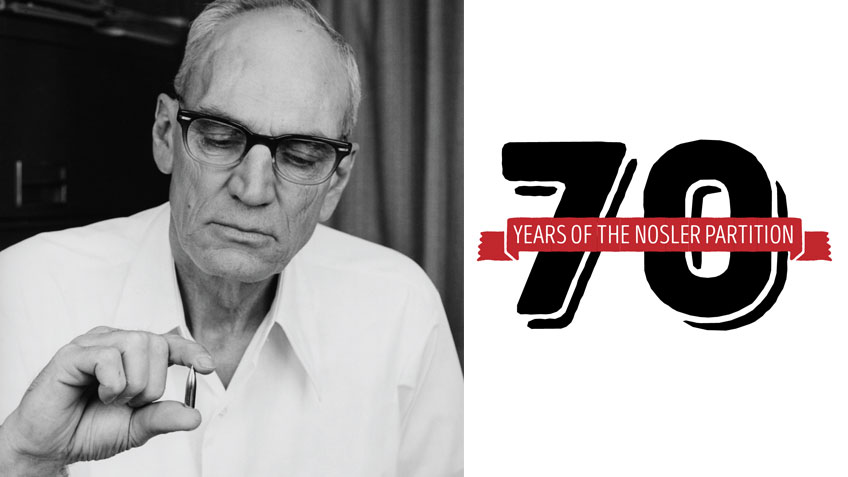
Just as necessity is the mother of invention, John Amos Nosler became the father of the Partition bullet and the company and legacy that bear his name. In 2007, Nosler’s work earned him the first-ever NRA Publications Golden Bullseye Pioneer Award. He died in 2010 at 97.
If not for a British Columbia moose wearing a thick coat of mud from his favorite wallow, we probably would not have the Nosler Partition bullet today. All but the tips of the animal’s antlers were concealed by dense willows, so the hunter—armed with a Winchester Model 70 in .300 H&H Mag.—had to sneak “uncomfortably close” in order to thread his bullet through a screen of brush. Even with perfect bullet placement, it often takes a moose quite some time to discover it is dead, and this one was no exception. Only after taking seven bullets did the great animal decide to give up the ghost.
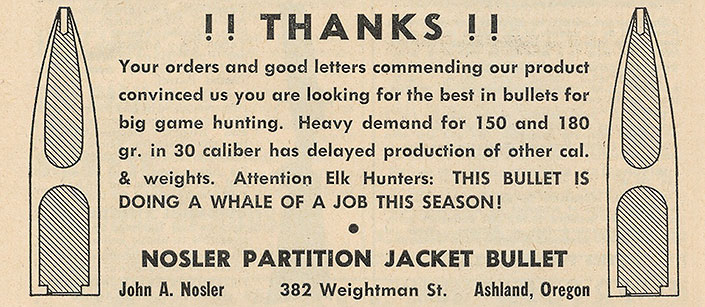
An excellent marksman with a drawer full of competitive shooting awards back home to prove it, the hunter felt confident that his bullets had been placed where they should have gone. And they were. Bullets recovered while field dressing the animal showed excessive expansion at close-distance impact velocity, which resulted in inadequate penetration on such a large animal.
But that was only half of the story. Another moose shot with that same brand of bullet during the previous season almost got away. A straight-on shot at several hundred yards, the bullet was placed dead center of the chest and, failing to expand at all, it traveled the full length of the animal while leaving behind a very narrow wound channel. Only after four hours of tracking was the bull located and finished off. At that point, the hunter had thoughts of returning to his old .30-40 Krag, but he had grown quite fond of the greater reach of the .300 H&H Mag. and decided an improvement in bullet performance was the answer.
The hunter in this story was John Amos Nosler, and his search for a better big-game bullet began soon after he returned to his Ashland, Ore., home in 1946. His goal was a bullet capable of consistently expanding to a larger frontal diameter at long range where impact velocity has dropped off, while retaining enough weight and sectional density to penetrate deeply at close range where impact velocity is high, even when heavy bone is struck. In other words, a bullet that would reliably expand when striking soft game, such as deer and pronghorn antelope at great distances, while also being capable of driving deep on heavy game, such as moose and elk. The solution to the problem came in the form of a jacket with an integral partition separating front and rear lead cores.
