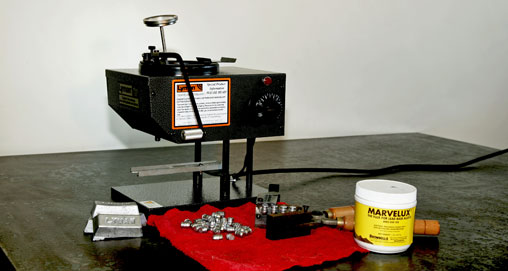
We all want to shoot more, but the cost of ammunition is as much a limiting factor, as is finding the extra time to shoot. With the cost of factory ammo averaging nearly a buck a shot, it doesn’t take long to drain the bank account of an active shooter. Many take up handloading as a cost-cutting tool. Still, the cost of jacketed bullets is often 50 cents or more each.
Truth is that for most of our shooting practice, cast bullets are perfectly satisfactory and a whole lot cheaper. Commercial cast bullets are pretty cost effective, but if you really want cheap bullets you cast your own. In this first of three articles on casting bullets we’ll look at accumulating a stash of suitable bullet-casting alloy. Then we’ll go through the casting process and finish up with sizing, hardening and loading.
Pure lead
Elemental or pure lead is difficult to find for those of us who scrounge our bullet metal. With a Brinell hardness (Bhn) of just 5, its only use as a bullet-making material is for round balls in traditional muzzleloaders or cap-and-ball revolvers. In those relatively low-pressure, low-velocity arms, the malleability of pure lead is needed for the bullets to upset and help seal the bore during the shot. Velocities are usually low enough to keep the bullets from leading the barrel (scraping lead off the bullet and leaving it in the barrel).
Short of buying pure lead from a foundry, the only way I know of garnering a supply is to melt alloy lead and scrape the alloying metals off without fluxing. Even then, there will be trace amounts of alloying metals, but for those really on the cheap it is an alternative.
Even if you don’t load muzzleloaders and cap-and-ball revolvers, a supply of pure-lead round balls in a variety of sizes is handy for slugging the bore. Hornady and Speer make pure-lead round balls in several calibers, so a box in each caliber category you load shouldn’t break the bank.
Lead alloys
There are several lead alloys used in bullet casting. They utilize varying amounts of tin and antimony, as well as trace amounts of other metals, in order to harden the bullet and to make it cast better. High ratios of antimony will harden lead considerably, but at the expense of brittleness. When bullets are cast from alloys containing 15 percent or more antimony they can actually split or shatter if dropped on the floor. Tin helps attenuate the undesirable characteristics of antimony. Trace amounts of manganese can help the alloy fill out the mould better, but most casters do not add it.
Lead-acid batteries, like those used in automobiles, often have arsenic in the plate alloy, as well as calcium. When arsenic and calcium come into contact with the hydrogen generated in the normal chemical reaction in the battery they form the ammonia analogues arsine and stibine. These are heavy gases, once used in chemical warfare nearly a century ago. Very small amounts of either of these gases can kill you, so the recycling of car batteries for bullets isn’t worth the risk.
One of the most popular and oldest alloys is Lyman No. 2. Made from 90-percent lead, five-percent tin and five-percent antimony, Lyman No. 2 comes out to a Bhn of 15. Lyman No. 2 alloy is great for most non-magnum handguns and rifle loads with a velocity of less than 2,000 fps.
Hardball is a modern version of Lyman No. 2 alloy with a Bhn of about 16. Its alloy is 92-percent lead, two-percent tin and six-percent antimony. Because of the lower ratio of tin Hardball alloy is slightly less expensive than the original Lyman No. 2. These alloys can be used interchangeably.
Magnum handguns and rifle loads with velocities greater than 2,000 fps, but less than 3,000 fps, benefit from a linotype alloy. Once available from newspapers, which used the alloy for the printing plates of their offset printing presses as early as 1886, linotype is made from 84-prercent lead, four-percent tin and 12-percent antimony and has a Bhn of approximately 22. The 46-percent increase in hardness combined with a proper lube and bullet design reduces leading in the bore significantly and promotes accuracy at the higher velocities. Sadly, linotype is no longer used in the offset printing process, so your options are to purchase it or make it from scratch.
Wheel weights have long been a popular source of bullet-making material. Three decades ago wheel weights contained as much as nine-percent antimony making them a good choice for a base metal for those wanting harder bullets for magnum revolvers and some rifles. Modern wheel weights have approximately 3-percent antimony—still useable but not nearly as hard or tough as it once was. Some modern wheel weights have been made from zinc. Typically, lead-based wheel weights melt at 600 degrees; zinc melts at 787 degrees. Zinc causes multiple problems when melted with lead, so if you melt some wheel weights and find chunks of metal floating on your melt, scrape the zinc off and discard it.
Cast bullet aficionados have other esoteric alloys that they espouse as perfect for one application or another, but these are the most popular. For those who want to delve deeply into it, the Cast Boolits website can lead you down that Yellow Brick Road.
Assimilating your alloy
If, like me, you scrounge your lead, you’ll need to melt it down into a homogenous alloy and pour it into 1-pound ingots to be melted later when you actually cast your bullets. There are a few things to keep in mind when melting lead.
First, go through your pile of material and make sure that there are no live rounds or spent brass in it. Hand remove anything that doesn’t look like lead. Also, ensure that the donor bucket or pile is absolutely dry. Any moisture or combustible materials in that pile will have a profoundly negative influence on your project and possibly your life.
Whereever you melt lead—either for assimilating an alloy supply or casting bullets—it must be well-ventilated. Vapors will come off the pot, and breathing them will have adverse health effects. At a bare minimum, if you choose to melt lead indoors—like your shop or garage—you should set up a fan pointed toward an open window or door.
Depending on the amount of lead you are melting you may use your casting furnace, or you may choose a larger outdoor stove. Several of my shooting buddies and I get together once or twice a year to work up a supply. One guy has a couple of dilapidated Dutch ovens which we put on top of a heavy-duty propane outdoor stove. A half dozen 1-pound ingot moulds are kept pretty busy as we put up 200 to 500 pounds of alloy.
Once the pot is fully melted, flux the melt with beeswax or Marvelux (available from Brownells). This ensures that the tin and antimony remains in the melt. Scrape off the dross (the debris that floats on top), pour the alloy into the ingot mould and place it on a mineral-type surface. Once it cools, dump the ingots on a heat resistant surface.
Now you have a supply of alloy for casting. In the next installment we’ll get into the actual bullet-casting process.