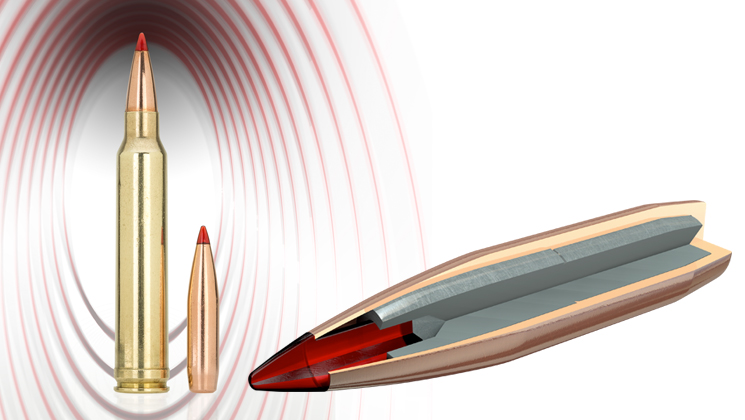
Hornady’s ELD-X bullet features a long, javelin-like body, a boattail base and the new Heat Shield Tip to improve long-range performance. Thanks to its tip, a sophisticated jacket and Hornady’s Interlock design,the ELD-X is a reliably expanding projectile intended for all-range hunting.
This really goes all the way back to bathtub caulk in a hollow point,” said Neil Davies, Hornady’s chief of marketing, referring to the early days of the company’s tipped-bullet research. Though true, the Grand Island, Neb., ammunition maker has evolved tip technology far beyond its jerry-rigged beginnings, and offers a full suite of tipped bullets—including the FTX, GMX and V-Max, to name a few—for rifles and handguns, with intended uses ranging from hunting to personal defense. The newest addition, the Extreme Low Drag-eXpanding (ELD-X) incorporates all the lessons learned from its predecessors and leverages technology rarely before used in commercial ballistic pursuits. The result is match-grade accuracy, high retained velocity and energy, and impressive terminal ballistics from less than 100 yards to beyond 800 yards. Is the ELD-X the perfect bullet? The market will answer that question soon enough, but after seeing how it was developed, and using it extensively in the field, I remain in awe of what Hornady has accomplished, and what the bullet will mean for shooters, hunters and the future of ammunition development.
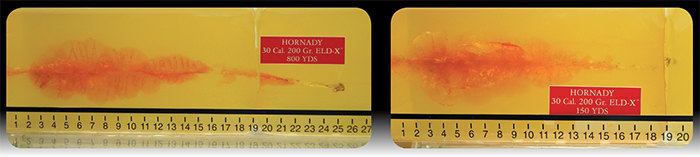
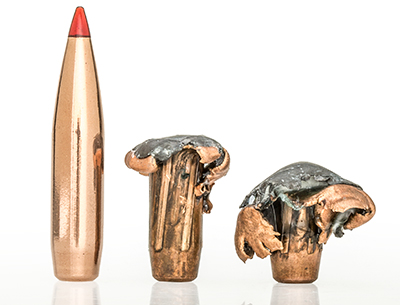
The Mission
Recent years have seen a growth in interest in long-range shooting. There has always been a market for guns and ammunition capable of consistent 1,000-yd. hits, but the niche was relatively small. Over time, though, consumer demand has grown; exploits of military snipers, high-profile—if controversial—feats of “long-range” hunting, the rise of all things tactical, and the availability of high-performance firearms and optics at increasingly affordable price points have all contributed to the rapidly expanding pool of extended-range shooters.
Hornady found itself a bit late to this particular party, but in 2012 made the decision to enter the emerging market in a fairly unique way. The company had already built a host of products renowned for their accuracy and lethality at conventional hunting distances (0-400 yds.). Likewise, it was well-equipped to develop a match-accurate, reliably expanding hunting bullet for use at extended ranges. But the challenge set before Hornady’s engineers was to develop a projectile that would embody the company’s keystones—”Accurate, Deadly, Dependable”—at any distance.
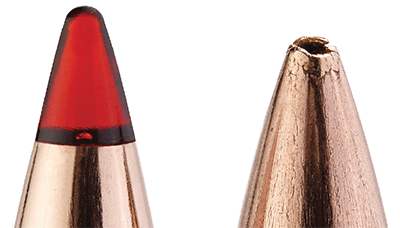
If you’re not a Ph.D.-level ballistician, literally a rocket scientist, you may not fully appreciate how difficult it is to develop an all-range hunting bullet. But in layman’s terms, the first challenge Hornady faced was designing a bullet that would be accurate throughout its entire range of travel. In that department the company has an excellent track record. One contributing factor to a bullet’s aerodynamic quality is its meplat—the very front tip. Hornady had, in its words, “perfected the meplat” in 1996 with its polymer-tipped A-MAX bullets. It is far easier to mold polymer tips to a consistent shape and diameter than to draw and form metal to the same. So the new bullet would be tipped, and the question of accuracy would largely be solved.