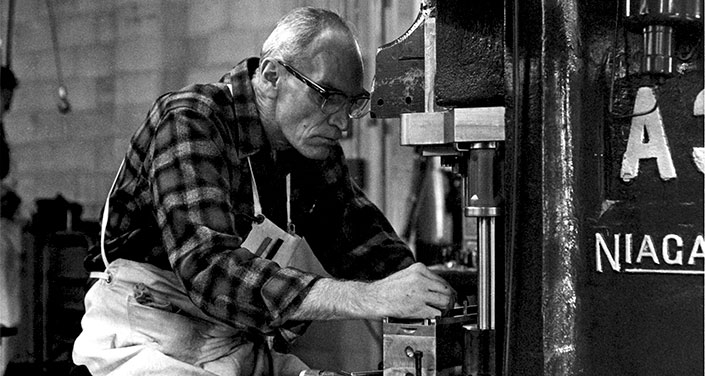
Using a lathe in a corner of his small shop, Nosler turned sections of copper rod to a diameter of 0.308" and, after it was cut to the desired lengths, cavities drilled into both ends were stopped short enough to leave a solid partition between them. Serving as an expansion arrestor, the partition would retain a high percentage of a bullet’s original weight. To aid expansion of the front section, a tapered reamer was used to thin the front end of its wall while leaving it thicker back toward the partition. The front and rear cavities of the first batch of bullets were filled by hand with molten lead, and after the cores had cooled, dies in a hand-operated press were used to swage the bullets to their final shape. Those first bullets were hollowpoints.
In 1947, John Nosler headed back to British Columbia for moose, this time with handloads containing his own bullets. He was accompanied by friend Clarence Purdie, developer of various handloading items including the Bonanza Co-Ax press, which is still available today from Forster Products. The plan was to give the bullets the ultimate test by placing them into the shoulder area where they would likely encounter heavy bone. Using a rifle in .30-’06 Sprg., Purdie dropped his moose with a single shot and, in doing so, became the first person to bag an animal with the new bullet. When John Nosler’s chance at a moose came, he managed to get inside 25 yds. for maximum impact velocity from his .300 H&H Mag. If anything would defeat his new bullet, that would. Perfectly expanded bullets with high weight retention recovered from those animals served as proof that Nosler was on the right track.
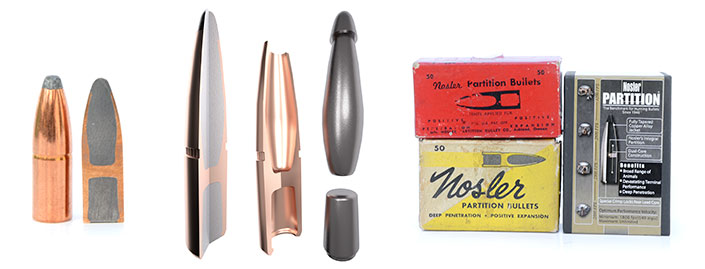
Filling the front and rear cavities of the jacket with molten lead was replaced by the insertion of lead slugs, followed by swaging them in place. Considerable hardness of the jacket, along with its solid midsection, caused pressure issues, and several different styles of bullets were tried before the problem was eliminated. One was a two-diameter design with the rear section matching barrel groove diameter (0.308") while the forward section was bore diameter (0.300"). The final solution was to cut a relief groove into the jacket over its partitioned area. Additional field tests by Nosler and several of his friends on other hunts served as further proof that his design was sound.
At the time, John Nosler owned a successful trucking company, and he had no desire to get into the bullet-making business. But he did want to see his idea go to market, and he expected to be paid for it. Frank Snow, Jim Spivey and Loren Harbor had only recently started a new shop in Whittier, Calif., called Sierra Bullets, so John went calling on them. While they were impressed enough to ask him to become a partner in their company, it did not work out. Vernon Speer—who had started making bullets bearing his name in the basement of his Lewiston, Idaho, home in 1944—was also interested, but his machinery was incapable of making the partitioned jacket. After applying for a patent on his design, Nosler visited with a Winchester executive who considered his bullet too complicated to make at a profit.
