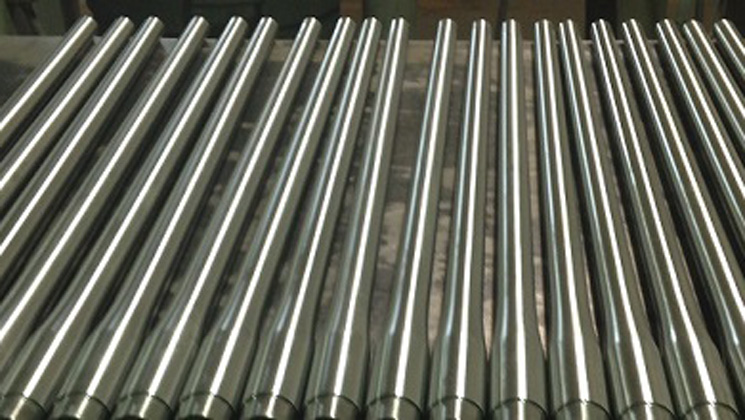
Image courtesy K&P Gun Co.
In a previous article I explained the basics of rifling and its purpose and influence on firearms. However, there is much more to a barrel than simply imparting a gyroscopic spin to the projectile. Barrel construction and profile are purpose built and have a major influence on how well the rifle performs what is asked of it.
Image copyright NRA Firearms Sourcebook
The barrel is fundamental to a firearm. It provides a launching point to the projectile, as well as a means of transferring the energy from the propellant into velocity of the projectile. Oddly, the Chinese, who invented black powder, used bamboo for some of the earliest barrels. As muskets were developed, their barrels were relatively long and rather thin walled. Pressures from black powder loaded from the muzzle are relatively low, compared to today’s smokeless powders. A longer barrel provided for a longer acceleration of the projectile, thus increasing its velocity. The thin profile made the early muskets more portable to the soldier. After rifling was introduced—circa 1498—the cross section became a little more stout because it was shown that a heavier barrel would “hang” better while shooting offhand, and larger amounts of black powder were being used to take advantage of the increased accuracy a rifled barrel provides over a longer distance.
Once repeaters became the norm, barrel profiles generally settled down a bit. Most were round, of medium weight and usually shorter than the ones found on single-shot muzzleloaders. Somewhere during all of this, it was discovered that barrels vibrate like a guitar string during firing; the notion came about that the less vibration, the more accurate the barrel. Octagon barrels were thought to be a bit stiffer, though subsequent tests show this is not necessarily the case. Nonetheless, octagon barrels were popular during much of the 19th century and into the 20th century.
As bolt-action rifles gained acceptance, it was found that better accuracy could be obtained by properly bedding the barrel in the stock. The trick was to bed the barrel with the right amount of upward pressure from the stock to dampen the vibrations. While the concept of a properly constructed barrel was rather well known, early 20th century manufacturing techniques lagged a bit as did the consistency of steel alloys used in barrel making.
Wikipedia image
When drilling raw barrel stock, the gun drill—a V-shaped drill with a hollow center like a hypodermic needle that carries cutting oil to the front of the drill where it is cutting—rarely came out at the dead center from which it was started. There were a variety of reasons for this. Inconsistencies in the alloy created hard and soft spots which might steer the drill off course. As often as not however, it would be a drill operator who got impatient and put too much or inconsistent pressure on the drill to veer it off course. The most often remedy was to chuck the drilled barrel blank on centers of each hole and turn down the blank to profile specs. This, however, created another problem of stresses within the barrel, causing it to bend ever so slightly away from the stress point.
Too, barrels that were off center more than a quarter inch were actually curved tubes. Any gun shop or barrel making facility worth its salt had an overhead press adjusted to eye level of the operator. He would take the barrel and install it in a pair of V-blocks set perhaps 4" to 6" apart. Disks with small apertures would be set in each end of the barrel. The operator would sight through the disks and observe a shadow line in the barrel. Wherever that line had a jog in it, the barrel had a bit of a wow in it. The operator would then set the break opposite a point in the straightening press and give it a bump with an overhead handwheel. This was a time-consuming task requiring a fair amount of skill. One afternoon some 35 or so years ago when I worked at Freedom Arms, Dick Casull showed me how this was done. The barrel press was ancient and the only one I have seen in a shop. It took about a half hour to straighten the barrel we were working on.