Deadly and dependable can, to an extent, be addressed together, though the latter can have a dual meaning. Dependability, especially in terms of a product’s quality control, is achieved through proven manufacturing techniques that ensure consistency from bullet to bullet and lot to lot. But the hunter locked onto his quarry wants to know that if he has done his best to break a clean, accurate shot, the bullet will deliver rapid and lethal effects. For him, deadly and dependable are one and the same. To achieve lethal results, the terminal performance of an ideal hunting bullet will produce a large, long, temporary wound cavity and also exhibit excellent penetration. As noted earlier, Hornady already knew how to do this. A polymer tip not only enhances ballistic performance, but because it is seated in a bullet’s nose cavity and forced back upon impact, it also serves as a mechanical initiator for expansion. Of course the other half of the expansion equation involves the bullet’s jacket. When properly designed, the front portion of the jacket will split into petals and form the desired mushroom shape during expansion. It also protects and retains the bullet’s lead core—preserving the slug’s weight is key to achieving adequate penetration.
So there are a lot of elements in play when designing a hunting bullet: accuracy/aerodynamics, a mechanism for expansion and sufficient retained weight to ensure deep penetration. The recipe is well-known, and many companies offer excellent products that exhibit these traits. But there is yet another variable that, to a large degree, dictates a bullet’s terminal performance: Velocity. How fast a bullet is moving is a key factor in any energy equation, and its fluctuation is why the all-range bullet concept poses difficulty. At close range, velocity is very high; but the farther a bullet travels, the slower it becomes, and its terminal effects will differ greatly depending on its speed at impact.
Hornady is calling its solution “continuous expansion.” This is an over-simplification but, suffice it to say, the company designed a bullet that would reliably expand upon impact and continue to mushroom until exiting the target or coming to rest. At closer range/higher velocity, the bullet’s jacket will allow it to shed some material as it expands down its length, while still keeping its mushroom shape and retaining 50 to 60 percent of its weight. The high velocity will drive even a lightened slug to adequate depths in most game animals—a 200-gr. .30-cal. example penetrated nearly 20" into ballistic gelatin at 150 yards. At longer range/lower velocity, the slower bullet will still bloom upon impact, but the continuous expansion will be arrested sooner. In this case, the lower velocity is aided by the higher retained weight, 80 to 90 percent, to still produce excellent penetration—more than 24" in ballistic gel with the same bullet at 800 yards. Overall, it’s an elegant solution to a complex problem.
A Better Way
There are many criteria by which consumers compare bullets, but given a particular bullet type and weight—often dictated by the intended pursuit—an oft-advertised feature is the bullet’s ballistic coefficient (BC). A simplified approximation of a projectile’s drag—how well it slips through the air or, conversely, is impeded by air resistance—BCs are used for making simple trajectory calculations. Ballistic coefficients compare the rate of velocity loss of a given bullet against a standard projectile. Most often used are the G1 and G7 standard projectiles, G1 referring to a flat-base, tangent-ogive projectile, while G7 is an ideal, low-drag bullet featuring a boattail and secant ogive. Because the tested bullet’s data is compared against (and therefore divided by) the standard projectile’s values, BCs are often less than 1.00, but the closer they come to 1.00, the better that bullet retains velocity. More retained velocity equals more energy at impact, an important consideration for extended-range shooting.
In 2014, Hornady was ready to come to market with its tipped, all-range hunting bullet. New ammunition in hand, the engineers headed to the range in order to wring out the bullet and determine its relevant data, including ballistic coefficients, for catalogs, reloading manuals and advertisements. But this time, beyond testing a new bullet, the Hornady guys were trying out new testing equipment as well—Doppler radar.
In the past, companies have used a series of chronographs or acoustic detectors (microphones) in order to determine down-range velocities and extrapolate BCs. Though this method had been the “best” way to express a bullet’s aerodynamic performance, it is far from a perfect system. Such a setup provides only a handful of data points, literally those few instances where the bullet physically passes the various pieces of testing apparatus. Those data points are then compared against the known standards to produce a “close enough” match. Based on the match, all information regarding the flight of a projectile between and after those few data points was assumed.
