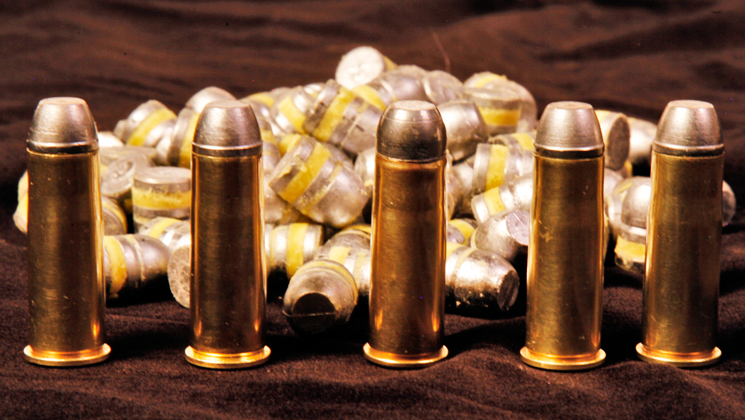
The use of gunpowder—black powder—as a propellant for projectiles was first seen in the 10th century. Initially, projectiles were rocks, arrows and anything else that could fit down the bore. Accuracy, of course, was nil, and if hit by one of these ersatz projectiles, the poor victim was more likely to die from infection rather than the stopping power of these objects.
Lead has been known to man for more than 3,000 years. Man began using it for jewelry by smelting it from ores like galena. By the 14th century, lead was becoming a common metal with which to cast bullets. The muskets and blunderbusses of the day would be loaded with a lead ball—or sometimes the scraps of sprues and such in a blunderbuss—and deliver some awesome wounds, if not always with accuracy. When rifling was introduced—at the end of the 15th century—accuracy improved, as well as deadliness of the arm. Jacketed bullets are a relatively new idea; the first successful metal-jacketed bullet appearing in Switzerland in 1882. And although the jacketed bullet has taken over much of the shooting world, the fact remains they are only needed in arms firing bullets at 3,000 f.p.s. or greater, or for very long and heavy bullets at 2,500 f.p.s. Some pistols—notably the Glock—are supposedly not to be fired with cast bullets, but most can safely and economically shoot with cast bullets.
If one looks at the molds available for cast bullets, it’s easy to be confused as to which one will best suit his needs. Overall shape, point profile, lubrication grooves, crimping grooves and gas-check heels run the gamut. If simple target shooting is your objective, almost any bullet will do. Revolver shooters often prefer wadcutter profiles—essentially a barrel-diameter slug with flat ends—that will cut a clean hole in target paper for easier scoring. Some wadcutters can have a hollow base to allow the rear of the bullet to obturate and more effectively seal the bore. When I started reloading, a lot of guys tried loading them backward—hollow point to the front—in order to (hopefully) get better stopping power in a short-barreled revolver. I tried it for a while; didn’t have to shoot anybody with it and moved on to more effective bullets.
A. Basic SWC design consists of a roughly conical nose, truncated with a flat point (called a meplat).
B. A concave sided SWC, typical of a lightweight .45 ACP bullet used in bullseye shooting.
C. The Elmer Keith design uses a wider front, and convex sides on the "cone" in front.
D. The Keith style SWC taken even further, nearly wadcutters in shape but are intended for large-game hunting with handguns.
Wikipedia images
For most revolver shooting, the Keith-Croft-designed semi-wadcutter has proven to be the most effective. Now normally referred to as the Keith semi-wadcutter (above right), it was Elmer Keith’s penchant for driving heavy-for-caliber handgun bullets at as high a velocity as could be obtained without blowing up the gun (most of the time; there were exceptions), in order to humanely take game animals or, if needed, stop some ne’r-do-well. Semi-wadcutters have a relatively long shank terminating with a sharp shoulder with a slightly smaller-caliber nose to provide some aerodynamic performance and stability. For the best performance in live tissue, it is very important that the nose, as well as the shoulder, be very flat with a sharp edge at the profile in order to transmit the most energy into the target. Flat meplats—the leading profile of the bullet—transfer energy from the bullet to flesh more effectively than a round or pointed meplat, which has a tendency to push flesh aside as it passes through the body.