Convinced his design would sell, Nosler made the decision to sell his trucking company and invest the money in making bullets. But he first had to learn how to make them faster than by hand. While he considered himself a good machinist, design engineering skills that he did not have would be equally important. In addition to hiring an engineer, he spent enough midnight oil on books to eventually become one himself.
The Nosler Partition Bullet Co. was founded in 1948, and its first advertisement ran in The American Rifleman during that year. Those first bullets, 150- and 180-gr. .30-cal. hollow points, were packed 50 to the box by John’s wife Louise, who along with their son Ron also handled shipping, bookkeeping and other chores. A price of 10 cents per bullet made them about twice as costly as bullets available from other companies, but it did not take hunters across the country and around the world long to learn they were worth every penny.

Up until 1952, the jackets of all Partition bullets had been made from copper rod, and during that year a switch was made to tubing consisting of 90 percent copper and 10 percent zinc. An automatic screw machine cut the tubing to the required length and tapered the wall at the end that would become the front of the bullet. Then, opposing punches in a hydraulic press simultaneously reached inside each jacket from both ends to displace enough material to form a partition where they met. This forming method left a small hole in the center of the partition. Another machine cut a relief groove into the jacket at the partition. The hollow-point style was replaced by a soft point with the front core exposed at the nose as seen on the Partition bullet today.
The change in process sped production, and while all went well for awhile, obtaining tubing that met Nosler’s high-quality standards eventually became impossible. Bullets with jackets made the old way from copper rod would curl back to the partition during expansion while retaining a large frontal area. But due to excessive hardness of some lots of jackets made from tubing, the front section would occasionally shear off at the partition during expansion, resulting in a small frontal diameter. There had to be a better way.
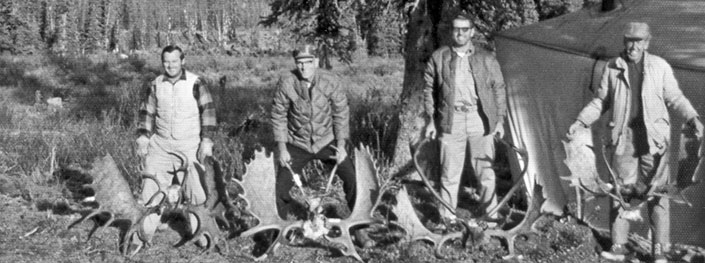
In 1974, the impact-extrusion method of jacket forming was adopted. In a nutshell, gilding metal wire is fed into machines that chop it to the required length and then form the cylindrical slug into specified dimensions. After the slug is annealed to the desired hardness, it is fed into a series of dies that exert tremendous pressure in forming the front and rear cavities while leaving a solid partition between them. The new process eliminates the hole in the center of the partition. After a second annealing, the jacket is trimmed at both ends and redrawn close to its final diameter. The rear core is crimped in place and, after insertion of the front core, the bullet is swaged to its final form and diameter (there are more than 20 steps in the process of going from gilding metal wire to finished bullet). The more easily compressed jacket allowed elimination of the relief groove. Polishing, washing, inspecting and packaging are the final steps.
When word got out that the old Partition was being phased out, a buying frenzy spread rapidly throughout the hunting world. After all, some suggested, there was no way the new bullet could be as good as the old one. Adding to the panic was Nosler’s decision to delay production of the larger calibers; it was not long before some hunters who had rifles in .375 H&H Mag. were willing to pay $5 each for 300-gr. Partitions. There were minor production issues early on, but once they were history the new bullet proved to be a big improvement over the old bullet, and it mostly had to do with differences in the grain structures of the two jacket materials being used. In addition to being harder, the grain of the old material ran at right angles to the axis of the bullet, and that encouraged the wall of the front cavity to shear off when expansion reached the partition. When that happened, none of the front lead core was retained. In addition to being softer and more ductile, the grain structure of the new material ran parallel to the axis of the bullet, and that enabled it to curl back against the partition without shearing off. The result was a larger frontal diameter along with higher retained weight due to partial retention of the front core.