In reality, though, most bullets do not match very closely to the G1 or G7 standard projectiles. And the more a bullet differs in shape from the standard, the more it will differ in drag characteristics. This is particularly important to those long-range shooters who rely most on BCs: longer shots (distance) yield greater velocity loss during flight and, ultimately, greater divergence from trajectory models based on G1 or G7 standards.
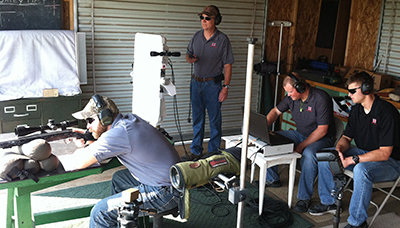
Doppler offers a better way to calculate trajectories. Using high-frequency microwaves to measure the Doppler shift in frequency reflected from a moving object, Doppler can track a bullet throughout its entire flight and, at any point, provide precise measurements for velocity, time of flight and distance traveled. The radar provides hundreds of thousands of data points for each bullet tracked. The technology allowed Hornady to replace extrapolated data with precise, high-resolution information. Trajectory curves that were once assumed became real and concrete—and, more importantly, different than anyone expected.
The Breakthrough
One of the visual representations developed by the Doppler radar and its associated software depicts a bullet’s drag coefficient (Cd)—essentially the amount of drag imparted on a moving object strictly due to its shape. The chart tracks the bullet’s velocity (X axis), expressed as Mach numbers (Mach 1 at sea level equals 1116 f.p.s.) and compares it to the projectile’s drag coefficient (Y axis). Because a projectile’s velocity decreases the longer and farther it travels, the graph is actually read from right to left.
A bullet is at its fastest and most stable as it leaves the muzzle of a firearm, and both values will deteriorate throughout the course of flight until speed and spin can no longer keep the projectile airborne. How fast the degradation occurs is largely dependent on the bullet’s shape and how well it slips through the air—again, this value is expressed as the Cd. As the bullet slows (Mach number decreases) and destabilizes, drag increases. Eventually, drag will overcome forward momentum and the bullet will drop, a crash depicted clearly on the Cd vs. Mach Number charts. Given this information, all bullets should share similar-looking curves on the Cd vs. Mach Number graph: a concave curve that gradually rises (drag increases) from right to left (velocity decreases) and culminating in a steep drop.
It was strange then, when at the range, the Hornady engineers observed a convex hump form when charting the new bullet’s drag. The hump was relatively small and usually occurred within the first 100 to 200 yards of flight, and following the hump the drag curve returned to its expected concave climb and drop. The irregularity may have been small and short-lived, but the shift from concave to convex, and back again, seen on the Cd vs. Mach Number graphs could only have one explanation: The bullet itself was changing shape in flight.
It did not take long for the Hornady team to realize it was not the whole bullet changing shape, only the non-metal component—the polymer tip. But how was this possible? And how widespread was the issue? The answer to the first has been illustrated in popular movies such as “Apollo 13.” Remember when the capsule re-enters the atmosphere, surrounded by fire, with Houston waiting to see if the damaged heat shield would hold? Bullets undergo the same heating effect, with the highest temperatures registering right on the tip, the point of the bullet’s structure tasked with diverting air around the projectile as it travels at high speed. Hornady found that the temperature at the tip was actually exceeding the polymer’s glass transition point—where material changes from rigid to rubbery—and possibly its melting point. Investigating further, the engineers found that the problem affected their competitors’ tipped bullets as well. Bottom line, in Hornady’s estimation, the current generation of polymer tips wasn’t standing up to the heat. The aerodynamic benefits derived from using molded-polymer tips, with their perfect meplats, were not being realized due to melting and deformation.
A New Product, A New Standard
Once the failure of polymer tips was discovered, things started falling into place for Hornady’s all-range hunting bullet. New polymers were tried and tested, and one was found that met the company’s criteria. With the new material, the Heat Shield Tip was born. Molded as precisely and consistently as previous polymer tips, the Heat Shield Tip boasts glass transition and melting points hundreds of degrees greater than the previous generation’s—475° F and more than 700° F, respectively. As well, the Heat Shield Tip is physically larger than its predecessors, a trait that facilitates bullet expansion at low velocity—a boon to an all-range, expanding projectile.