Some have added hollowpoints—a hollow cavity in the meplat—with the objective of increasing the terminal forces of the bullet on target. The trouble is with handgun velocities topping out at roughly 1,500 f.p.s., the deformation of the nose of the bullet into a profile for energy transfer is problematic. It may or may not work out well. Some years ago, there was some hoopla over casting the shank portion of the semi-wadcutter from a hard alloy like linotype and a separate hollowpoint from a softer alloy, then gluing the two together. It never caught on that much because, one, it was a tedious, time-consuming chore and, two, it was difficult to get the exact amount of glue each time, thus rendering your bullets having different weights and destroying accuracy.
Bullets intended for use in repeaters other than revolvers usually have a rounded profile on their noses to facilitate better feeding from magazine to chamber. If they are designed for the tubular magazine of a lever-action rifle, there is usually a small flat meplat to prevent a cartridge from setting the one forward of it off during recoil.
As long as velocities stay below about 950 f.p.s., low-hardness alloys work fine. As the velocity increases beyond 1,000 f.p.s., however, the combination of a soft alloy, intense heat and pressure from heavier powder loads and friction within the barrel will cause portions of the cast bullet to tear off and deposit within the barrel. We call this leading, and it destroys accuracy. To eliminate leading, bullets must be cast from a harder alloy, and the bullet lube must become more resistant to heat, as well as provide more lubricity.
Early on during the pioneer movement in the U.S., frontiersmen learned that a little tin added to the alloy would make it fill out a mold more consistently. Later on, a healthy dose of antimony hardens the alloy, thus increasing the velocity tolerance the barrel would have. Lyman, a company synonymous with bullet casting, developed what is known as the Lyman No. 2 alloy, consisting of 90 percent lead, 5 percent tin and 5 percent antimony. This alloy is relatively easy to mix and works well on bullets pushed to about 1,200 f.p.s. I use this alloy in all of my black powder cartridge loads with bullets from 212 grs. for the .44-40 WCF up to the thumb-size 530-grainers in my .45-90 Sharps replica. As long as I properly lubricate—which I’ll cover soon—I never have a problem with leading, and powder fouling remains soft and easy to remove, too. For my magnum revolver and center-fire rifle loads, I up the antimony content to as much as 14 percent, and the result is a hard bullet that never deforms much. On game, these tough bullets cut their way through flesh and bone, and when properly placed have never failed me.
While jacketed bullets rely on a copper-based alloy to provide lubricity and heat resistance, cast lead bullets require a separate lubricant. Most of these lubricants are wax based, though the leather-shirted pioneer types often use animal tallow. You can purchase sticks or tubes of commercially made lubes, but a lot of casters—me included—choose to make our own. Bullet lubricant recipes run from the mundane to the exotic, and each has a cadre of devoted followers, boldly touting their favorite as the end-all of lubricants.
With no intentions of stepping on anyone’s personal favorite, here is a recipe that a cowboy action friend of mine—now, sadly, deceased—gave me. It works so well for me that I use it exclusively for black powder as well as heavy smokeless loads. I vary its consistency by the ration of peanut oil to beeswax. In a double boiler—not one from your kitchen, once you make bullet lube in it you will not want to use it for food—melt about 2 lbs. of beeswax. Once the wax is liquid, add a cup or so of peanut oil and mix thoroughly. As you are mixing this, add a tablespoon of STP Oil Treatment (the old style). Pour the mixture into your lubrisizer cavity or molds you have made for it and cool. If the cooled lubricant is too soft, re-melt it and add a little more beeswax. If it is too stiff and flakes as you try to lube your bullets, re-melt it and add a little peanut oil.
I’ve been using this recipe for more than 10 years now. In a softer configuration, it handles all my black powder cartridges beautifully, making clean up even easier than smokeless. By adding roughly two to three ounces of beeswax, I can drive heavy semi-wadcutters in my .357 and .44 Magnum revolvers to the max without any concern for leading. I also use it in a cast bullet load for my old Model 94 Winchester, driving a 165-gr. RCBS flat point to about 1,550 f.p.s. that is accurate and devastating on rabbits.
Cast bullets may seem to be old fashioned; some even snort that they are out of date. Nothing could be further than the truth. Cast bullets are perfectly fine for as much as 90 percent of your shooting needs, and they extend the amount of shooting you can do by making your projectiles much less expensive.