During the years following 1974, a number of tweaks and improvements were made in both the design and the manufacturing process—one of the more important was that the jacket had to be made thicker back near the partition on bullets of larger calibers. Weight retention of Partition bullets in smaller calibers will usually range in the neighborhood of 60 percent at close-distance impact velocities to about 80 percent out at 500 yds. The large-caliber Partitions I have the most experience with are 225 gr. and 250 gr. in the .358 STA, 210 gr. and 250 gr. in the .338 Win. Mag., 300 gr. in the .375 H&H Mag. and .375 Ruger and 400 gr. in the .416 Rigby and .416 Rem. Mag. Even at close-range impact velocities, the bullets I have recovered managed to retain 85 percent or more of their original weight. This is important to note since those bullets are often used on large and potentially dangerous game where plenty of penetration is needed.
While John Nosler designed his bullet for optimum performance on game of various sizes rather than precision target shooting, the Partition can be surprisingly accurate. It rarely carves out groups as small as those made by match-grade bullets, but when fired from accurate rifles, it seldom fails to shoot inside minute-of-angle, and that includes those in .338, .358, .375 and .416 calibers. Several years after the current version was introduced, I shot the .270 Win. loaded with 130- and 150-gr. Partitions in my return-to-battery rest. That cartridge was chosen because it was developed specifically for big-game hunting and has never been considered an accuracy cartridge. Maximum charges of H4831 pushed those bullets to 3133 and 2994 f.p.s., respectively, from the 24" barrel. Averages for five, five-shot groups at 100 yds. were 0.419" for the 130-gr. bullet and 0.468" for the 150-gr. bullet. The smallest group fired with the 130-gr. bullet measured just 0.334".
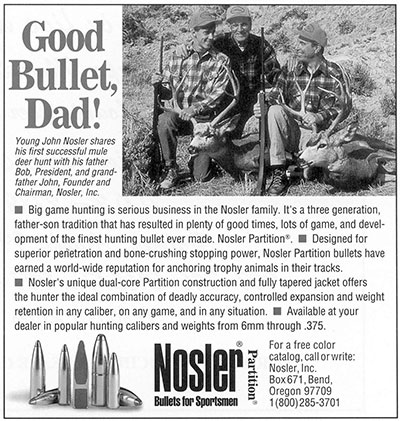
Through the years, John Nosler hunted with rifles in .30-30 Win., .30-40 Krag, .30-’06 Sprg., .300 Win. Mag., .270 Win., .243 Win., .348 Win. and a 7 mm Mag. of his own design, but a Pre-’64 Model 70 in .300 H&H Mag. used to take more than 30 moose, and an assortment of other game, remained his favorite. John retired in 1988 and, while his son Bob purchased Nosler, Inc., during that year, he remained quite active in the company until shortly before his death in 2010. John Nosler was the unanimous choice for the first NRA Golden Bullseye Pioneer Award in 2007. In March 2018, Bob’s son John was promoted to president and chief operating officer, while Bob became chairman of the board and chief executive officer.
The Nosler Partition is now offered in 14 calibers and 35 different weights, ranging from 0.224"/60 grs. to 0.458"/500 grs. Unlike in the old days, there is plenty of competition, not only from Nosler’s AccuBond and E-Tip, but from the Swift A-Frame, as well as expanding bullets of monolithic construction from Barnes, Hornady and others. Even so, no small number of hunters around the world still consider John Nosler’s Partition to be the big-game bullet by which all others are measured.
Final Notes: I began using Nosler Partition bullets in 1965, and during the past 50-plus hunting seasons have used them to take various game ranging in size from southern whitetails to brown bear in Alaska to Cape buffalo in several African countries. I never had the opportunity to sit around a campfire with John Nosler, but I have shared several hunts with his son Bob. Great hunts are not always all about hunting, so among many interesting things I learned from Bob was quite a bit of company history. Much of the knowledge gained during those memorable days afield was recalled while writing this article. But there were still a few gaps remaining and they were filled when Bob sent a copy of Gary Lewis’ excellent book, Going Ballistic, The Life and Adventures of John Nosler. A web search will turn up plenty of copies.