The hits kept coming as testing revealed improved accuracy, retained velocity and higher BCs when using the Heat Shield Tip. Data for one example pit the 6.5 mm A-MAX bullet, with its standard polymer tip, against an identical bullet topped with the Heat Shield Tip. Both projectiles weighed 140 grs., achieved a muzzle velocity of 2800 f.p.s. and were fired from the same barrel under the same conditions. At range, the A-MAX exhibited drops of 3.2" at 200 yds., 26.9" at 400 yds. and 164.6" at 800 yds., and still held a velocity of 1759.7 f.p.s. at 800 yds. For the bullet with the Heat Shield Tip, drops were reported as 3.2", 26.2" and 157.6", respectively, and velocity was 1856.1 f.p.s. at 800 yds. Though both bullets performed similarly within conventional range, at 800 yds. the Heat Shield tipped bullet dropped 7" less (0.84 m.o.a.) and retained nearly 100 f.p.s. more velocity compared to the conventional tip, and was also more resistant to wind drift. When the numbers were crunched, the traditional A-MAX yielded an excellent G7 BC of 0.275, but was outpaced by the Heat Shield Tip at 0.307.
The Heat Shield Tip was married to the continuously expanding bullet design to create essentially an über bullet, one that, true to the mission, was match-accurate and would be a reliable, ethical hunting projectile, even well beyond conventional range. Testing and improvements continued, though, and included a writers’ hunt for plains game in South Africa. There, I and several other hunters took nearly 40 animals, from Vaal Rhebuck to bull Eland, with the new bullet loaded into custom .300 Win. Mag. cartridges. For reference, I used a prototype Ruger American Magnum rifle topped with a Burris Eliminator III LaserScope and took animals at ranges from 100 yds. to 570 yds., all with single shots. Other hunters took game beyond 600 yds., with one beyond 800 yds., also one-shot harvests. I was astounded time and again by the bullet’s accuracy and absolutely devastating terminal effects. As a testament to the latter, every animal shot was recovered, and only one ran beyond its hunter’s eyesight, though it only managed 100 yds. before expiring.
Data and recovered bullets from my hunt, and others like it, initiated still more refinements. When I made a trip out to Grand Island, Neb., in September 2015, five months after Africa, Hornady unveiled the final product—the Extreme Low Drag-eXpanding bullet, the ELD-X. Combining the Heat Shield Tip with a sophisticated jacket and Hornady’s Interlock design, the ELD-X bullet will be loaded with the best-available powder, primers and cases in the new Precision Hunter line of ammunition. Beyond accomplishing the original mission to develop a match-accurate, all-range hunting bullet, the ELD-X project has laid a foundation for new generations of better tips, better bullets and better practices for testing ammunition and reporting the results.
That’s why I believe the legacy of the ELD-X will extend beyond the product itself. After all, Hornady and other makers aren’t going to stop producing their current tipped bullets, and why should they? There are many excellent and reliable projectiles on the market that are deadly accurate, especially within conventional ranges, and they don’t all wear the iconic red tip.
Still, discovering the effects of velocity-induced heat on current polymer tips will yield important advancements in tip technology and the use of polymers in ammunition. Likewise, the products that the Heat Shield Tip spawns will usher in a new era of ballistic consistency and accuracy, especially beyond the 400-yd. threshold—Hornady has already announced the ELD Match, a non-expanding target bullet that leverages the new tip’s long-range advantage. But the real advancement, in my opinion, will be in how bullets are tested for velocity and aerodynamic characteristics going forward, and the biggest winners will be consumers browsing the ammunition aisle of the local sporting goods store.
The advantages of the Doppler radar over chronographs or acoustic detectors are clear, as are those of the Doppler-produced, full-flight drag coefficients over traditional BCs. The technology removes the need to extrapolate or assume, well, anything. From muzzle to target, the Doppler supplies real data at every distance. Given ammunition consistency, shooters won’t have to predict trajectories, they will be known, and the onus for making a good shot at extended range will shift from the equipment back to the rifleman—where it belongs.
The final step to making this a reality puts a burden on ammunition manufacturers. In order for consumers to make informed decisions about what ammunition will best suit their needs, all ammunition will need to be tested using the best technology, currently Doppler radar. And, to account for myriad shooting conditions encountered during testing, results need to be corrected back to an atmospheric standard. Just as the radar fleshes out the ballistic data, standard conditions with regard to atmospherics (temperature, humidity, etc.) would allow shooters to compare “apples to apples” when ammunition shopping. A bullet or cartridge tested in the Minnesota winter is not going to perform the same way it might during the summer in Arizona; we are shooters, we know this. Standards for testing ammunition and reporting results would level the playing field, eliminate exaggerated or understated data, and allow for direct comparison of ballistic characteristics from load to load and brand to brand. It can be done, it’s already being done, but it’s a practice that I hope will be adopted by the industry at large.
For more information, contact: Hornady Manufacturing Company, 3625 W. Old Potash Highway, Grand Island, NE 68803; (800) 338-3220; hornady.com.