Modern metallurgy and manufacturing techniques have made the barrel straightening press as appropriate as a buggy whip. Computer-operated machines control everything from alloy composition and purity rough cuts with .0005" of final dimension. Tolerances are so small now that decent barrels can be knocked out nearly as fast as soda bottles.
There are those shooters who demand the absolute most from their barrels. Precision, target and varmint shooters want to be able to precisely place a bullet close enough to their point of aim that the difference must be measured in thousandths of an inch. Ken Johnson, owner of K&P Gun Co., in Rapid City, S.D., has been making custom barrels for nearly 30 years. He admits that many of today’s mass produced barrels are generally of great quality and are quite accurate, but a few stinkers can and do sneak through. “Few mass produced barrels are stress relieved. Even though our steels are superior to what was once normal,” he told me, “We still double stress relieve our barrels so that none of them need straightening.” With his tooling, Ken says that he almost never sees a gun drill exit a blank more than .010" to .015" off center. Custom barrel makers then ream the rough bore very close to final dimension, and many actually hone the interior to final dimension, providing the smoothest and most consistent surface to support the bullet as it accelerates down the bore. Most custom barrel makers cut the rifling into their barrels, as opposed to button rifling which more or less cold forges the rifling. Cut rifling is more precise and makes a difference for those whose groups are a single hole in the target and group size is measured in thousandths of an inch out of round.
Because of the repeatability and consistency of modern barrels, the old practice of bedding the barrel in the stock to dampen vibration is no longer used. Today’s barrels are free-floated, meaning that nothing touches the barrel except where it is retained in the receiver. The theory is a barrel is going to vibrate during firing anyway; if it is consistent throughout, then it will vibrate the same from shot to shot. And in practice this seems to be true.
Barrel weight—meaning how much a barrel weighs by varying its diameter—used to be pretty cut and dry. For the hunter or soldier afoot, he wants the lightest firearm he can get since he does a lot more walking than shooting. Climbing a 12,000 ft. sheep mountain with a 7½ lb. rifle is far less taxing than climbing that same mountain with a 12 lb. target rifle. The target or varmint shooter doesn’t have to pack his rifle but a few yards and usually with no difference in elevation. He can enjoy the benefits of a heavier rifle—steadier on target, less felt recoil, less physical punishment during long strings of shots and less mirage because a heavier barrel heats up more slowly than a lightweight one.
Another aspect of barrels is length. Shorter barrels are handier and less of a burden to pack around in the field. But longer barrels yield higher bullet velocities, which, in turn, provide flatter trajectories, making it easier to hit targets at long range. When I started hunting some 40-plus years ago, barrels for standard cartridges like the .30-'06, .270 Win. or .308 Win. were usually 22". Magnums were usually 24" to 26". Today, with the popularity of long-range precision shooting on the rise, it’s not uncommon to see rifles with 28" to as much as 34" barrels—about as long as the old single-shot black powder rifles of the 19th century.
Many shooters and some barrel makers say that the muzzle crown is the most important part of the barrel because it is the last thing to touch the bullet before it leaves the rifle. Crowning can be recessed or hemispherical. Rifles from the 19th and 20th centuries often had a hemispherical crown, whereby the muzzle has a rounded profile and the last of the rifling is slightly recessed. Today, most rifles have a recessed crown. The muzzle is squared in a lathe, and then a center portion of the muzzle is recessed about .050" to .100". The primary reason for recessed crowns is that it is less expensive to do, while providing a truly square muzzle.
Today’s firearms market is trending toward modular guns. Entire cottage industries are popping up to cater to specific models—witness the AR-15 and Ruger 10/22, to name two classic examples. Barrels are also becoming part of the modular gun market. A good friend of mine has three different barrels in three lengths for one of his rifles. Each has a purpose, and he can switch one to another in a handful of minutes in the field. For me it’s a lot of extra weight to pack and trouble to switch, but my buddy loves being able to cater his rifle precisely to the task at hand. He’s probably right; the trend does appear headed that way. Knowing how barrel technology is headed and understanding the advantages it offers will help you make a better choice.